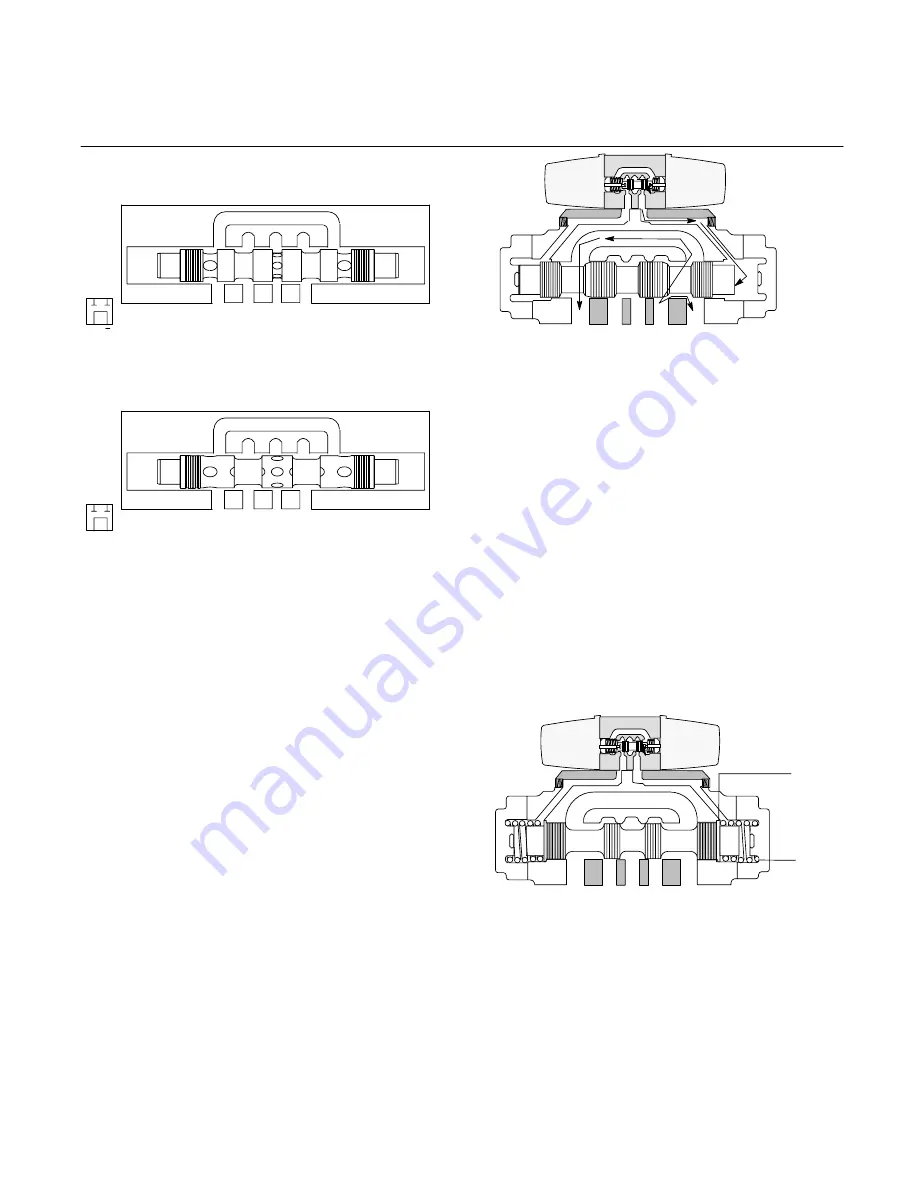
9
A. Type ‘4’ spool allows oil to circulate freely from port
(P) to port (T) in the center position. Ports (A) and (B) are
blocked to the workload.
T
A
P
B
A B
P T
Closed Crossover, Pressure to ‘‘T’’
with ‘‘A’’ & ‘‘B’’ Blocked
B. Type ‘8’ spool is designed similar to type ‘4’ spool.
Ports (P) and (T) are connected in the center position.
However, ports (A) and (B) are momentarily open during
spool crossover.
T
A
P
B
A B
P T
Tandem, Open Crossover, Pressure to ‘‘T’’
with ‘‘A’’ & ‘‘B’’ Blocked
C. Methods of Spool Control, Main Stage
1. Remote Pilot Source: Main stage valves are available
for use with a remote source. This means that the valve is
shifted from a remote pressure source by other valves in
the logic circuit.
2. Integral Pilot Valve: The integral pilot type two stage valve
is a very common valve used in the field today. Two stage
valves allow large volumes of fluid to be switched to and from
an actuator with minimum power required for control.
Reference figures 3 through 7 shown in the following section.
D. Main Stage Spool Position
Main stage spools are positioned within the valve by special
arrangements. The four basic main stage positioning
arrangements are: no spring-floating, spring centered, spring
offset and pressure centered.
The following paragraphs (1 through 4) describe these
arrangements. A fifth function can be obtained by the use of a
detent pilot valve. This function is described in paragraph five.
1. No Spring-Floating: When centering springs are omitted
from the main stage spool, the spool is said to be floating. If
control pressure is removed, a floating spool can move from
its last position under the influence of gravity or tank line
pressure. This must be considered during the design of the
system. Units with floating type spools have the model code
letter omitted. Figure 3 illustrates floating spool positioning in
a two-stage valve.
Figure 3. No Springs, Floating Model
Solenoid ‘‘A’’ is energized and shifts pilot spool to the
right. This opens pressure to pilot port ‘‘A’’ and the main
stage spool.
When solenoid ‘‘A’’ is energized, the main stage spool
will shift left. Flow from P
³
A and B
³
T is obtained.
Main stage spool will stay in this position until solenoid
‘‘B’’ is energized, but may float to other positions with
both solenoids de-energized.
1.
2.
3.
A
B
T
A
P
B
T
P
B
A
2. Spring Centered: A spring and washer arrangement is
used on both ends of the main stage spool in the spring
centered configuration. If control pressure is removed from a
spring centered spool, the valve will go to the center position
due to spring force. Two configurations of a two-stage spring
centered valve can be obtained, a type ‘B’ and a type ‘C’. If
one solenoid is used on a spring centered pilot valve, the
model code is identified with the letter ‘B’. When two
solenoids are used, the model code is identified with the
letter ‘C’. Figure 4 illustrates spool positioning of a two-stage
spring centered ‘C’ model.
Figure 4. Spring Centered ‘‘C’’ Model
Solenoids are de-energized. Pilot spool is in center
position due to spring force.
Main stage springs and washers keep main stage
spool at center position. Flow is A & B
³
T with
³
P
blocked.
When solenoid ‘‘A’’ is energized, the pilot spool will
shift to the right, causing the main stage spool to
shift left. Flow would then be P
³
A and B
³
T.
1.
2.
Main
Stage
Spring
Main
Stage
Washer
T
A
P
B
T
A
B
P
B
A