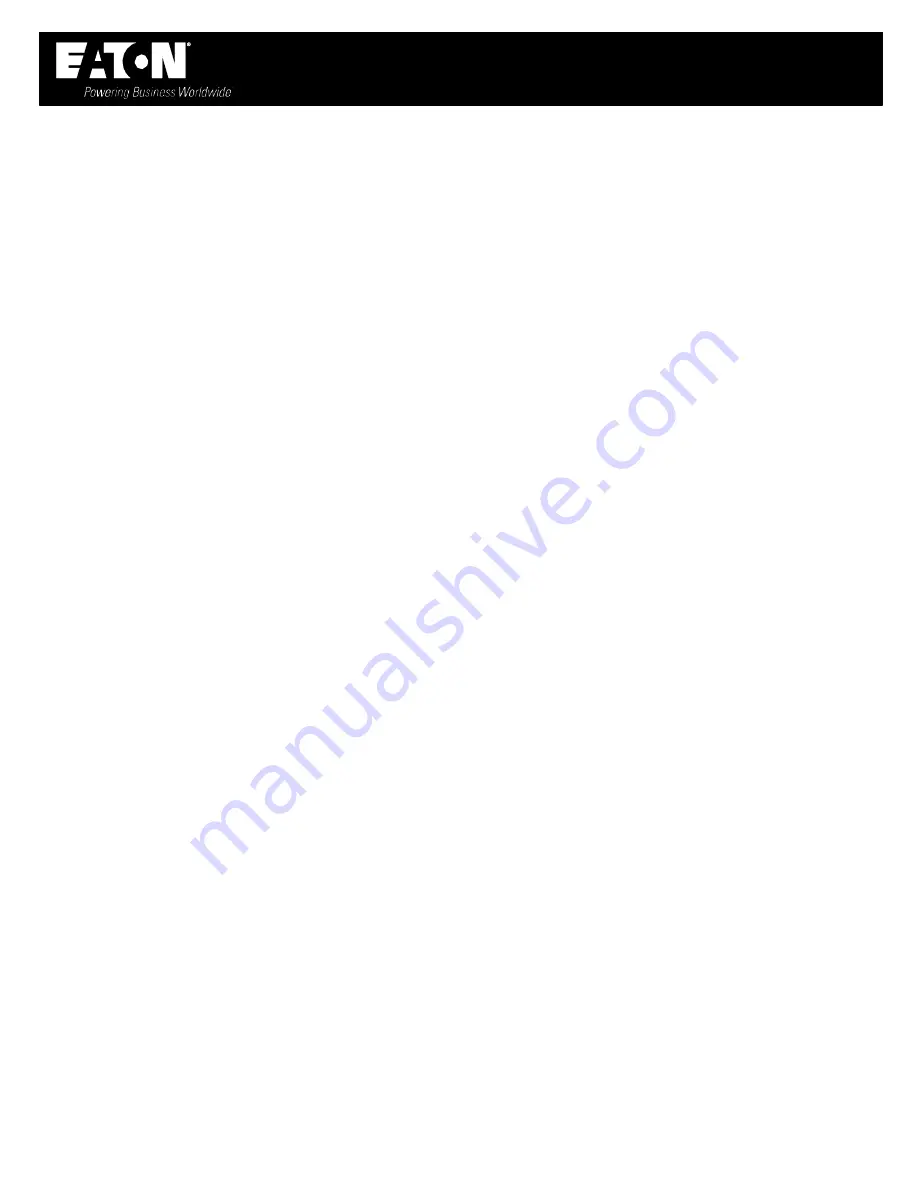
Installation, Operation & Maintenance Manual
Control Panels for Automatic Self-Cleaning Strainers
Model 596 and Model 2596
IOM
Controls 04/2020
REV B.
Page
2
of 9
Eaton Filtration LLC,
44 Apple
Street, Tinton Falls,
NJ
07724 www.eaton.com/filtration
Phone:
732-212-4700
RECEIVING, HANDLING AND INSPECTION
The control panel, motor and accessories have been packed
in a separate container but shipped with the strainer. This
provides protection from damage during
transit and also provides for ease of storage if the controls are
not installed immediately. When first received the following
must be done:
1. Unpack and inspect for damage.
2. Report any damage to carrier immediately.
3. If controls are not installed at this time, refer to Storage
Instructions.
STORAGE INSTRUCTIONS
Repack all components in the original carton and reuse all
protective packaging. Store all components in an indoor,
clean, and dry environment. Protect from temperature
extremes. Mark cartons to protect from handling abuse.
STRAINER MODE OF OPERATION
CONTINUOUS BACKWASH
This is the most effective way to keep the strainer element
“
clean
”
and have the least pressure loss. Continuous element
washing can be accomplished with a minimum of control
devices. However, it offers no flexibility of operation when
there are significant changes in flow volume or solids content
of the fluid.
The
“d
rain
”
line requires a blow-down/drain valve which may
be manually operated. Normal valve position is CLOSED.
The backwash line requires a backwash valve which may be
manually operated on the backwash line. Normal valve
position is FULL OPEN.
The backwash motor requires a motor starter. Furnish with
overload protection and fused disconnect.
STRAINER MODE OF OPERATION
AUTOMATIC BACKWASH (TIMED CYCLE)
The preferred mode of operation for a self-cleaning strainer is
one where the control system will permit both intermittent and
continuous backwash as required by operating conditions.
The
“d
rain
”
line requires a blow-down/drain valve which may
be manually operated. Normal valve position is CLOSED.
The backwash line requires a backwash valve, either electrically
or pneumatically operated on the backwash line. This valve
should operate only in the FULL OPEN or FULL CLOSED position.
A fully adjustable differential pressure switch is furnished to
detect the increase of pressure across the strainer. It will
activate a backwash cycle independent of the time-controlled
sequence. NOTE: Set switch at 2psi over the observed clean
pressure drop.
Eaton provides a control panel, containing all necessary relays,
timers, lights, switches, etc. This will initiate and monitor the
intermittent backwash cycles.
VALVE SELECTION
Several important factors to consider when selecting the
necessary valves.
Valve Type: Gate, plug, and butterfly valves can be used.
However, ball valves provide the most advantages. Ball valves,
when
“
Full Open
”
provide a uniform and straight flow path
minimizing pressure loss. Since only 90° rotation of the stem is
required to go from
“
Fully Closed
”
to
“
Fully Open
”
motorized
operators are easily adapted and provide short cycle times.
Valve Material: Iron, bronze, steel, and stainless steel are the
most common. Select valve and trim material that will not
corrode or react with the process fluid or the environment.
Pressure Rating: Select the valve class with a pressure rating
equal to or greater than the system design pressure.
Connection: Select a valve with end connections (flanged,
threaded, etc.) that will provide ease of maintenance and
trouble-free service.