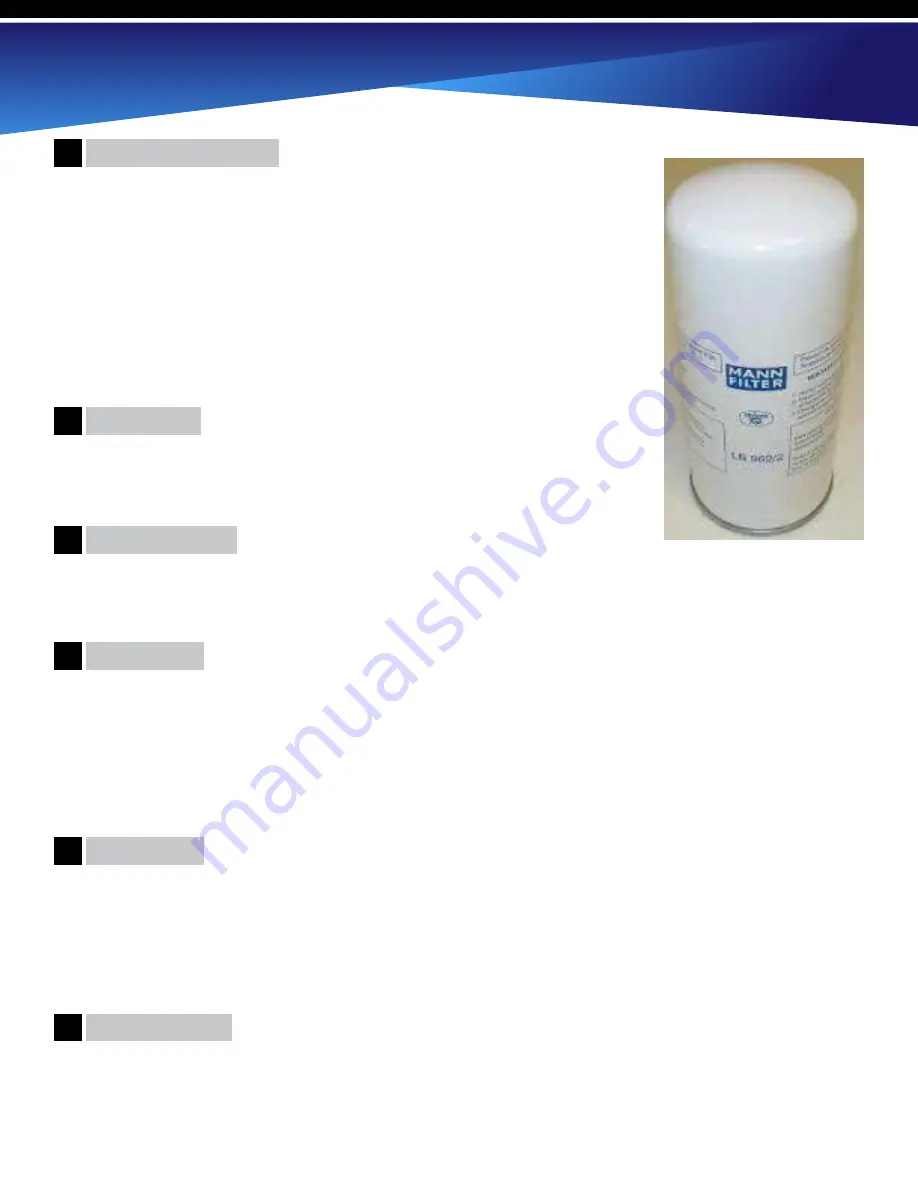
Operating Instructions
25
Air/Oil Separator Filter
Safety Valve
Blow Down Valve
Check Valve
After Cooler
Air Storage Tank
11
12
13
14
15
16
During the process of air compression from pump, air and oil are mixed together
to lubricate, seal and cool compressor rotors. This air and oil is transferred to air/
oil separator tank and then the air/oil separator filter removes oil mist from the
compressed air. The filter core is made of multiple-layer fine glass fibers. The filter
reduces the oil particle size and can lower content to less than 3 PPM. During
normal operation, the air/oil separator filter can be used for about 4000 hours or
annually, whichever comes first. Refer to the computer controls of the compressor
to monitor operating time and remember to reset maintenance timer when filter is
replaced. There is an automatic alarm that can be set to remind operator of service
times
The ASME certified safety valve on the air/oil separator tank is set to open when
the pressure exceeds 175 PSI (12.1 bar). NEVER attempt to operate machine
without ASME safety valve.
The air flows through the check valve then enters the after cooler. The fan on the air cooled after cooler radiator
draws in ambient air and blows it through the radiator cores to reduce heat in the compressed air and lubricating oil
exhausted from the rotary screw pump. The heat absorbed in the radiator cores is discharged from the screw cabinet
because of the cooling fan and generally reduces air temperature by 60°F (15°C). If ambient air temperature exceeds
112°F (45°C), the system may overheat. It is important to operate the compressor in a well ventilated area for the
cooling process to be effective.
(optional, not shown)
The air storage tank can serve as cushion to keep output pressure relatively stable. It can
also reduce operating temperature, remove moisture content, provide cleaner air and reduce the load of the dryer. A
larger tank also reduces the cycling of the suction valve. As a guideline, for every CFM the compressor produces, a
minimum of 1.2 gal. of air storage is needed.
The blow down valve is a two-way valve normally open. When the machine is shut down or the compressor is
unloaded, the vent valve opens and relieves pressure in the air/oil separator tank to ensure the compressor will not be
started under load.
A minimum pressure check valve is installed after the air oil separator filter. The starting pressure is set at over 43.5
PSI (3 bar). The functions of the minimum pressure valve are as follows:
a.
Actuates oil lubrication of the air end.
b.
Regulates air flow through the air separator filter to prevent damage to the separator filter element. Air flow
begins when pressure in the air / oil separator tank reaches 43.5 PSI (3 bar).
c.
Prevents back flow from the air receiver tank into the air / oil separator tank. This component serves as a
built-in check valve. No additional check valve is needed for installation.
Summary of Contents for PRS0100001
Page 1: ...Operating Instructions 1...
Page 39: ...Operating Instructions 39...
Page 40: ...Eaton Compressor Rotary Screw Compressor 40...
Page 41: ...Operating Instructions 41...