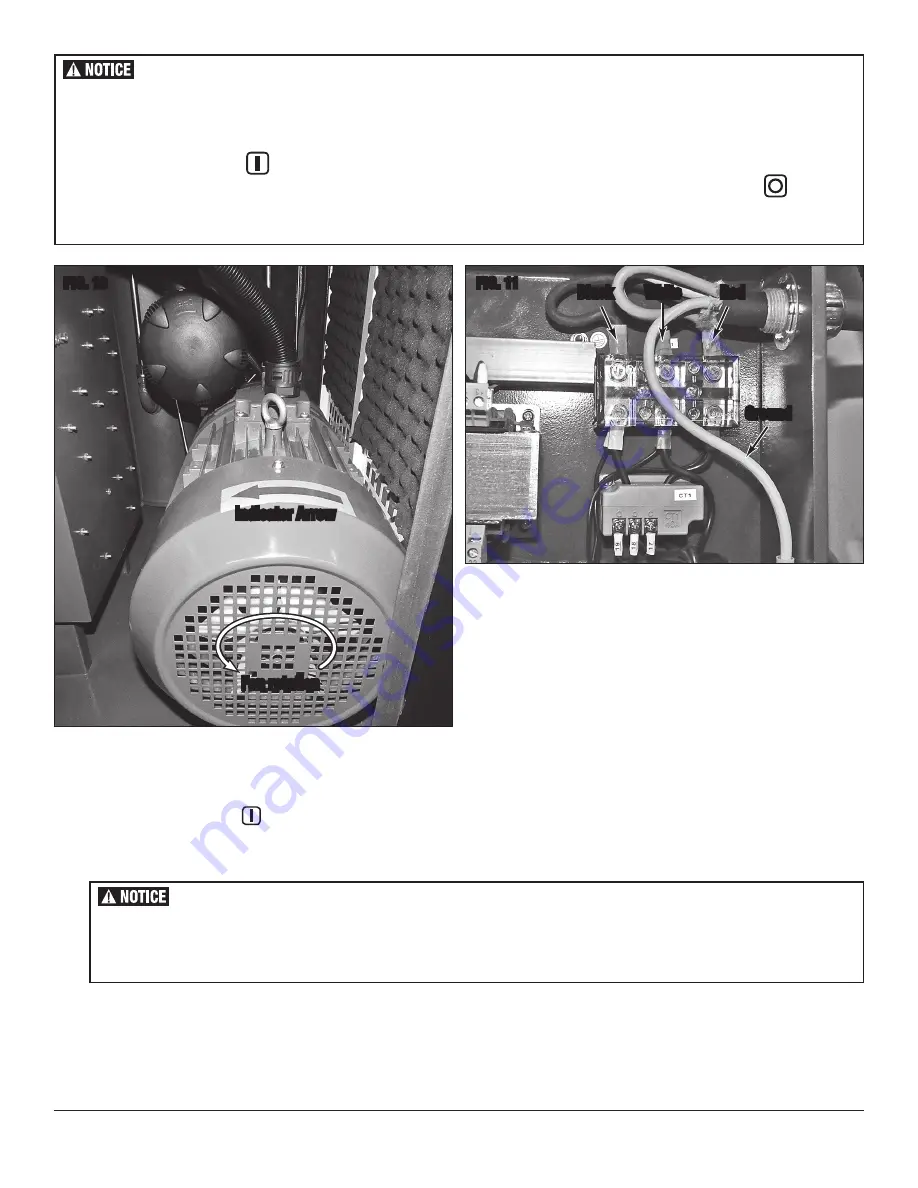
To order parts and supplies: 800.343.9353 >> eastwood.com
9
As an added precaution, the following check should be performed before starting the Compressor for the first time:
1.
Obtain the assistance of an observer and view the Motor cooling fan blades visible through the screened housing at the end of the Motor case
(FIG 10)
.
2.
Have the same observer note the directional arrow label on the Motor case
(FIG 10)
.
3.
Depress the “START” Button of the Control Panel.
4.
If the observer views the cooling fan begin to rotate in the opposite direction of the directional arrow label, depress the “OFF” Button immediately!
5.
If 3 phase connection corrections are required, do so and repeat check sequence beginning at step 1.
6.
If correct rotation of the Motor has been verified, proceed to COMPRESSOR OPERATION.
FIG. 10
FIG. 11
COMPRESSOR OPERATION
• Depress the “START” Button of the Control Panel
(FIG 9
).
• Allow the Tank pressure to build to 145 PSI [10 bar] before each use. With the Air Compressor turned on, operation is automatic and under the control of
the internal Pressure Controller. It will turn off @ 145 PSI [10 bar] and automatically restart @ 115 PSI [8 bar].
The Pressure Gauge is visible through the upper right-side Compressor Panel and indicates the actual output line and tank pressure.
When the pressure reaches the 145 PSI [10 bar] cutoff point, an Unloader Valve will automatically release static pressure in the
Scroll to allow it to easily restart without needing to overcome residual pressure. This produces a momentary audible “hiss” or
“burbling” sound and is normal.
Indicator Arrow
Fan rotation
Ground
Black White Red
✓
✓
✓
✓