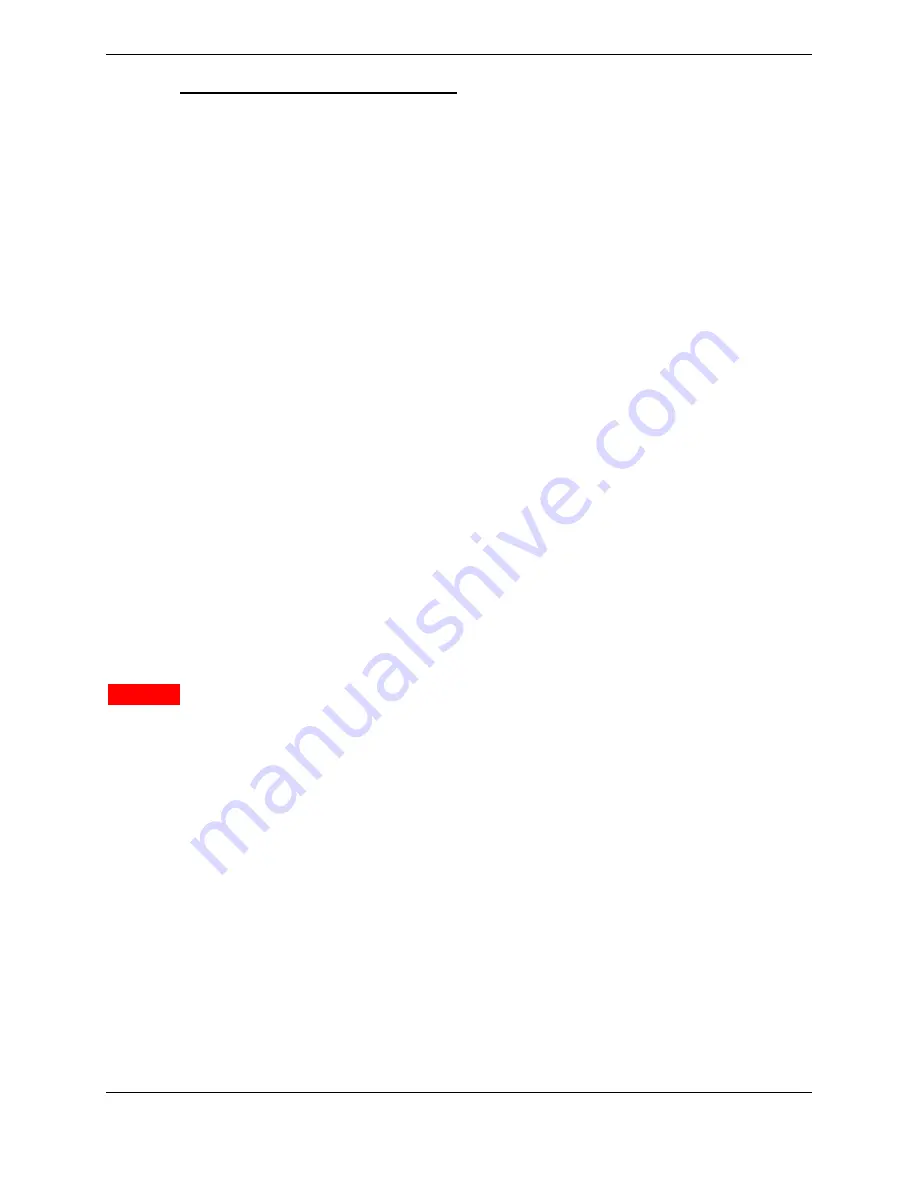
Page 7
This document is proprietary. No disclosure, reproduction or use of any part thereof may be made without the expressed written
permission of Ebbco Inc. or its subsidiaries.
Section 3:
System Installation and Start-Up
3.1 Installation Procedure
1. Upon receipt of the system, carefully check each component against the bill of materials to ensure
that everything has been received with the system. If anything is missing or damaged, immediately
contact the freight company to file the appropriate claim.
2. Remove system from wooden 2 x 4 undercarriage using suitable materials handling equipment.
3. Install catcher tank sweeper package as shown in the sweeper layout drawing provided.
4. Install the gate valve to the suction port on the catcher tank.
5. Install the gate valve to the discharge port on the catcher tank.
6. Install hose barbs into the suction and discharge gate valves.
7. Close the suction and discharge valves.
8. Fill the catcher tank with water.
9. Position system next to waterjet machine as discussed with Ebbco Inc. Anchor system to floor as
necessary.
10. Using the black suction hose and clamps provided in the installation kit, connect the suction barb on
the catcher tank to the suction barb on the garnet removal system.
11. Using the black discharge hose and clamps provided in the installation kit, connect the discharge
barb on the catcher tank to the discharge barb on the garnet removal system.
12. Place abrasive bag hopper under purge outlet. Connect decant line to fitting provided on hopper.
13. Connect the overflow piping from the 3" port on the abrasive bag hopper to the garnet pump column.
14. Have a qualified industrial electrician connect the 3 phase electrical power to the control panel as per
electrical drawing. (230vac/3 ph/60Hz)
3.2 Start Up Procedure:
1. Check the pump suction basket for debris.
2. Open the suction and discharge valves on the catcher tank.
3. Ensure that the catcher tank is full of water.
4. Check pump for correct rotation (clockwise as viewed from the top of the motor) by bumping the HOA
switch, located on the main electrical panel.
5. The pump motor on the filtration system has been synchronized at the factory if the pump motor is
running in reverse have a qualified electrician swap over one of the in coming line powers at electrical
panel.
6. Turn the HOA switch to the HAND position.
Warning!
If the filtration system dose not prime after 5 seconds, stop the system. Try three more times
and if the system still will not prime call the Ebbco service department 1-586-716-5151
7. Check separator inlet and outlet pressure gauges to ensure differential pressure is between 4 and 12
psi.
Summary of Contents for GRS-0250-B-CC
Page 17: ......
Page 18: ......
Page 19: ......
Page 20: ......
Page 21: ......
Page 22: ......
Page 23: ......
Page 24: ......
Page 25: ......
Page 26: ......
Page 27: ......
Page 28: ......
Page 29: ......
Page 30: ......
Page 31: ......
Page 32: ......
Page 37: ......
Page 38: ......
Page 39: ......
Page 40: ......