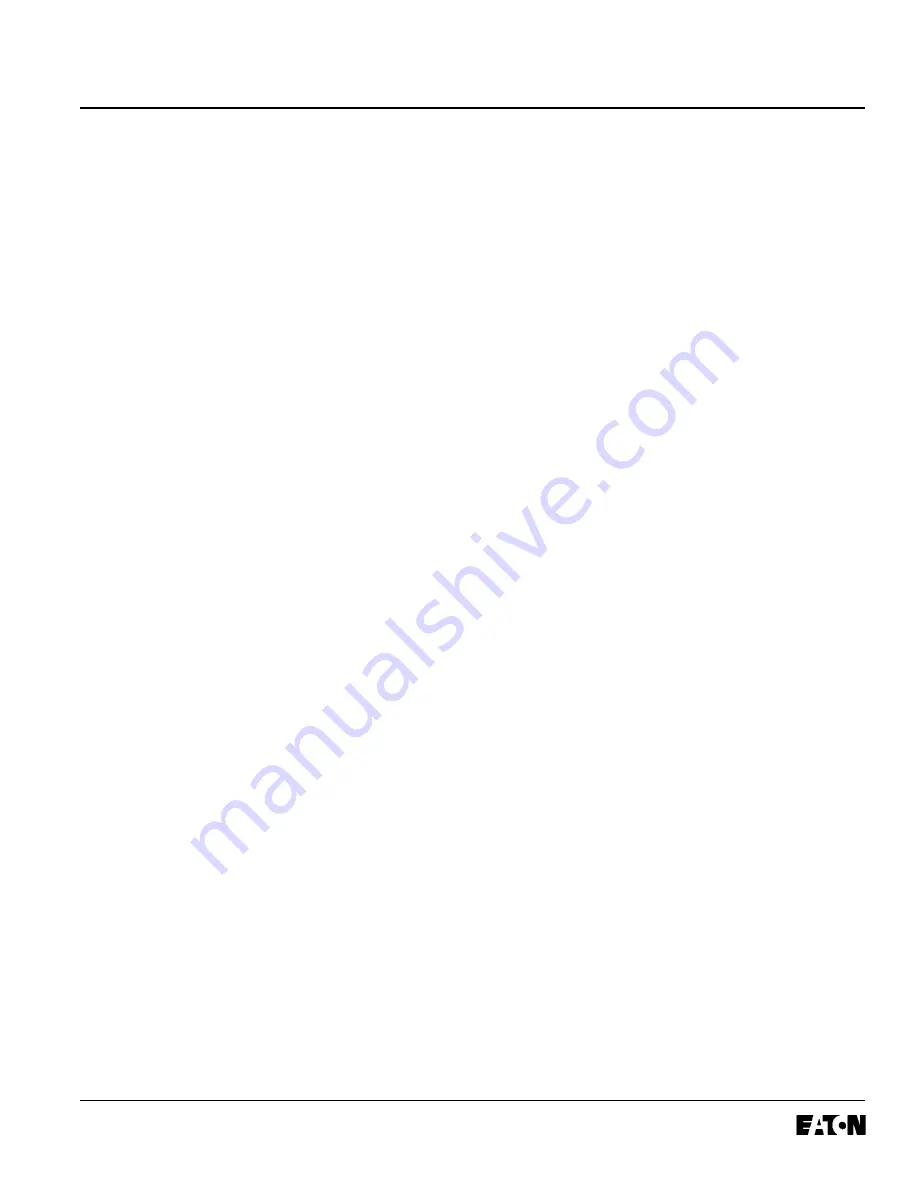
I.B. 17555C
Effective November 1999
Page 13
Test Pushbutton (Yellow)
The selected test operation is initiated by pressing and
releasing the Test pushbutton.
Select Settings Pushbutton (Blue)
In the program mode of operation, the Select Settings
pushbutton is used to step to the next setpoint by press-
ing and releasing the pushbutton. This pushbutton steps
forward. To step back, the Select Settings pushbutton can
be pressed and held, while pressing and releasing the
Lower pushbutton.
Raise/Lower Pushbutton (White)
The Raise and Lower pushbuttons are used during the
program and test modes to increase or decrease the
value of the displayed setpoint. The Lower pushbutton
also serves a dual function in conjunction with the Select
Settings pushbutton, as described under Select Settings
Pushbutton.
Save Settings Pushbutton (Blue)
While in the program mode, selected setpoints can be
saved by depressing and releasing the Save Settings
pushbutton. Settings can be saved individually or one
time as a group. If the Save Settings pushbutton is not
used, the previous setpoints will remain when the pro-
gram mode is exited.
View Settings Pushbutton (Blue)
The View Settings pushbutton is functional only when the
unit is in the normal operating mode, not the program or
test modes. It functions to display the unit’s set-points,
including the phase and ground current transformer ratio
selected via programming. This software version of the
DT3000 will be displayed after the ground ct ratio setting.
The software version will appear in the RMS Amperes
display window and the letters “SVER” will appear in the
Settings display window.
