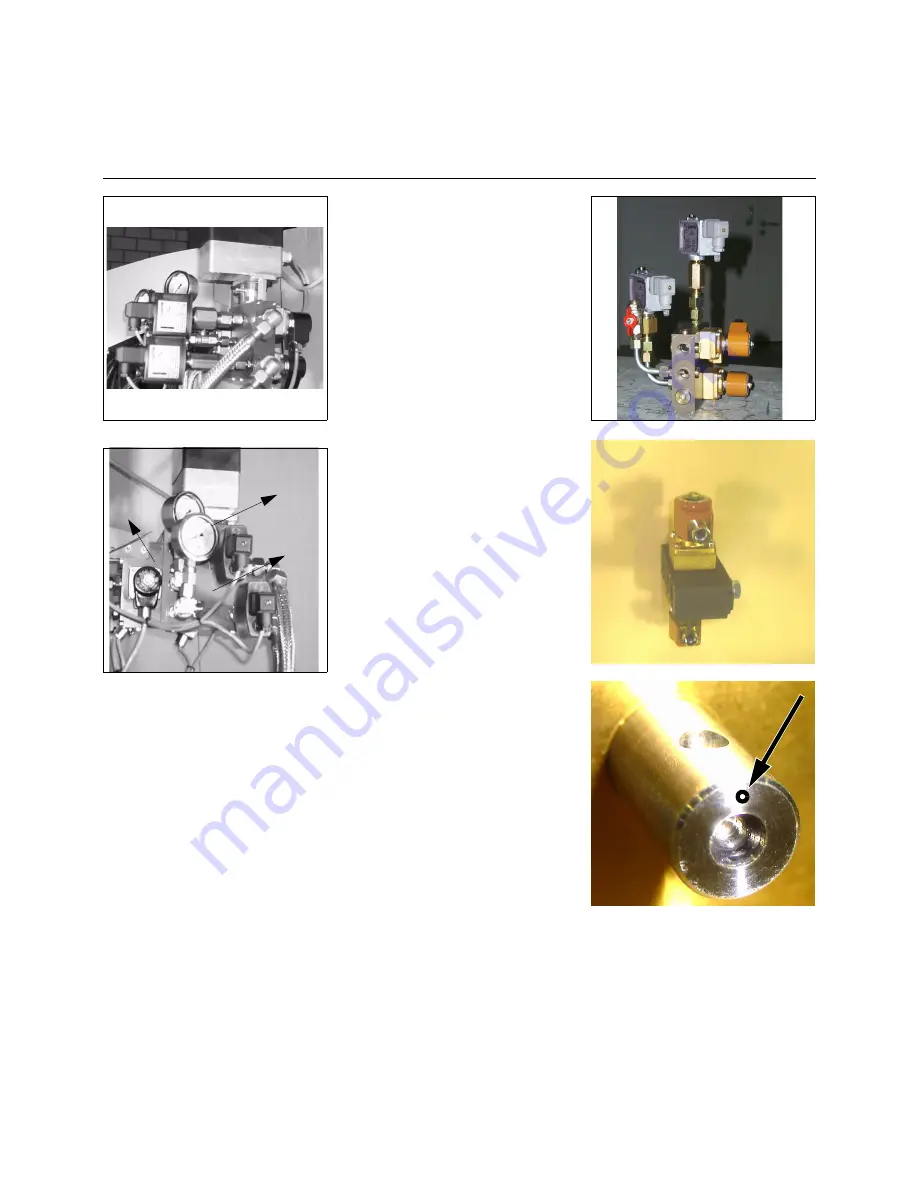
9
Operation
Hydraulic Valves and Instruments Group
The hydraulic valves and instruments
group is an integrated concept that
combines several functions of the
hydraulic systems of burners. Its modu-
lar construction makes it possible to
meet a wide range of requirements and
conditions of installation.
Depending on the level of equipment of
the hydraulic system, oil pressure swit-
ches and
pressure gauges (3)
may be
installed in the supply and return pipes
of the
basic module (1)
. The solenoid
valve in the supply pipe is of servo-assi-
sted type while the return valve is
directly controlled. The solenoids of the
two valves are electrically connected in
series which will prevent one of the val-
ves being opened alone if any of the
solenoids is defective. For the replace-
ment of the solenoid valves during
maintenance work it should be ensured
that the right valve type is installed in
the correct direction of mounting. For
mounting the solenoid valve in the sup-
ply pipe (type 321F2523) it must be
ensured that the direction of flow shown
be a stamped arrow on the valve flange
is the same as the direction of flow of
the oil (from the pump to the nozzle
rod). The solenoid valve in the return
pipe (type 121 F2523) is marked with a
stamped arrow opposite to the direction
of the oil flow from the nozzle rod back
to the pump.The volume flow control
valve installed in the return pipe con-
sists of a bush pressed into the hydrau-
lic valves and instruments group and
locked against torsion and a control
shaft. As the control shaft is turned, the
contoured configuration of the bush and
shaft will change the open cross section
for the oil flowing back and thus vary the
oil return flow rate. Control shafts with
different control contour parameters are
available for adjustment to various oil
nozzle sizes. This concept ensures that
an excellent control characteristic and a
wide control range can be covered for a
great variety of applications. The control
contour parameter is affixed to the con-
trol shaft by means of an electric mar-
ker. The current position of the control
shaft is indicated by the position dis-
play. From the "min." mark (low load of
burner) the control shaft will turn clock-
wise to the "max." mark (full load of bur-
ner). If the control shaft has been
removed during maintenance work care
should be taken when reinstalling it to
ensure the right mounting position of
the control contour by observing the
centre punch mark on the shaft end
face. In the low load position (min.) the
centre punch mark will in any case point
up (12 o'clock position - see figure).
If the hydraulic valves and instruments
group is used in conjunction with nozzle
rods not approved as safety shut-off
valve according to EN 264, an
exten-
sion module
(2)
is available which
incorporates an additional solenoid
valve each in the supply and return
pipes. The extension module is atta-
ched directly to the basic module. The
modules are sealed against each other
by O-rings.
Metal hoses are used for connection
between the hydraulic valves and
instruments group and the nozzle rod.
The hose lines must be protected
against exterior mechanical damage.
The hoses must be positioned and
mounted in accordance with the appli-
cable technical standards. For the
installation care must be taken not to
introduce torsional or buckling stresses
neither by the mounting procedure nor
by movements at a later stage. Speci-
fied bending radii of the hoses must not
be changed.
Basic module
Extension module
Control shaft installation
Complete hydraulic valves and
Instruments group
3
1
2