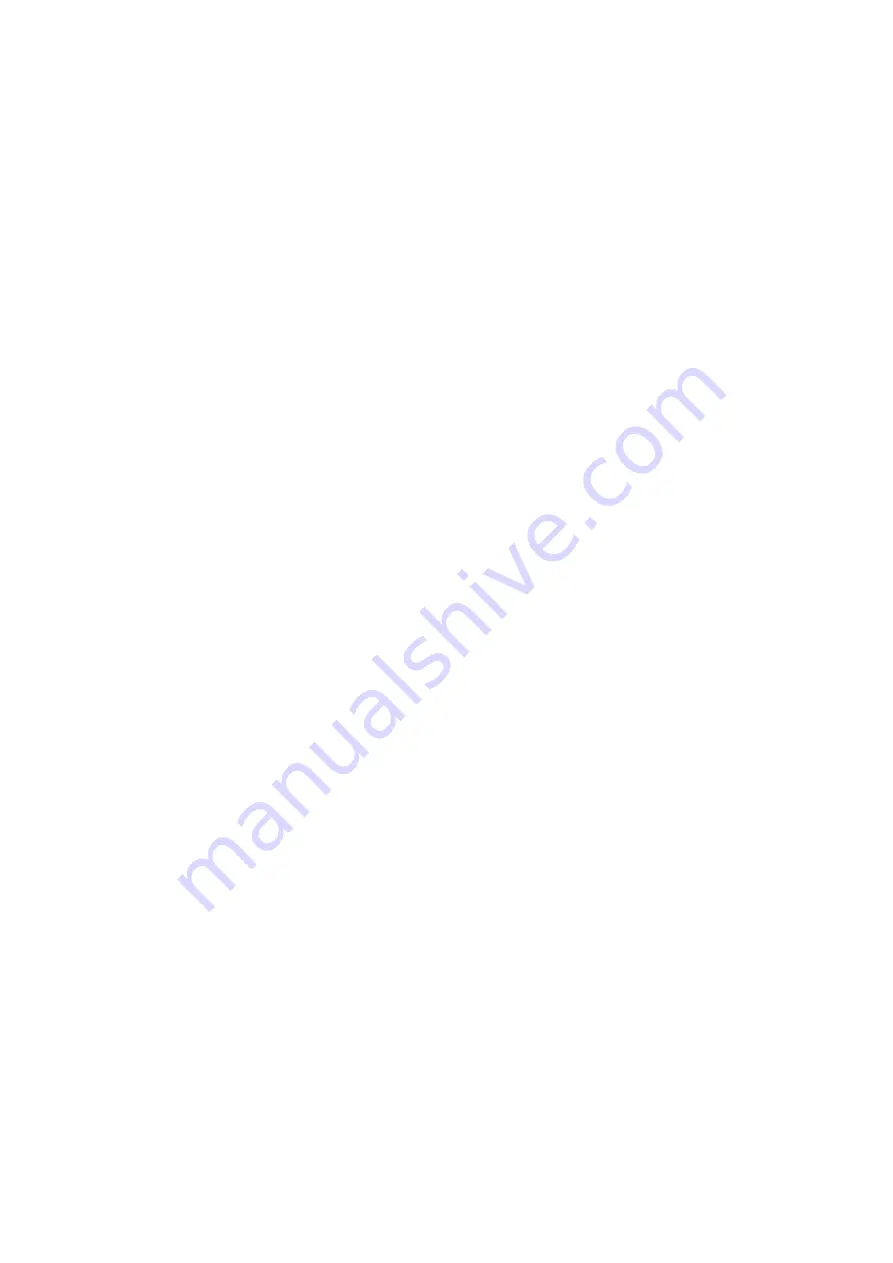
7 Function description
ESR5-NV3-300
12/19 MN049006EN
www.eaton.com
11
7 Function description
7.1 Single-channel sensor circuit
The sensor circuit is not designed with redundancy.
The safety relay does not detect short and cross-circuits in the sensor circuit.
7.2 Two-channel sensor circuit
The sensor circuit is designed with redundancy.
Depending on the wiring, the safety relay has cross-circuit detection.
With the corresponding wiring, the safety relay detects short and
cross-circuits in the sensor circuit.
7.3 Automatic start
The device starts automatically after the sensor circuit has been closed.
7.4 Manual, monitored start
The device starts with closed sensor circuit once the start circuit has been
closed by pressing the reset button.
A connected reset button (connected to S33/S34) is monitored.
7.5 Safe shutdown
When the sensor circuit is opened, the enabling current paths 13/14, 23/24,
and 33/34 open without delay.
The enabling current paths 57/58 and 67/68 open after the delay time has
elapsed.
When the enabling current paths are open, the device is in the safe state.
The signaling current path 41/42 closes.
7.6 Off delay
The enabling current paths 57/58 and 67/68 drop out after the set delay time
has elapsed (stop category 1).
Use the rotary switch and DIP switch on the device to set the delay time in
24
increments from 0.2
s to 300
s.
→
See also
Summary of Contents for 171858
Page 1: ...Manual ESR5 NV3 300 Safety relay 12 19 MN049006EN...
Page 4: ......