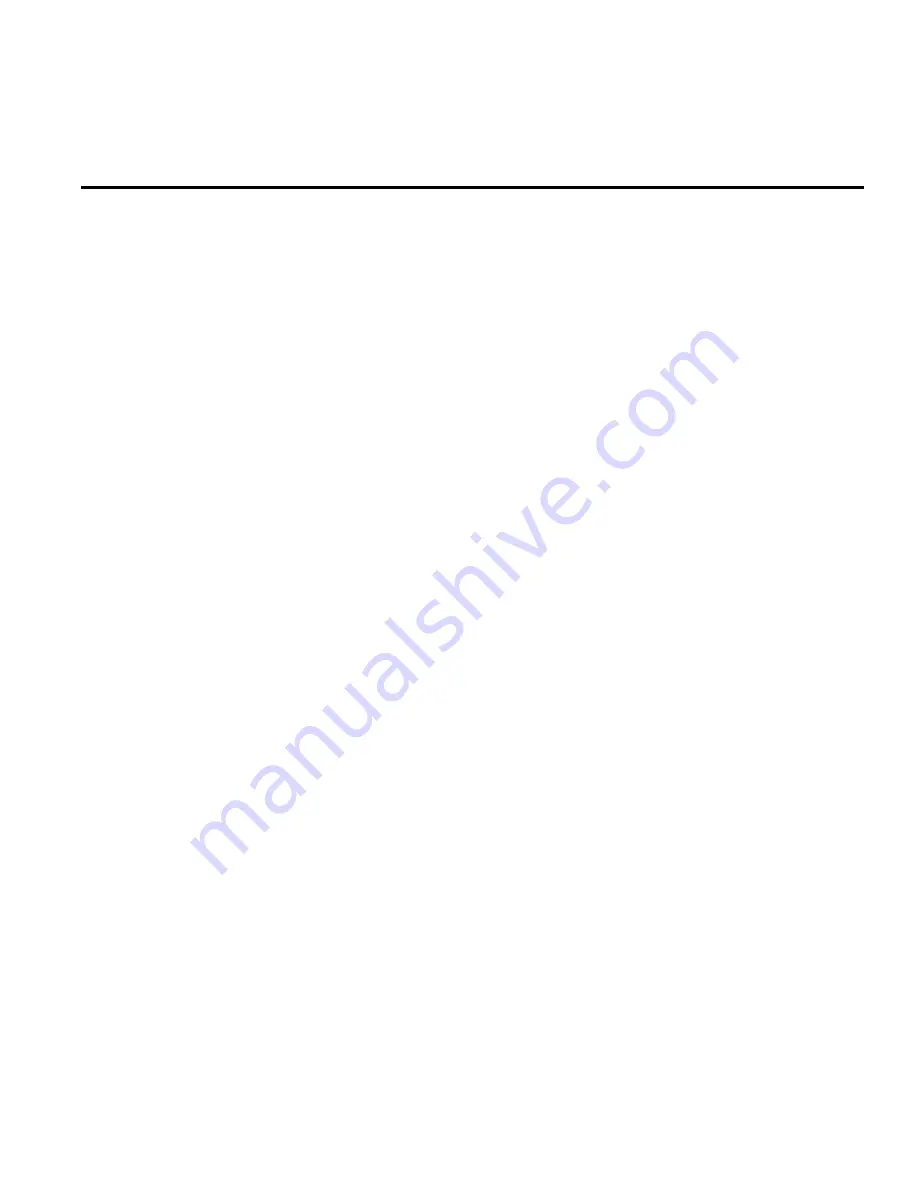
Crary Industries Inc. is pleased to explain the evaporative emission
control system (EECS) warranty on your 2013 equipment. New
equipment must be designed, built and equipped to meet the EPA’s
stringent anti-smog standards. Crary Industries Inc. must warrant the
EECS on your equipment for the period of time listed below provided
there has been no abuse, neglect or improper maintenance of your
equipment.
Your EECS may include parts such as the fuel tank, fuel lines, fuel
caps, vapor hoses, and clamps.
Where a warrantable condition exists, Crary Industries Inc. will repair
your equipment at no cost to you including diagnosis, parts and labor.
MANUFACTURER’S WARRANTY COVERAGE:
This evaporative emission control system is warranted for two years. If
any evaporative emission-related part on your equipment is defective,
the part will be repaired or replaced by Crary Industries Inc.
