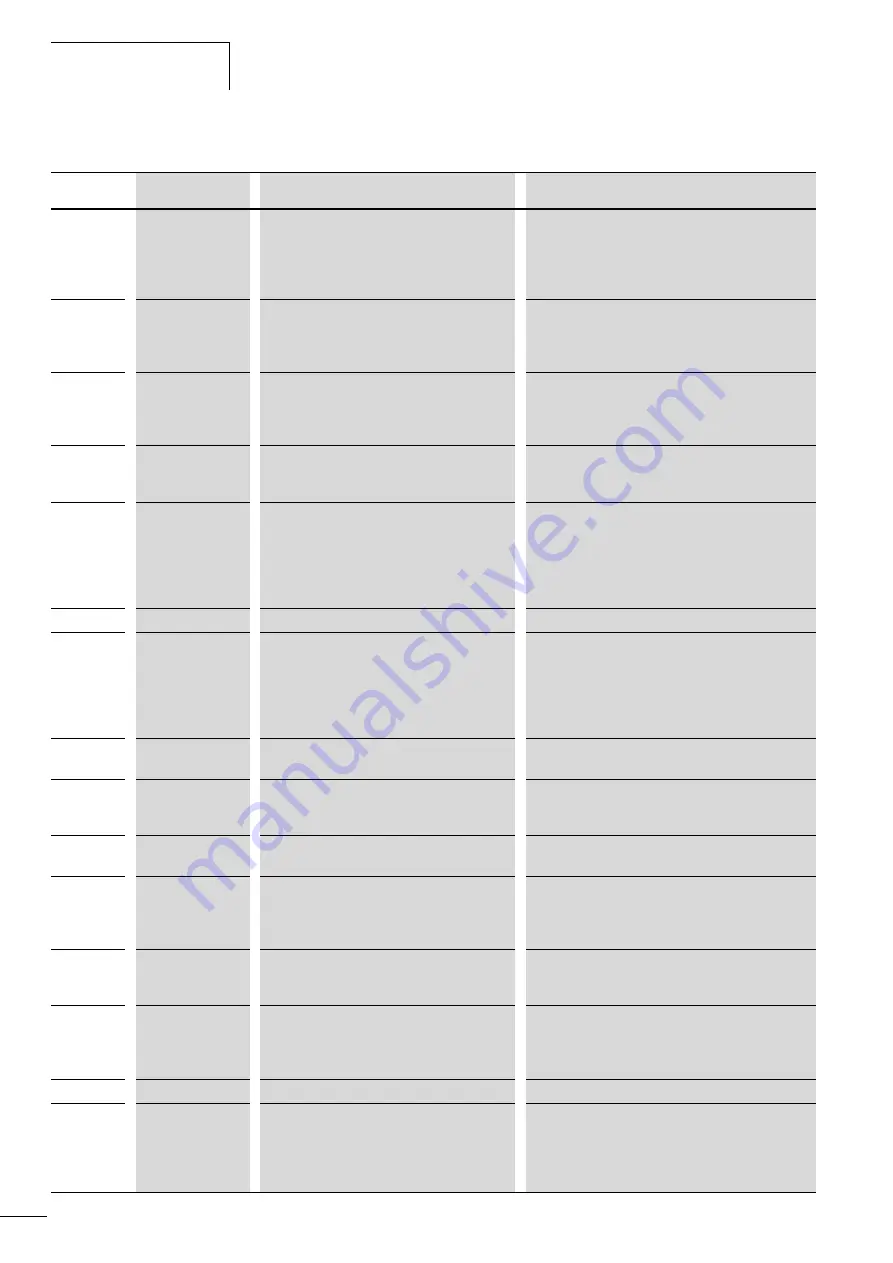
Error and Warning Messages
04/10 MN04020001Z-EN
64
Table 5:
List of fault messages (F) and warning messages (AL)
Display
Designation
Possible cause
Instructions
01
Overcurrent
• The frequency inverter has detected an exces-
sive current (> 4 × I
N
) in the motor cable.
• Sudden load increase.
• Short-circuit in motor cable.
• inadequate motor.
• Check the load
• Check the motor size
• Check the cable
(
h
parameter P6.6)
02
Overvoltage
• The DC intermediate circuit voltage has
exceeded the internal safety limit.
• the delay time is too short.
• high overvoltage peaks in line power
increase braking time
03
Ground fault
• An additional leakage current was detected
when starting by means of a current
measurement.
• Insulation fault in the cables or in the motor
Check the motor cable and the motor
08
System fault
• CPU error message
• Internal communication fault.
Reset error: Switch mains voltage off and on (Restart).
If the fault occurs again, please contact your closest
Moeller representative.
09
Undervoltage
The DC intermediate circuit voltage has exceeded
the internal safety limit.
Probable cause:
• the supply voltage is too low,
• internal device fault,
• Power failure.
• If a brief power failure takes place, reset the fault and
restart the frequency inverter.
• Check the supply voltage. If it is OK, there is an internal
fault.
If this is the case, please contact your closest Moeller
representative.
13
Under-temperature
The IGBT switch temperature is below -10 °C.
Check the ambient temperature
14
Overtemperature
The IGBT switch temperature is above 120 °C.
An excessive temperature warning is issued if the
IGBT switch temperature goes above 110 °C.
• Make sure that there is an unobstructed flow of
cooling air
• Check the ambient temperature
• Make sure that the switching frequency is not too high
in relation to the ambient temperature and to the
motor load
15
Motor blocked
The motor blocking protection mechanism has
been triggered.
Check the motor
16
Motor over-tempera-
ture
The frequency inverter's motor temperature
model has detected motor overheating. The motor
is overloaded.
Decrease the motor load.
If the motor is not overloaded, check the temperature
model parameter.
17
Motor underload
Motor idle, connection to load machine inter-
rupted (e.g. torn drive belt).
This function must be activated at P8.5. The overload
message is set at P8.12 and P8.13.
22
EEPROM checksum
error
• Error when storing parameters.
• Malfunction,
• Component fault,
• Error in microprocessor monitoring.
Please contact your closest Moeller representative.
25
Watchdog
• Error in microprocessor monitoring.
• Malfunction,
• Component fault.
Reset the fault and restart
If the fault occurs again, please contact your closest
Moeller representative.
27
Back EMF
Electromotive force
The voltage induced in the motor with the rotation
is greater than the output voltage of the frequency
inverter.
• The rotation energy is greater than the braking energy.
• Lengthen deceleration times.
• Switch on brake chopper and braking resistor.
• Use higher rated frequency inverters.
35
Application error
The application is not working.
Please contact your closest Moeller representative.
50
Live zero error
(Analog input)
Monitored zero point (4 mA, 2 V
h
Parameter P2.1)
• Current less than 4 mA, voltage less than 2 V.
• Signal cable interrupted,
• The signal source is faulty.
Check the analog setpoint circuit and current and voltage
source (
h
Parameters P8.10).
Summary of Contents for M-Max series
Page 8: ...04 10 MN04020001Z EN 4...
Page 12: ...04 10 MN04020001Z EN 8...
Page 58: ...04 10 MN04020001Z EN 54...
Page 66: ...04 10 MN04020001Z EN 62...
Page 138: ...04 10 MN04020001Z EN 134...
Page 150: ...04 10 MN04020001Z EN 146...
Page 196: ...04 10 MN04020001Z EN 192...