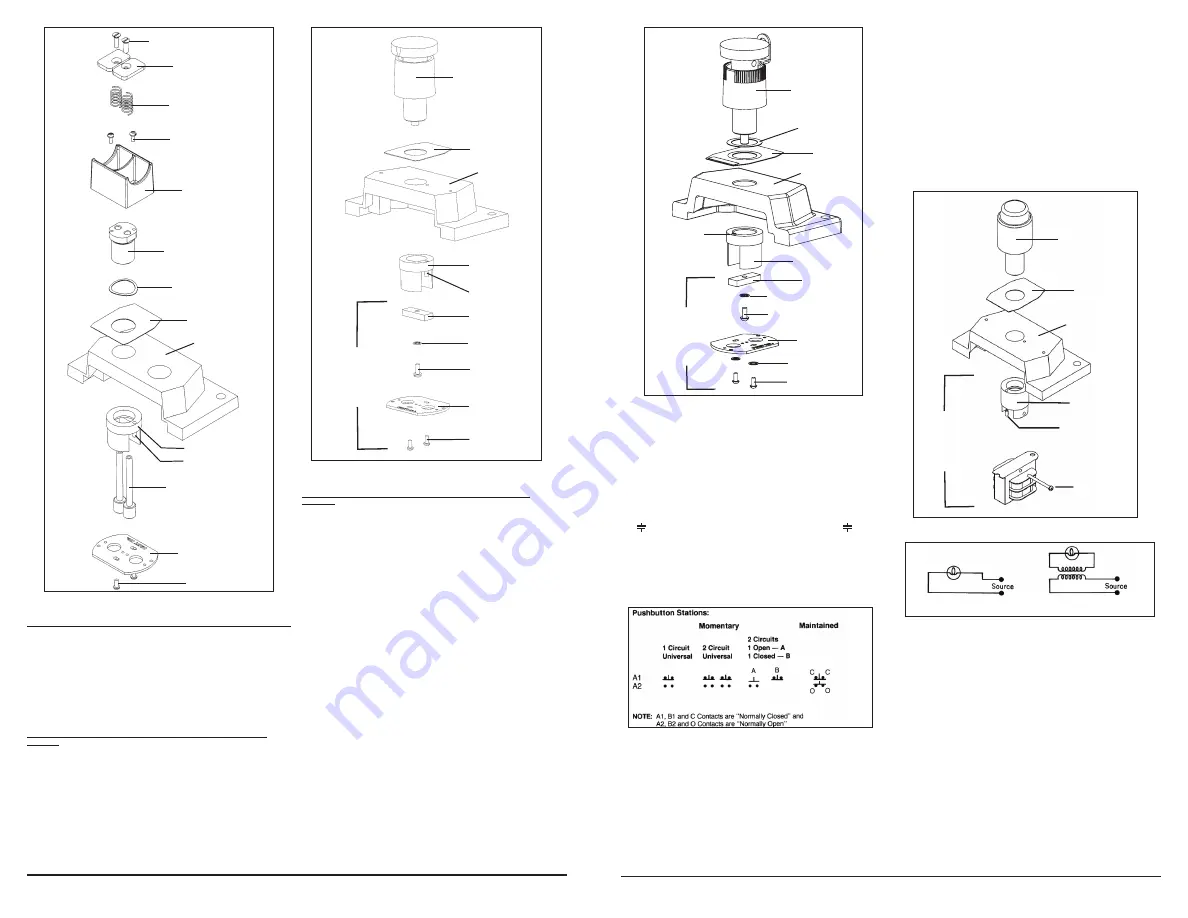
IF 1418 • 02/15
Copyright © 2015, Eaton’s Crouse-Hinds Business
Page 3
IF 1418 • 02/15
Copyright © 2015, Eaton’s Crouse-Hinds Business
Page 4
Momentary mushroom head pushbutton with one contact block
• Install pushbutton sub-assembly to the front side of the cover
by threading it down tight to the cover in the desired location.
Use a DL legend plate if required as noted in ASSEMBLY OF
PUSHBUTTONS.
