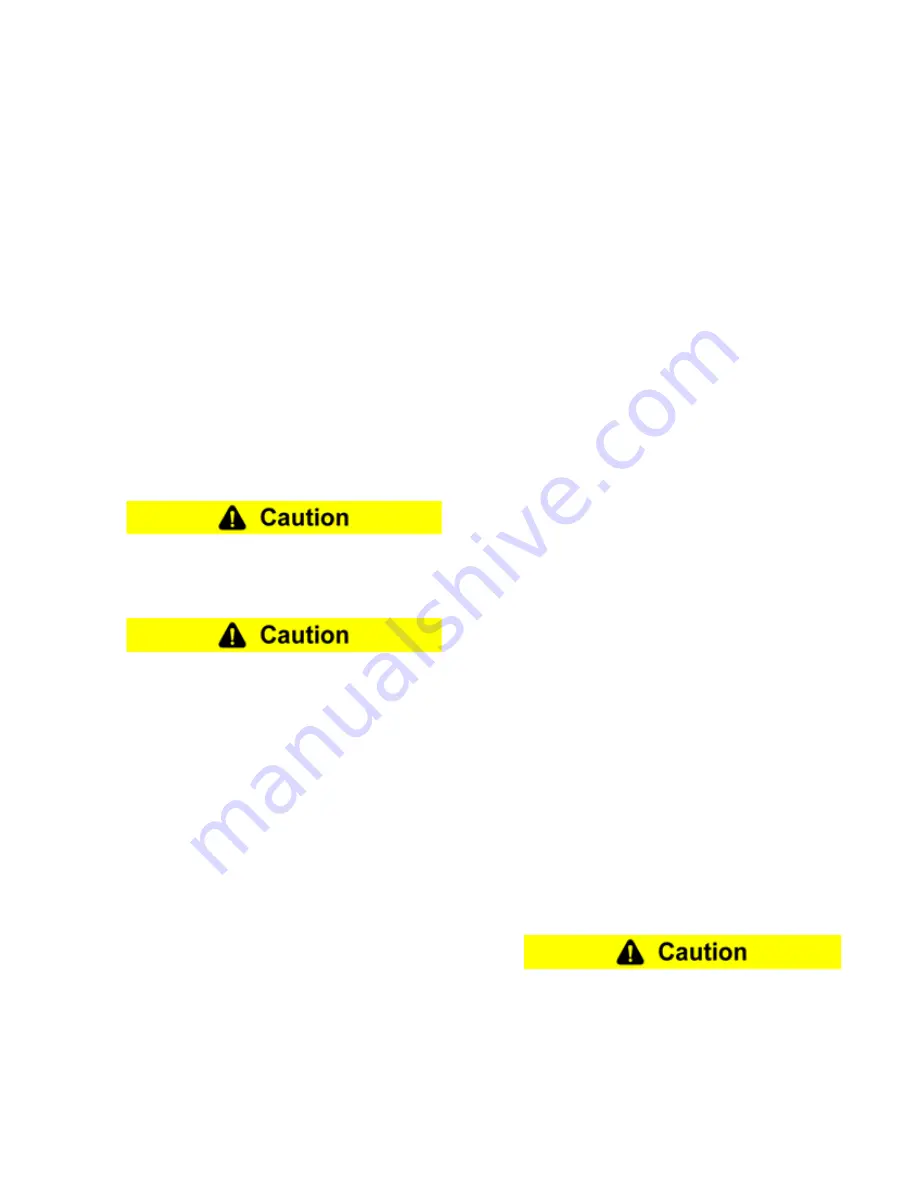
WCB11070 (PDF FORMAT)
23
©
Copyright Eaton Corp. 2007, All Rights reserved.
4.9
Assembly Procedures
Note :
Friction discs and water jackets (mounting
flange, end plate, and reaction plate- if applicable)
should be assembled per the appropriate mainte-
nance procedures prior to final assembly of the ten-
sioner.
4.9.1
Position the mounting flange (1) on a flat, level sur-
face, mounting face down.
4.9.2
Install the studs (6) into the mounting flange. The stud
end with the shorter length of threads is to be assem-
bled into the mounting flange. Clean the stud end to
be assembled by applying Loctite Locquic
®
Primer
Grade "T" to the threads. After the threads have dried,
apply Loctite
®
#271 on the threads to be assembled
and insert the stud completely into the threaded hole
in the mounting flange so that the installed end is flush
or slightly recessed inside the face of mounting flange.
See
Figure 1
. Using a machinists square as a refer-
ence, hold the stud in position so that it remains per-
pendicular to the machined surface of the mounting
flange until the Loctite
®
has cured. Repeat for the
remaining studs.
Loctite Locquic
®
Primer Grade "T" contains
harmful vapors. Refer to the product label and
follow proper safety precautions.
The end of the stud must not extend past the
mounting surface of the mounting flange.
4.9.3
Install the appropriate number of wear spacers (29)
and clamp tubes (12) over the studs.
4.9.4
Place a friction disc assembly onto the mounting
flange. Center the friction disc.
4.9.5
For sizes 8, 14 and 18, place a release spring (34)
over every other clamp tube. For sizes 24, 36 and 48,
install a release spring over every clamp tube. For sin-
gle disc WCB2 tensioners, proceed to Section 4.9.9.
4.9.6
Noting the location of the water inlets in the mounting
flange, lift the reaction plate (30) into position, align
the water inlets with those in the mounting flange, and
slide the reaction plate over the studs and clamp
tubes.
4.9.7
For sizes 8, 14 and 18, place a release spring (34)
over every other clamp tube. For sizes 24, 36 and 48,
install a release spring over every clamp tube.
4.9.8
Place friction disc assembly onto the reaction plate.
Repeat the sequence of steps 4.9.5 through 4.9.8
until all friction discs, reaction plates and release
springs are assembled.
4.9.9
Noting the location of the water inlets in the mounting
flange, lift the pressure plate (13) into position and
align the water inlets with those in the mounting
flange. Slide the pressure plate over the studs and
clamp tubes.
4.9.10 Thoroughly clean the seal grooves in the piston (33)
and apply a thin, even coat of Dow Corning 55 O-ring
lubricant to the piston seal grooves and chamfer on
the piston, the sealing surfaces in the cylinder (19),
and the seals (21) (23).
4.9.11 Install the new seals in the grooves in the piston, not-
ing the orientation of the seal lips. See
Figure 19
4.9.12 Position the cylinder on a flat level surface so that the
pressure cavity faces upward.
4.9.13 Carefully place the piston onto the cylinder with the
chamfered edge of the piston facing downward, taking
special care to avoid damaging the seal lips.
4.9.14 Gradually apply an evenly distributed force to press
the piston into the cylinder being sure not to cock the
piston which may damage the sealing surfaces or
seals. The use of 'C-clamps' may assist with the
assembly process.
4.9.15 Lift the cylinder/piston assembly into position and slide
it over the studs, noting the orientation of the ports on
the cylinder face.
4.9.16 Lubricate the threads on the end of the studs with 30
wt. oil or anti-seizing compound and assemble the
washers (17) and locknuts (18).
4.9.17 Tighten the locknuts, ONE TURN AT A TIME and in an
alternating (crosswise) pattern until the cylinder is
seated firmly against the clamp tubes. Torque the
locknuts to the appropriate value. See Table 4.
The locknuts (18) must be tightened gradually
to prevent damage to the tensioner compo-
nents.
4.9.18 Re-install the tensioner per Section 2.0