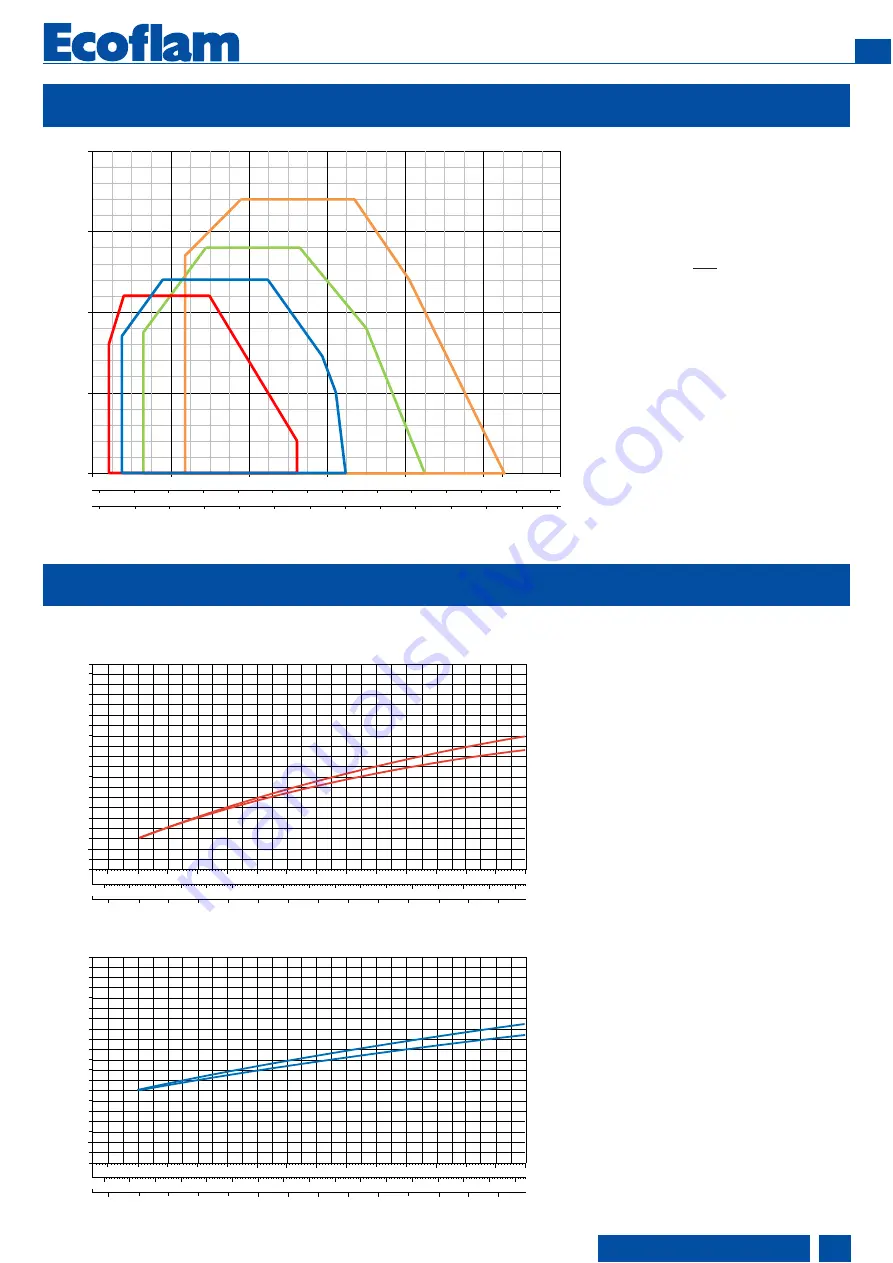
7
www.ecoflamburners.com
EN
420010985900
0
10
20
30
40
2000
4000
6000
8000
10000
12000
14000
2000
4000
6000
8000
10000
12000
14000
200
400
600
800
1000
1200
1400
mbar
kW
kg/h
kcal/h*1000
MAIOR 700.1
MAIOR 1200.1
MAIOR 800.1
MAIOR 1000.1
WORKING DIAGRAMS
TEST BOILER FLAME DIMENSIONS
The burner/boiler matching does not pose
any problem if the boiler is CE type-
approved.
If the burner must be combined with a
boiler that has not been CE type-approved
and/or its combustion chamber dimensions
are clearly smaller than those indicated in
diagram, consult the manufacturer.
The firing rates were set in relation to
special test boilers, according to EN 267
regulations.
The sizes are indicative and dipend on
the configuration, to the combustion
chamber pressure and to the draught.
The values have been taken out from
tests executed with flame tubes.
The dimensions of the flame are made
in test boiler in laboratory without
resistence therefore exists max and
min lenght that take into account the
difference in lenght that comes from the
boiler backpressure.
Example:
Burner thermal output = 8000 kW;
L flame (m) = 5 m (medium value)
D flame (m) = 1 m (medium value)
WARNING:
Some flame modifications
can be done in our FLEXSHOP in the
factory in order to shape the flame and
adapt it to some special boiler
or application.
L (m)
2000
3000
4000
5000
6000
7000
8000
9000
10000
4
5
1000
2000
3000
1000
6
11000
0
2
3
7
8
12000
kW
13000
9
10
11
kg/h
100
200
300
400
500
600
700
800
900
1000
1100
kcal/h
x 1000
4000
5000
6000
7000
8000
9000
10000
11000
12000
13000
14000
15000
14000
15000
16000
17000
1200
1300
1400
Ø (m)
2000
3000
4000
5000
6000
7000
8000
9000
10000
0,6
0,8
1000
2000
3000
1000
1
11000
0
0,2
0,4
1,2
1,4
12000
kW
13000
1,6
1,8
2
kg/h
100
200
300
400
500
600
700
800
900
1000
1100
kcal/h
x 1000
4000
5000
6000
7000
8000
9000
10000
11000
12000
13000
14000
15000
14000
15000
16000
17000
1200
1300
1400
FLAME LENGHT LIGHT OIL BURNERS
FLAME DIAMETER LIGHT OIL BURNERS
Working diagrams
The working diagram shows
burner output as a function of
combustion chamber pressure.
It corresponds to the maximum
values specified by EN 276
measured at the test fire tube.
Boiler efficiency should be
taken into consideration when
selecting the burner.
Calculation of
burner output
QF = Burner output (kW)
QN = Rated boiler output(kW)
η = Boiler efficiency (%)
QF =
QN x 100
η
Summary of Contents for MAIOR P 1000.1 PRE
Page 22: ...22 www ecoflam burners com EN 420010985900 APPENDIX Fluidics nozzle chart...
Page 23: ...23 www ecoflam burners com EN 420010985900 APPENDIX Fluidics nozzle chart...
Page 24: ...24 www ecoflam burners com EN 420010985900 APPENDIX Fluidics nozzle chart...
Page 31: ...31 www ecoflam burners com EN 420010985900 APPENDIX Electrical diagrams...
Page 32: ...32 www ecoflam burners com EN 420010985900 APPENDIX Electrical diagrams...