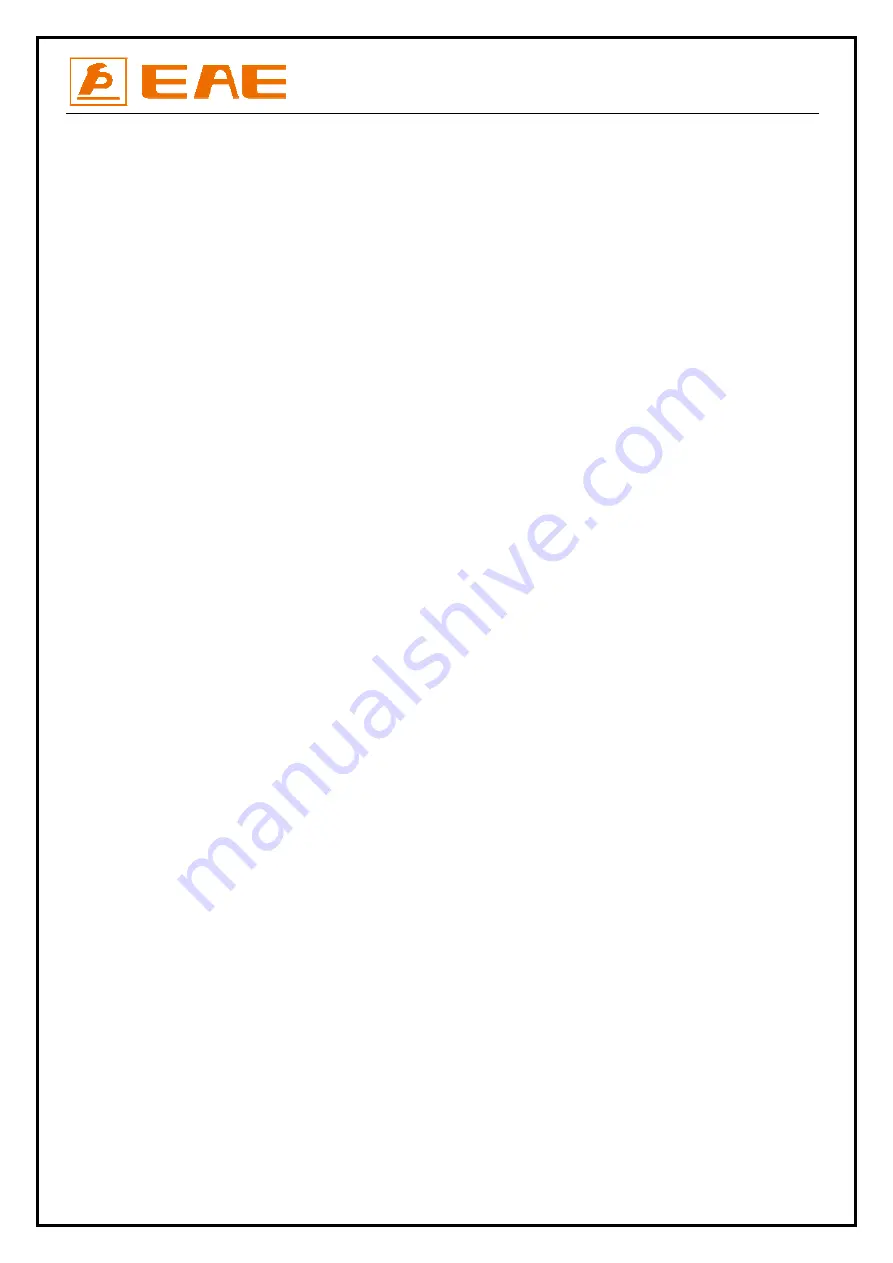
Installation, Operation and Parts Manual
EE-6605S/A/B
17
MAINTENANCE
Easy
and
low
cost
routine
maintenance
can
ensure
the
lift
work
normally
and
safely.
Follow
the
below
routine
maintenance
schedule
with
reference
to
the
actual
working
condition
and
frequency
of
your
lift.
Lubricate
moving
parts
with
No.1
lithium
base
grease.
6.1.
Daily
checking
items
before
operation
The
user
must
perform
daily
check.
Daily
check
of
safety
system
is
very
important
–
the
discovery
of
device
failure
before
action
could
save
your
time
and
prevent
you
from
great
loss,
injury
or
casualty.
∙
Check
whether
oil
hose
well
connected.
No
leakage
is
allowed.
∙
Check
the
electric
connections
.Make
sure
all
connections
are
in
good
condition.
∙
Check
whether
the
expansion
bolts
well
anchored.
∙
Check
if
safety
teeth
and
safety
block
matched
well
or
not.
6.2.
Weekly
checking
items
∙
Check
the
flexibility
of
moving
parts.
∙
Check
the
working
conditions
of
safety
parts.
∙
Check
the
amount
of
oil
left
in
the
oil
tank.
Oil
is
enough
if
the
carriage
can
be
raised
to
highest
position.
Otherwise,
oil
is
insufficient.
∙
Check
whether
the
expansion
bolts
well
anchored.
6.3.
Monthly
checking
items
∙
Check
whether
the
expansion
bolts
well
anchored.
∙
Check
the
tightness
of
the
hydraulic
system
and
screw
firm
the
joints
if
it
leaks.
∙
Check
the
lubrication
and
abrasion
circumstance
of
moving
parts.
6.4.
Yearly
checking
items
∙
Empty
the
oil
tank
and
check
the
quality
of
hydraulic
oil.
∙
Wash
and
clean
the
oil
filter.
If
users
stick
to
the
above
maintenance
requirements,
the
lift
will
always
keep
a
good
working
condition
and
its
service
life
could
be
extended.
Summary of Contents for EE-6605S
Page 19: ...Installation Operation and Parts Manual EE 6605S A B 19 Floor plan for surface installation...
Page 21: ...Installation Operation and Parts Manual EE 6605S A B 21...
Page 22: ...Installation Operation and Parts Manual EE 6605S A B 22...
Page 23: ...Installation Operation and Parts Manual EE 6605S A B 23...