OWNER’S WARRANTY RESPONSIBILTIES:
As the equipment owner, you are responsible for performance of the
required maintenance listed in your owner’s manual. Crary Industries
Inc. recommends that you retain all receipts covering maintenance on
your equipment, but Crary Industries Inc. cannot deny warranty solely
for the lack of receipts.
As the equipment owner, you should however be aware that Crary
Industries Inc. may deny you warranty coverage if your equipment or
a part has failed due to abuse, neglect, or improper maintenance or
unapproved modifications.
You are responsible for presenting your equipment to Crary Industries
Inc.’s distribution center or service center as soon as the problem
exists. The warranty repairs should be completed in a reasonable
amount of time, not to exceed 30 days. If you have a question regarding
your warranty coverage, you should contact Justin Banyai at 1-701-
282-5520.
GERERAL EMISSIONS WARRANTY COVERAGE:
Crary Industries Inc. warrants to the ultimate purchaser and each
subsequent purchaser that the equipment is:
Designed, built and equipped so as to conform with all applicable
regulations; and
Free from defects in materials and workmanship that cause the failure
of a warranted part to be identical in all material respects to that part as
described in Crary Industries Inc.’s application for certification.
The warranty period begins on the date the equipment is delivered to
an ultimate purchaser or first placed into service. The warranty period is
two years.
Subject to certain conditions and exclusions as stated below, the
warranty on emission-related parts is as follows:
(1)
Any warranted part that is not scheduled for replacement as
required maintenance in the written instructions supplied, is warranted
for the warranty period stated above. If the part fails during the period
of warranty coverage, the part will be repaired or replaced by Crary
Industries Inc. according to subsection (4) below. Any such part
repaired or replaced under warranty will be warranted for the remainder
of the period.
EPA EMISSION CONTROL WARRANTY STATEMENT
YOUR WARRANTY RIGHTS AND OBLIGATIONS
(2)
Any warranted part that is scheduled only for regular
inspection in the written instructions supplied is warranted for the
warranty period stated above. Any such part repaired or replaced under
warranty will be warranted for the remaining warranty period.
(3)
Any warranted part that is scheduled for replacement as
required maintenance in the written instructions supplied is warranted
for the period of time before the first scheduled replacement date for
that part. If the part fails before the first scheduled replacement, the
part will be repaired or replaced by Crary Industries Inc. according
to subsection (4) below. Any such part repaired or replaced under
warranty will be warranted for the remainder of the period prior to the
first scheduled replacement point for the part.
(4)
Repair or replacement of any warranted part under the
warranty provisions herein must be performed at a warranty station at
no charge to the owner.
(5)
Notwithstanding the provisions herein, warranty services
or repairs will be provided at all of our distribution centers that are
franchised to service the subject engines or equipment.
(6)
The equipment owner will not be charged for diagnostic
labor that is directly associated with diagnosis of a defective, emission-
related warranted part, provided that such diagnostic work is performed
at a warranty station.
(7)
Crary Industries Inc. is liable for damages to other engine or
equipment components proximately caused by a failure under warranty
of any warranted part.
(8)
Throughout the equipment warranty period stated above,
Crary Industries Inc. will maintain a supply of warranted parts sufficient
to meet the expected demand for such parts.
(9)
Any replacement part may be used in the performance of any
warranty maintenance or repairs and must be provided without charge
to the owner. Such use will not reduce the warranty obligations of Crary
Industries Inc.
(10)
Add-on or modified parts that are not exempted by the EPA
may not be used. The use of any non-exempted add-on or modified
parts by the ultimate purchaser will be grounds for disallowing a
warranty claim. Crary Industries Inc. will not be liable to warrant failures
of warranted parts caused by the use of a non-exempted add-on or
modified part.
WARRANTED PARTS:
The repair or replacement of any warranted part otherwise eligible for
warranty coverage may be excluded from such warranty coverage
if Crary Industries Inc. demonstrates that the equipment has been
abused, neglected, or improperly maintained, and that such abuse,
neglect, or improper maintenance was the direct cause of the need for
repair or replacement of the part. That notwithstanding, any adjustment
of a component that has a factory installed, and properly operating,
adjustment limiting device is still eligible for warranty coverage. The
following emission warranty parts are covered:
(1)
Fuel Tank
(2)
Fuel Cap
(3)
Fuel Line
(4)
Clamps
(5)
Vapor Hose