• Fasten the mounting block to the inside of the cover. Orient
the mounting block so that the contact block is in the
desired position as shown in Figure 2. This step will allow
the contact block to be in the proper position. Tighten the
set-screw thereby locking the pushbutton assembly to the
cover, see Figure 6. Tighten the set-screw thereby locking the
pushbutton assembly to the cover.
• Assemble the necessary contact block per instructions below.
Momentary mushroom head pushbutton with two contact
blocks
• Install pushbutton sub-assembly to the front side of the cover
by threading it down tight to the cover in the desired location.
Use a DL legend plate if required as noted in ASSEMBLY OF
PUSHBUTTONS section.
• Fasten the mounting block to the inside of the cover. Orient
the mounting block so that the contact blocks will be in the
desired position, see Figure 2. Tighten the set-screw thereby
locking the pushbutton assembly to the cover, see Figure 6.
Using the one #6-32 x 5/16 pan head screw and lock washer,
fasten the double contact block actuator to the plunger of
the pushbutton operator assembly. Next, fasten the mounting
plate to the mounting block using the two #4-40 x 1/4 pan
head screws provided.
• Assemble the necessary contact blocks per instructions in
INSTALLATION OF CONTACT BLOCK section.
Maintained mushroom head pushbutton with contact
block(s)
• Referring to Figure 7, install pushbutton sub-assembly
including lockout tab to the front side of the cover by
threading it down tight to the cover in the desired location.
Orient this assembly so that the lockout tab allows a hasp
of the lock to not interfere with an adjoining device. Use
a DL legend plate if required as noted in ASSEMBLY OF
PUSHBUTTONS.
• This step will allow the contact block(s) to be in the proper
position. Fasten the mounting block to the pushbutton sub
assembly on the inside of the cover. If using one contact
block (operator part number DEV11-S769), orient the
mounting block so that the two drilled and tapped mounting
holes are parallel to the long side of the cover. If two contact
blocks (operator part number DEV12-S769) are to be used,
orient the contact block mounting screws so that the two
drilled and tapped mounting holes are perpendicular to the
long side of the cover. Tighten the setscrew using a 1/16”
Allen wrench thereby locking the pushbutton assembly to the
cover, see Figure 7. For DEV12-S769 only, using #6-32 screw
and lock washer fasten double contact block actuator to
operator plunger. The countersunk hole is designed to accept
this screw head. Fasten mounting plate to mounting block
using two #4-40 screws and washers per Figure 7.
• Assemble the necessary contact block(s) per instructions in
INSTALLATION OF CONTACT BLOCK section.
Figure 5. Assembly of Double Pushbutton Operator
Spring Washer
Legend plate
Bearing
Pushbutton Guard
Pushbutton Button
#6 - 32 x 3/8 countersunk screw
Spring
#5 - 40 x 3/16 screw
Cover
(cut-away shown)
Mounting block
1/16” hex head set screw
Plunger
Mounting plate
#4 – 40 x 1/4 screw
• Note the mounting block may need to be backed off 1/2 turn
to ensure proper operation of contact blocks.
INSTALLATION OF CONTACT BLOCK
(Catalog Number ESWP126)
Install the required number of contact blocks to the mounting
block or mounting plate.
The field wiring terminals on the contact block are marked.
The , and “O” indicates normally open contacts; and
and “C” indicates normally closed contacts of the contact block.
The lugs on the contact block are provided with binding head
screw terminals.
• Strip the insulation on each conductor wire back 3/8”.
• Use a slotted or Phillips head screwdriver to loosen the field
wiring terminal screws the required 3 or 4 turns.
• Insert the bare wire conductor(s) on either side of the terminal
screw(s), under the terminal clamp(s) and securely tighten the
screw(s).
Note
: Do Not exceed 15 in. lbs. of torque.
ASSEMBLY OF PILOT LIgHTS
(INCLUDINg TrANSFOrMErS)
Select the DL legend plates with proper markings or marking
windows. Orient them horizontally on the cover as desired.
