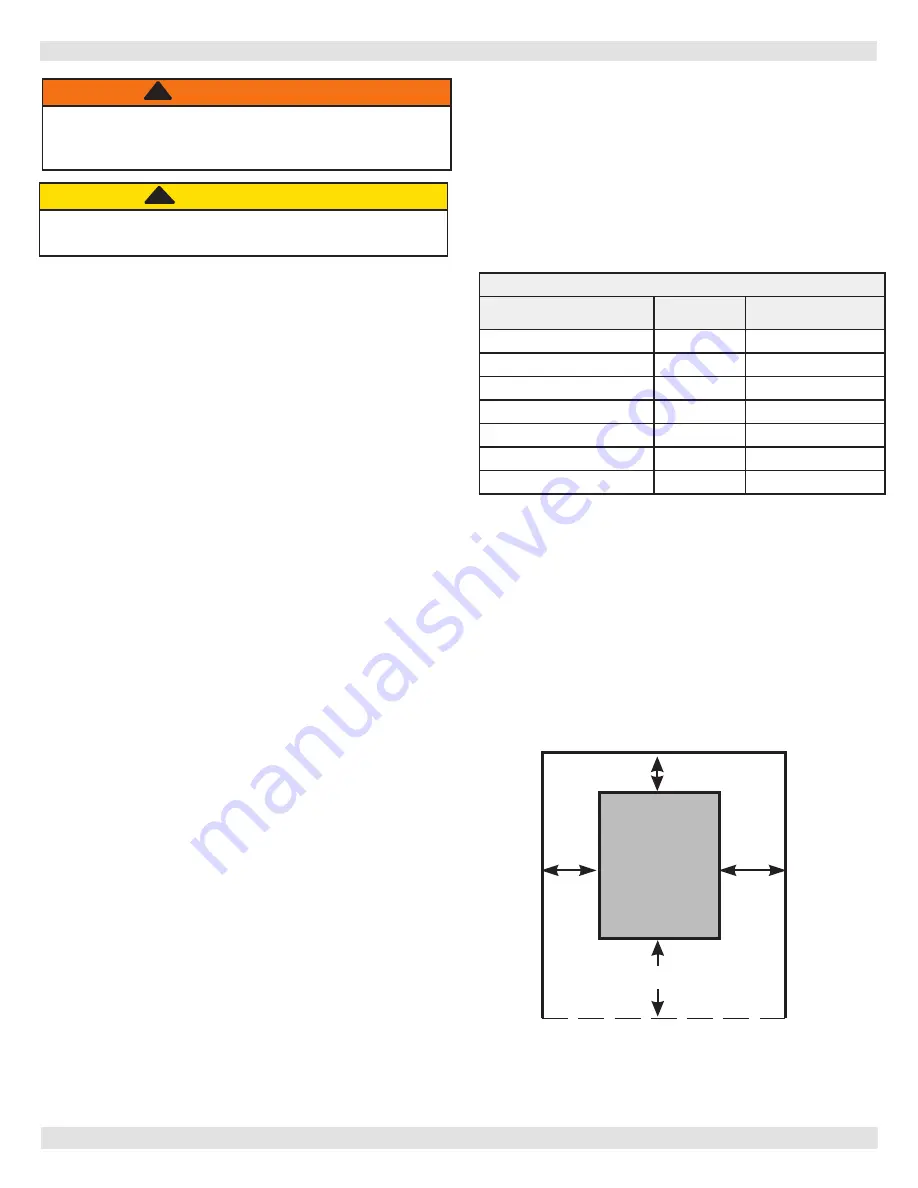
7
3 -LOCATING THE BOILER
Table 2 - MINIMUM CLEARANCE DIMENSIONS
Inches
(mm)
Top
6”
(152mm)
Rear
6”
(152mm)
Control Side
7”
(178mm)
Opposite Side
6”
(152mm)
Front
18”
(457mm)
Flue/Vent Connector
6”
(152mm)
Near Boiler Piping
2”
(51mm)
NOTE: Greater clearances for access should supersede fire
protection clearances.
* Definition of Alcove is three sided space with no wall in
front of boiler. ANSI standard for alcove is 18 inches from
front of appliance to leading edge of side walls as shown
below.
1.
Installation shall conform to the requirements of the
authority having jurisdiction or, in the absence of such
requirements, to the National Fuel Gas Code, ANSI
Z223.1/NFPA 54, and/or Natural Gas and Propane
Installation Code, CAN/CSA B149.1.
2.
Where required by the authority having jurisdiction, the
installation shall conform to the Standard for Controls
and Safety Devices for Automatically fired Boilers,
ANSI/ASME CSD-1.
3.
Boiler series is classified as a Category I. Vent
installation shall be in accordance with "Venting of
Equipment”, of the National Fuel Gas Code, ANSI
Z223.1/NFPA 54, or "Venting Systems and Air Supply
for Appliances," of the Natural Gas and Propane
Installation Code, CAN/CSA B149.1, or applicable
provisions of the local building codes.
4.
Boiler has met safe lighting and other performance
criteria with the gas manifold and control assembly on
the boiler per the latest revision of ANSI Z21.13/CGA
4.9.
5.
Install boiler such that gas ignition system components
are protected from water (dripping, spraying, rain,
etc.) during appliance operation and service, (circulator
replacement, condensate trap, control replacement,
etc.).
6.
Locate boiler on level, solid base as near chimney as
possible and centrally located with respect to heat
distribution system as practical.
7.
Allow 24 inches (610mm) at front and right side for
servicing and cleaning.
8.
When installed in utility room, door should be wide
enough to allow largest boiler part to enter, or to
permit replacement of another appliance such as water
heater.
Minimum Clearances to Combustible
Construction
(as seen from above)
6"
BOILER
18"
6"
Front
7"
Control
Side
9.
FOR INSTALLATION ON NON-COMBUSTIBLE
FLOORS ONLY -
For installation on combustible
flooring special base shall be used. Please refer to
(Combustible Floor Addendum) included in literature
envelope provided with boiler and outlined in
National
Fuel Gas Code
, ANSI Z223.1/NFPA 54.
Do Not Install
Boiler on carpeting.
3.1 Installation Requirements
CAUTION
Boiler weight exceeds 200 pounds (90.7 kg). Do not
lift boiler without assistance.
!
WARNING
Fire hazard. Do not install boiler on combustible
flooring or carpeting. Failure to follow these
instructions could result in death or serious injury.
!
PN 240013090 REV. C [10/01/2021]