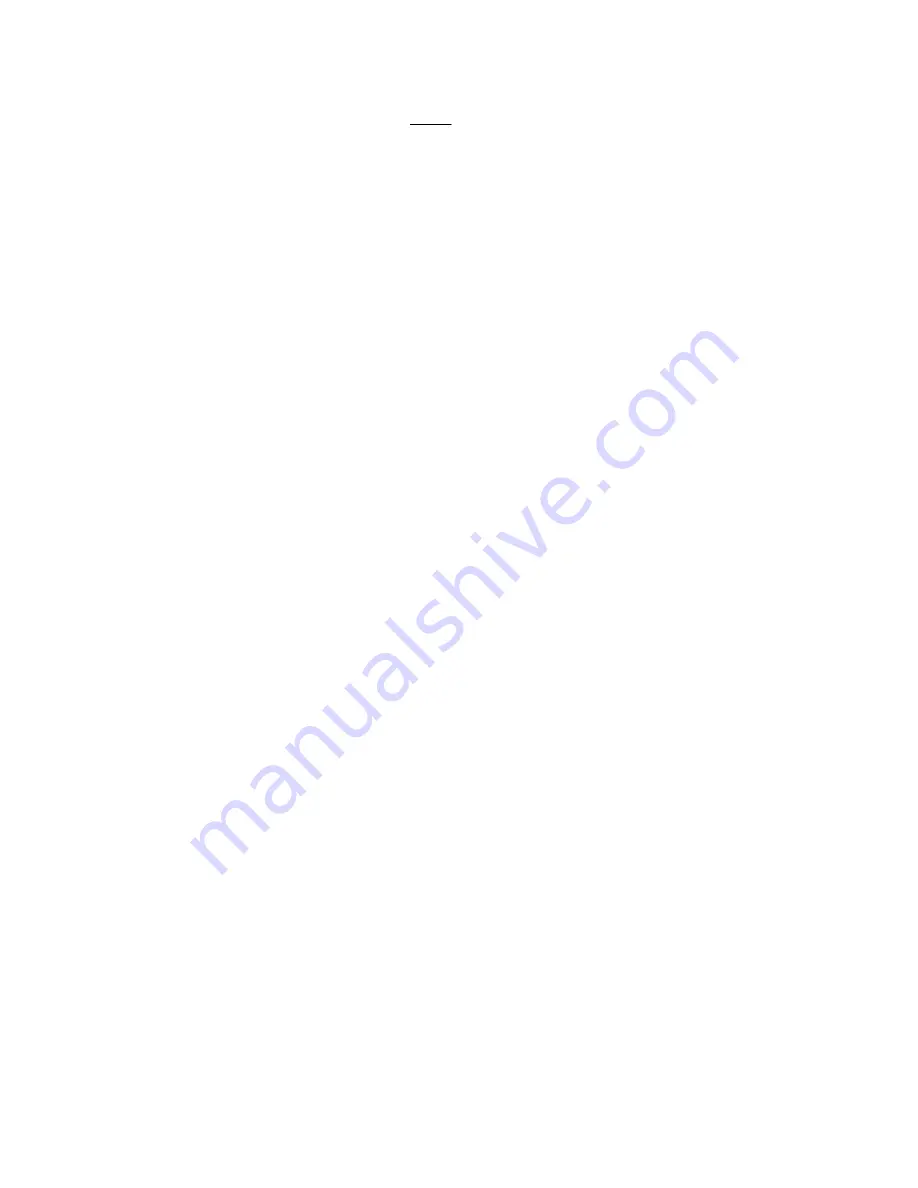
20
tg
2=
/
=
L
d
D
2
−
Where
D
d
large end diameter, small end diameter;
L: axial length between D and d;
2: included angle between conical generatrix and central line
“D and d ” shall keep a distance from the end-face. The measuring method is same with
5.2.1. “L” can be read out from the transversal handwheel
(see No.15 in Fig.2) of the
worktable. To make the calculation easier, “L” is better to be rounded to an integral
number.
5.2.3 Inner dimension measurement using double measuring accessories
The internal measuring accessories are divided to two kinds: the large-size ones are used
for measuring a hole bigger than 30mm (Fig.9, Fig.10); the small-size ones are used for
measuring hole bigger than 10mm. For measuring a hole less than 10mm, it is necessary
to use a electrical measuring method. (See
5.2.4)
This is a relative measurement. The standard samples are small-size and large-size standard ring gauges (No.53, No.52 in Fig.6).
Their actual dimensions are written on their end-faces and the calibrated positions are indicated by scale.
The large-size measuring accessories are fixed on the measuring spindle and the shaft of
28mm on the tailstock. When using small-size measuring accessories, it is necessary to
change the shaft into a special one and make its mark align with the tailstock mark. The
measuring accessories are mounted on the fixed shaft of the cap-shaped measuring
accessories. Open the front cover of the special shaft and adjust the four screws to correct
axiality (Note: it is better for the user not to adjust the axiality because it has been
calibrated before ex-factory.) If required, it can be adjusted by mounting the plain
measuring accessories. The four screws shall be locked after adjustment.
Procedures for measuring a internal dimension with double measuring accessories:
a) Mount the measuring accessories and make the weight for the outer measuring relieve
from the measuring spindle and replace weight for outer measuring;
b) First mount the standard ring gauge on the worktable and let the mark line parallel
with the measuring spindle. Lift the worktable to make the two measuring accessories
penetrate into a hole and contact with the hole wall to find a “turn-over point” and
record the reading L
0
or reset the display by pressing a key;
c) Remove the ring gauge and replace the workpiece. Lift the worktable to make the two
measuring accessories penetrate into a hole and contact with the hole wall to find a
“turn-over point” and record the reading L
1;
Summary of Contents for EX-100
Page 4: ...3 Fig 3...