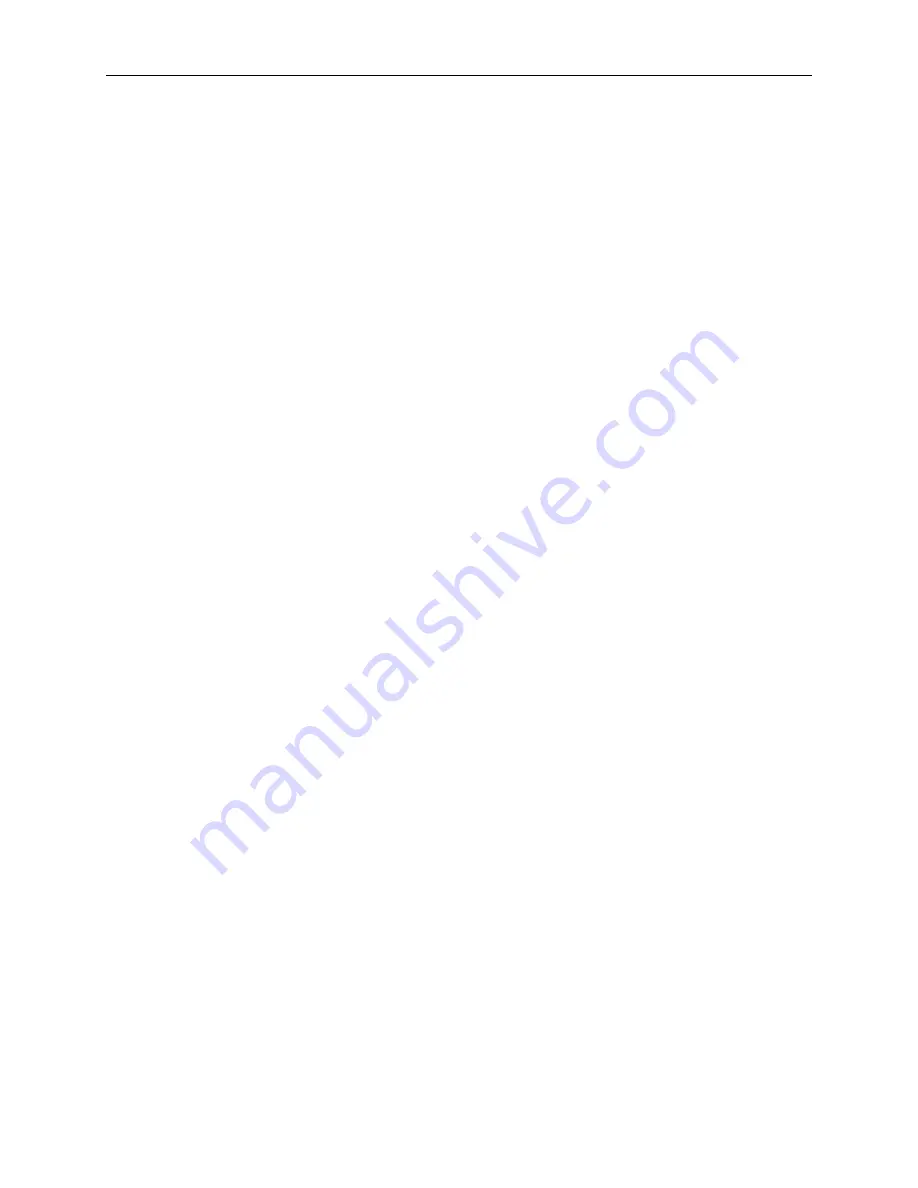
10 Introduction
Standard Features
•
Designed to seal most polyolefin, polyethylene, and PVC* shrink films
*
With hot knife systems only.
•
All-welded main frame from 12 gauge steel
•
Seal head casting equipped with head return cylinder
•
Stainless steel film clamps hold film in place while sealing
•
Available with hot wire or hot knife seal systems
•
Hot knife seal systems available with mushroom (standard), pancake, or arrow
inserts
•
Dual locking magnet clamps apply even pressure across the seal-bar
•
Adjustable dwell time for better seal control
•
Analog temperature control adjustable for a variety of films
•
Adjustable product tray accommodates wide variety of product sizes
•
Takeaway conveyor can be raised or lowered to center the seal with the product
•
Automatic takeaway conveyor with stainless steel mesh belting
•
Heavy duty film roll support and simple film loading
•
Adjustable pin perforator provides air evacuation
•
Custom two-part epoxy finish resists scratching
•
Heavy duty casters for transportation within plant
•
Easy to use design requires minimal training and maintenance
•
Side seal size of 16 in. × 22 in. or 16 in. × 36 in.
•
Maximum film width up to 19 inches
•
EM1622T, EM1622TK & EM1636TK available in 110V or 220V
EM1636T available in 220V only
•
Made in the USA
Highlights
•
Available in hot knife or hot wire seal systems
•
Adjustable product tray easily separates film and accommodates variety of
product sizes
•
Adjustable pin perforator provides air evacuation in film
•
Simple, easy to use control panel with automatic cycle timing
•
Takeaway conveyor can be raised or lowered to center the seal on your product.