Select Pushbutton (White)
The Select pushbutton is used to step between any of the
eight current values that are displayed in the RMS
Amperes window. The eight currents are IA, IB, IC, IG, IA
ampere demand, lB ampere demand, IC ampere
demand, and IG ampere demand. Stepping with this
pushbutton is in the sequence just given. The currents
displayed are the present RMS values; the ampere
demand currents are the averaged RMS values sensed
over a 5 minute period of time. The demand value is the
largest 5 minute average measured since the amp
demand was last reset.
LEDs: LEDs are used to indicate a number of functions,
operations and/or warnings. Many of the LEDs used pro-
vide different indication messages. The specific message
is determined by the color and a constant on or blinking
operation. Several of the LEDs are bi-colored and can be
lit green or red.
Operational LED
The Operational LED at the top of the relay should be
green and blink on for approximately one second and
then off for one second. This indicates that the relay is
functioning properly in its normal operation mode. If this
LED is blinking red, it indicates the relay may need repro-
gramming. If this LED is lit in any color shade other than
a definite green or red, or if it is not blinking at all, an
internal problem has been detected requiring replace-
ment of the relay.
High Load LED
The High Load LED will blink green when high load set-
tings are being selected in the program mode. In the
operational or test modes, the High Load LED will blink
red when a load current of 85% or above the inverse time
overcurrent phase pick-up setting is reached. If the load
current remains at 85% or above the inverse time over-
current phase pickup setting for the time interval setting,
the LED will change to steady red at the end of the time
interval. Whenever the load current drops below the 85%
level, the timer will reset and the LED will turn off.
Communication Trip LED
This LED, will be continuous red when the breaker has
been tripped by the master computer via INCOM. The
LED will turn off when the Reset pushbutton is pressed or
the circuit breaker is reclosed.
Curve Shape LED
This LED will blink green when the slope setpoint is dis-
played in the Settings/Test Time/Trip Cause window while
in the program mode. When the curve shape set-point is
being viewed in the unit’s normal operating mode, this
LED will be a continuous green.
Time Overcurrent Setting LED
This LED is bi-colored. While in the program mode, the
LED will blink green when the inverse time overcurrent
pickup setpoint is displayed in the Settings/Test Time/Trip
Cause window. It will be a continuous green when the
inverse time overcurrent pickup setpoint is being viewed
in the unit’s normal operating mode. The LED will blink
red whenever the load current exceeds the inverse time
overcurrent pickup setpoint. If the relay trips on inverse
time overcurrent, the LED will be continuous red.
Inverse Time Overcurrent Time LED
This LED will blink green when the LED time overcurrent
time setpoint is displayed in the Settings/Test Time/Trip
Cause window while in the program mode. When the
time multiplier is being viewed in the unit’s normal operat-
ing mode, the LED is continuous green.
Summary of Contents for Cutler-Hammer Digitrip 3000
Page 18: ...I B 17555C Effective November 1999 Page 12 Fig 2 1 Typical Communications Wiring Diagram...
Page 27: ...I B 17555C Effective November 1999 Page 21 Fig 3 1 Digitrip 3000 Typical Wiring Diagram...
Page 36: ...I B 17555C Effective November 1999 Page 30 Fig 3 11 Local Programming Sequence Flow Chart...
Page 37: ...I B 17555C Effective November 1999 Page 31...
Page 52: ...I B 17555C Effective November 1999 Page 46 Fig 7 5 Short Delay Phase Curves SC 5394 92B...
Page 54: ...I B 17555C Effective November 1999 Page 48 Fig 7 7 Instantaneous Curves SC 5396 92B...
Page 59: ...I B 17555C Effective November 1999 Page 53 Fig 7 12 Short Delay Ground Curves SC 5403 92B...
Page 60: ...I B 17555C Effective November 1999 Page 54 Fig 7 13 ANSI Moderately Inverse Curves SC 6685 96...
Page 61: ...I B 17555C Effective November 1999 Page 55 Fig 7 14 ANSI Very Inverse Curves SC 6686 96...
Page 62: ...I B 17555C Effective November 1999 Page 56 Fig 7 15 ANSI Extremely Inverse Curves SC 6687 96...
Page 63: ...I B 17555C Effective November 1999 Page 57 Fig 7 16 IEC A Moderately Inverse Curves SC 6688 96...
Page 64: ...I B 17555C Effective November 1999 Page 58 Fig 7 17 IEC B Very Inverse Curves SC 6689 96...
Page 65: ...I B 17555C Effective November 1999 Page 59 Fig 7 18 IEC C Extremely Inverse Curves SC 6690 96...
Page 66: ...I B 17555C Effective November 1999 Page 60 Fig 7 19 IEC D Flat Curves SC 6691 96...
Page 68: ...I B 17555C Effective November 1999 Page 62...
Page 73: ...I B 17555C Effective November 1999 Page A5 Fig A 7 DT3001 Typical Wiring Diagram...
Page 76: ...I B 17555C Effective November 1999 Page A8...
Page 81: ...I B 17555C Effective November 1999 Page B5 Fig B 2 Digitrip 3010 3020 Dimensions Inches...
Page 83: ...I B 17555C Effective November 1999 Page B7 Fig B 3 Digitrip 3010 3020 Typical Wiring Diagram...
Page 89: ...I B 17555C Effective November 1999 Page B13...
Page 90: ...I B 17555C Effective November 1999 Page B14...