Note a marking window is provided for field marking customer’s
specific terms. Assemble the pilot light assembly through the
legend plate and onto the cover. Tighten the pilot light assembly
to the cover until it bottoms out on the thread. Use the ¾ - 20
lock nut on the inside of the cover to secure the pilot light to the
cover. See Figure 9.
If using a transformer do NOT use the ¾ - 20 lock nut. Fasten
the mounting block to the pilot light assembly from the inside
of the cover. Orient the mounting block so that the transformer
does not interfere with an adjoining device, as shown in Figure
2. Tighten the set-screw thereby locking the pushbutton
assembly to the cover, see Figure 9. Mount the transformer to
the mounting block using the mounting screw and lock washer.
Connect both wire leads of the pilot light to the secondary side
of the transformer using its white wires. Safely insulate each of
these connections by use of wire nuts. The primary side of the
transformer (black wires) is to be connected to the power supply.
See Figure 10 for wiring diagram of pilot light.
Note that one of the holes in the mounting block is tapped
to accept the mounting screw. With the lock washer on the
mounting screw, insert mounting screw first into untapped hole.
Test wiring for correctness with continuity checks and also for
unwanted grounds with an insulation resistance tester.
Carefully assemble cover assembly to the back box with the
cover screws. Check the tightness of the cover screws to ensure
that the cover assembly is securely fastened.
SELECTOr SWITCH
• Referring to Figure 11, install bearing / shaft sub-assembly to
the front side of the cover by threading it down tight to the
cover in the desired location. Use a DL legend plate if required
as noted in ASSEMBLY OF PUSHBUTTONS.
• This step will allow the contact block(s) to be in the proper
position. Fasten the mounting block to the bearing / shaft sub
assembly on the inside of the cover. Tighten the setscrew
using a 1/16” Allen wrench thereby locking the mounting
block to the cover. Orient the mounting plate on cam module
assembly so that the two flat sides are parallel with the long
side of the cover. Then, slide operator module assembly onto
shaft. Fasten the cam module assembly to the cover using
#6-32 lockwashers and screws.
• Assemble the necessary contact block(s) per instructions in
INSTALLATION OF CONTACT BLOCK section.
• Orient the knob / lock tab assembly so that the indicating
mark points to the desired position for full travel for both 2 and
3 position selector switches. Tighten #4-40 screw to fasten
knob / lock tab assembly in this proper position.
• Referring to Figure 12, test wiring for correctness with
continuity checks and also for unwanted grounds with an
insulation resistance tester.
• Carefully assemble cover assembly to the device body with
the cover screws. Check the tightness of the cover screws to
ensure that the cover assembly is securely fastened.
Figure 6. Assembly of Momentary Mushroom Head
Pushbutton Operator
Mushroom head
pushbutton operator
Legend plate
Cover
(cut-away shown)
Mounting block
1/16” hex head
set screw
Double contact
block actuator
Lock washer
#6 – 32 screw
Mounting Plate
#4 – 40 x 1/4 screw
Material
used only
with double
contact
block
arrangement
Figure 7. Assembly of Maintained Mushroom Head
Pushbutton Operator
Mushroom head
pushbutton operator
assembly
Spring Washer
Legend plate
Cover
(cut-away shown)
Mounting block
1/16” hex head
set screw
Double contact
block actuator
Lock washer
#6 – 32 screw
Mounting Plate
#4 Lock Washers
#4 – 40 x 1/4 screw
Material used
only with
double
contact
block
arrangement
(e.g. DEV12-S769
Figure 8. Wiring Diagram for Pushbutton Stations
Figure 9. Assembly of Pilot Light (Including Transformers)
Legend plate
Cover
(cut-away shown)
Mounting Screw
and Washer
Mounting block
Set Screw
Pilot Light Assembly
Material used only
with transformer.
Standard 120
VAC pilot light uses
3/4-20 lock nut with
a set screw (not
shown).
Figure 10. Wiring Diagram for Pilot Lights
(Including Transformers)
Pilot Lights:
Nominal 120V