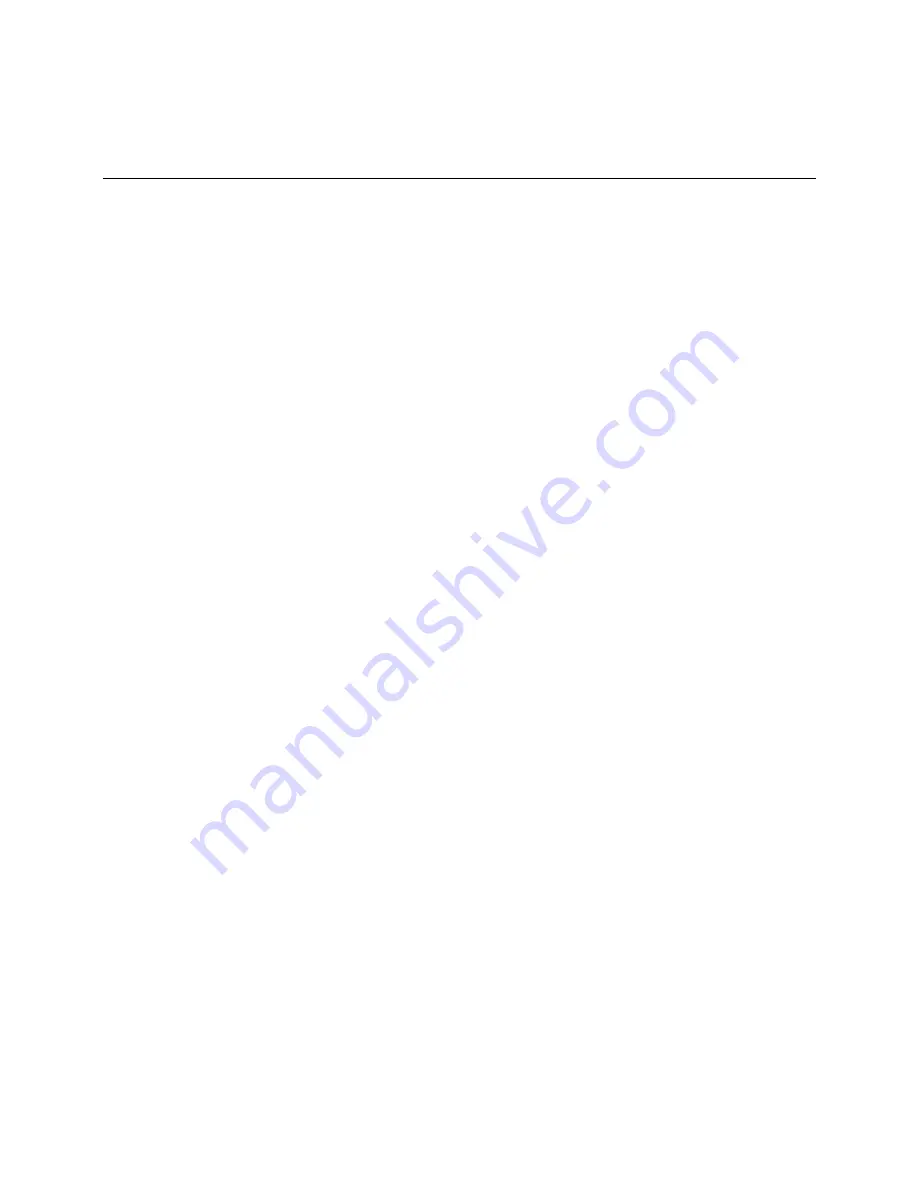
22
Adjusting Instructions
Start-up of Burner Control System Type BCS 300
Flame Detecting System Type FLW 05
Description
The electronic burner control system
type BCS 300 is a programmable auto-
matic firing controller of modular con-
struction with integrated electronic
compound controller. It is designed for
the control and automatic control of oil,
gas and dual-fuel burners of medium to
larger outputs.
The automatic firing controller may be
used for intermittent or continuous
mode of operation and for furnace
systems built according to TRD.
The controller consists of the following
units that communicate via a safety-ori-
ented bus system:
-
burner controller module type
BCS 300 (attached to burner)
-
flame detector module type BCS-
FLW 05 (attached to burner)
-
fuel and air servomotors
-
operating and display unit type
BAM (not required for operation of
furnace system)
The system also incorporates a PID
firing rate controller with standard or
servo-control parameterization capabi-
lity and a valve leak tester.
Technical data:
Operating voltage:
230 V a.c.
Frequency:
50-60 Hz
Power input:
BCS incl. BAM:<15 VA
FLW 05:
<1.5 VA
Back-up fuse:
max. 10 AF
Equipment fuse:
6.3 A slow-blow
0.1 A slow-blow
Permissible ambient temperature:
in operation:
0 - 60 °C
during storage: -20 - 70 °C
Starting the burner control system
NOTE:
The burner control system is
allowed to be started by duly qualified
specialists only. The personnel opera-
ting the system should strictly observe
the applicable instructions for start-up.
Before proceeding with the pro-
gramming of the system make a check
of its wiring (especially for compliance
with the relevant DIN-VDE standards
and the regulations of the local power
supply company).
The parameterization of the automatic
firing controller programs, the valve leak
test and the firing rate adjustment will
be handled from the operating and dis-
play module.
NOTE:
For selecting the automatic con-
troller programs and adjusting the pre-
ventilation times care should be taken to
observe the applicable standards.
The fixed safety time settings are not
allowed to be extended by external swit-
ching operations.
The fuel-air compound curves may be
programmed by means of the operating
and control module or a laptop compu-
ter.
If the compound controller is adjusted
by means of the operating and display
module it will only be possible to correct
the curve point settings.
A completely new curve and the defini-
tion of new curve points can be achie-
ved with the aid of a laptop computer
only.
After the automatic controller programs
have been set it will be possible to
check the inputs and outputs of the bur-
ner control system for proper
functioning via the operating and dis-
play module.
NOTE:
For the tests, all manual fuel
shut-off valves must be kept in closed
position in any case.
The compound modules are provided
with a basic curve when delivered ex
works. This may be changed by means
of the operating and control module to
adjust it to the local conditions. For this
purpose, it is possible to correct the
damper positions for the 10 index points
in the range from 10, 20, 30, etc. to 100.
Flame detecting system
The flame detector module type FLW 05
is used in conjunction with the burner
control system.
The following flame sensors may be
connected to the flame detector
module:
-
QRA 2
-
QRA 53/55
-
RAR 7/8
-
ionization electrode
-
any flame detector with contact
output
The sensor to be used will be selected
by appropriate programming in the bur-
ner control system. The type of sensor
used will depend on the burner opera-
ting mode (continuous or intermittent).
The flame boosters integrated in the
flame detector will be checked for pro-
per operation at an interval of 90
seconds in continuous mode.
Flame detectors with contact output
must if run in continuous mode be intrin-
sically safe because only the parts of
the BCS flame detector are checked for
safe operation.
The intensity of the flame signals (UV
sensor, light sensor, ionization elec-
trode) is evaluated in the burner control
system and indicated on the operating
and display module.
This allows an exact orientation of the
flame sensors.
It is not possible to measure the flame
intensity by means of instruments.
The flame sensors must be checked for
accumulation of dirt at regular intervals.
Take care that the sensor window is
kept free of dust all the time.
The flame intensity display may be used
as an indicator for the dirt accumulation
load.
If the situation cannot be remedied by
cleaning it will be necessary to replace
the flame sensor.