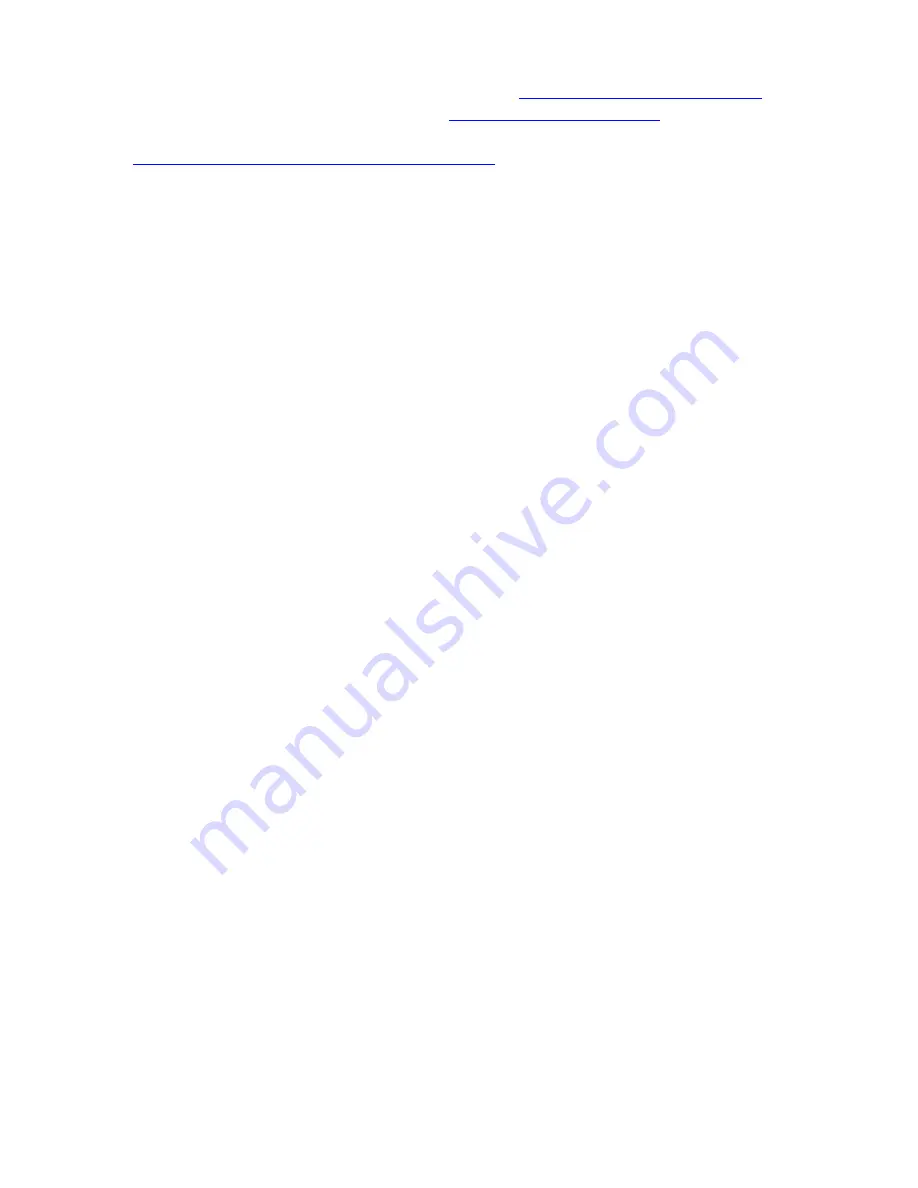
HWM-H-IOM (10/14)
Page 12
Straight propylene-glycol: Chemical Specialties, Inc. (
www.chemicalspec.com/spg.html
)
Inhibitor: Nu-Calgon Products, Ty-lon B20 (
www.nucalgon.com/products
)
Inhibited propylene-glycol: Houghton Chemical Corp., SAFE-T-THERM
®
,
www.houghton.com/fluids/safe-t-therm/index.html
)
General guidelines for introducing propylene glycol into the water circulating system follow. The
manufacturer’s specific instructions and industry standards always take precedence when
introducing propylene-glycol to the system.
Calculate the quantity of inhibited propylene-glycol (fluid) required to achieve the
desired results.
Introduce a sufficient quantity of water to the system and pressure check to ensure a
sealed system.
Drain some water from the system to provide enough volume for the calculated
amount of fluid.
Add the correct amount of fluid and any water needed to completely refill the system,
allowing for liquid expansion due to operating temperature.
Circulate the inhibited propylene-glycol antifreeze solution for at least 24 hours to
ensure complete mixing. Check the liquid concentration to assure that the correct
mixture is obtained.