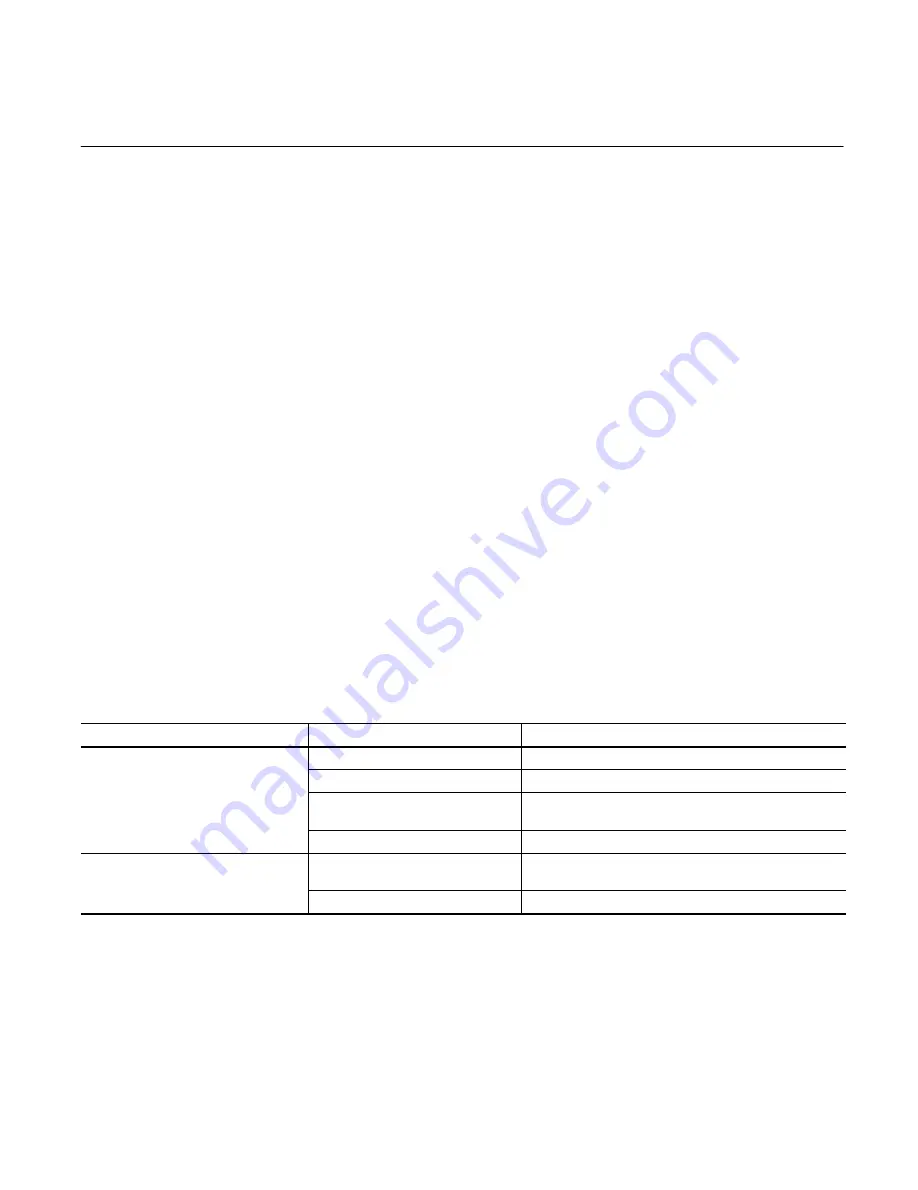
18
Section VII - Service, Inspection & Maintenance
A. Service Tools
No special tools are required to service this valve series.
B. Inspection
Periodic inspection of the fluid condition and tube or piping
connections can save time consuming breakdown and
unnecessary parts replacement. the following should be
checked regularly.
1. All hydraulic connections must be kept tight. A loose
connection in a pressure line will permit the fluid to leak
out. If the fluid level becomes so low as to uncover the
inlet pipe opening in the reservoir, extensive damage to
the system can result. Loose connections also permit air
to be drawn into the system resulting in a noisy and/or
erratic operation.
2. Clean fluid is the best insurance for long service life.
Therefore, check the reservoir periodically for dirt and
other contaminants. If the fluid becomes contaminated,
flush the entire system and add new fluid.
3. Filter elements should also be checked periodically. A
clogged filter element will cause higher pressure drops
within the system.
4. Air bubbles in the reservoir can ruin the valve and other
components. If bubbles are seen, locate the source of
the air and seal the leak.
C. Adding Fluid to the System
When hydraulic fluid is added to replenish the system, pour it
through a fine wire screen (200 mesh or finer). When
applicable, pump the fluid through a 10 micron filter. DO
NOT use a cloth to strain the fluid or lint may enter the
system.
D. Adjustments
No periodic adjustments are required other than normal
system maintenance,
E. Replacement Parts
Reliable operation throughout the specified operating range
is assured only if genuine Vickers parts are used.
Sophisticated design processes and material are used in the
manufacture of our parts. Substitutions may result in early
failure. Part numbers are shown in the parts and service
drawings listed in Table 1.
F. Product Life
The service life of this product is dependent upon
environment, duty cycle, operating parameters and system
cleanliness. Since these parameters vary from application to
application, the ultimate user must determine and establish
the periodic maintenance required to maximize life and
detect potential component failure.
G. Troubleshooting
Table 4 lists the common difficulties experienced with
directional valves and systems. It also indicates the probable
causes and remedies for each of the troubles listed.
Also remember that many apparent failures may actually be
the failure of other parts of the system. The cause of
improper operation is best diagnosed with adequate testing
equipment and a thorough understanding of the complete
hydraulic system.
TROUBLE
PROBABLE CAUSE
REMEDY
Valve spool fails to move
Dirt in system
Disassemble, clean and flush.
Solenoids inoperative
Check electrical source and solenoids.
Improper assembly
Check proper assembly. Refer to appropriate figure
and assembly procedure.
Improper installation connections
Check installation drawings
Valve produces undesirable response
Improper valve assembly
Improper installation connections
Checks parts drawing and installation drawing for
proper assembly and installation connections
Solenoid wiring reversed
Reverse connections to the solenoids
Table 4. Troubleshooting Chart