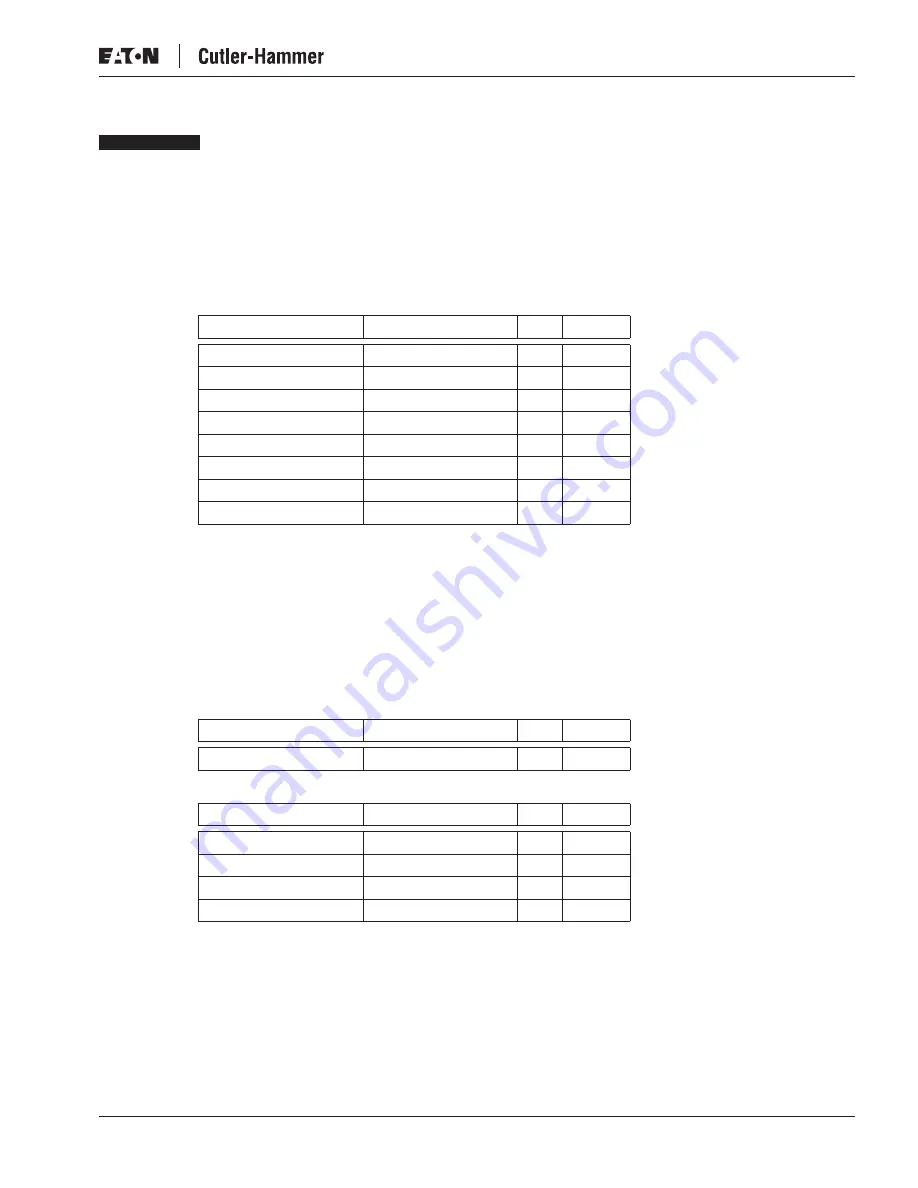
LonWorks Option Board User Manual
MN04003008E
For more information visit:
www.eatonelectrical.com
A-1
April 2004
Appendix A — Process Data
Process Data OUT
The nodes can read the drive’s actual values using process data variables.
Basic, Standard, Local/Remote, Multi-Step, PID control and Pump and Fan control
applications use process data as follows:
Table A-1: Process Data OUT Values
The Multipurpose Control Application has a selector parameter for every Process Data. The
monitoring values and drive parameters can be selected using the ID number (see
9000X AF
Drive Application Manual
tables for monitoring values and parameters). Default selections
are as in
Table A-1
.
Process Data IN
Process Data is used with All-in-One applications as follows:
Table A-2: Basic, Standard, Local/Remote and
Multi-Step Applications
Table A-3: Multipurpose Control Application
Data
Value
Unit
Scale
Process data OUT 1
Output Frequency
Hz
0.01 Hz
Process data OUT 2
Motor Speed
rpm
1 rpm
Process data OUT 3
Motor Current
A
0.1A
Process data OUT 4
Motor Torque
%
0.1%
Process data OUT 5
Motor Power
%
0.1%
Process data OUT 6
Motor Voltage
V
0.1 V
Process data OUT 7
DC link voltage
V
1V
Process data OUT 8
Active Fault Code
—
—
Data
Value
Unit
Step
PD1 – PD8
Not used
—
—
Data
Value
Unit
Step
Process Data IN1
Torque Reference
%
0.1%
Process Data IN2
Free Analog INPUT
%
0.01%
Process Data IN3
Adjust Input
%
0.01%
PD3 – PD8
Not Used
—
—