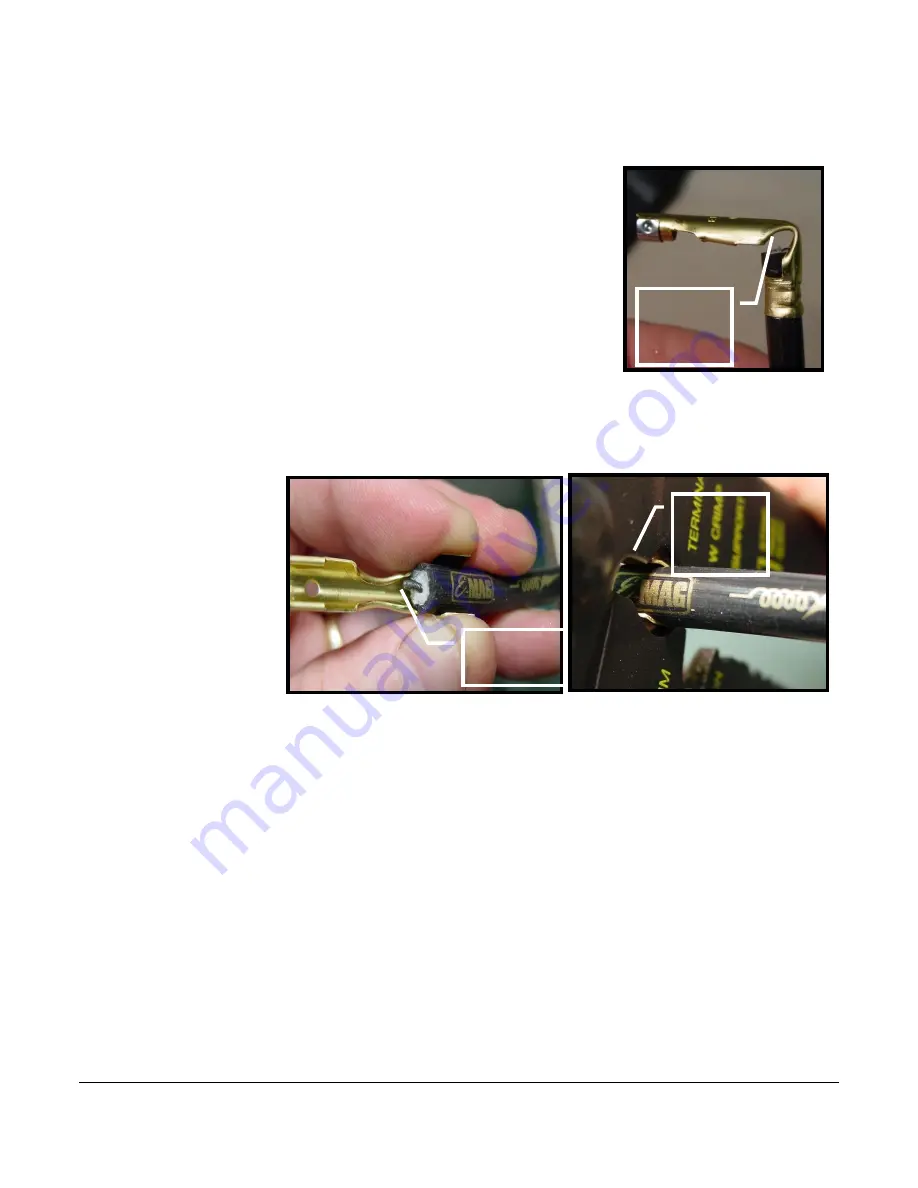
28
Bend
coil
terminal
90 deg
Terminals and Boots
Coil ends
- The brass terminals and 90-degree flat-backed boots are
for the coil end connections. Run the wire completely through the
boot so you have a couple of inches extended past the boot. This will
give you room to work the wire and terminal. A light coating of
SILICONE SPRAY
(not included) is required to lubricate the wire as
you work it through the boot.
Plug ends
–
90-degree boots and terminals are standard, but you
can specify straight plug boots and terminals (when placing your
order) at no additional cost.
With either style, you can crimp the
terminal to the wire and then insert the assembly into the boot with
silicone spray lubrication.
Note 1: It is best to push wire into the boot (rather than pulling) to avoid straining the wire core.
Note 2: Free the terminals from their strips with wire cutters. The terminals are NOT finger friendly.
They will easily cut if not handled carefully.
Pre-Crimp
-
Fold the ¾”
of exposed wire core
back against the lead
and position it in the
crook between the
terminal ears. Then
finger pinch the terminal
ears to 1) provide a
preliminary snug fit, and
2) reduce the spread
between the ears so
they fit in the “W Crimp”
station of the crimping tool. Position so you have at least 1/8” of plug wire past the terminal ears.
Final Crimp
- Crimp the terminal using the W Crimp Station on the Tool. Position the ears so they
feed toward the side with the “W” point. The ears will roll back toward each other and imbed
themselves in the outer jacket as the Final Crimp is formed. Push (not pull) the terminal to final
position inside the boot.
Coil terminals will need to be bent 90 degrees (at the narrow section) before positioning in the boot.
Resistance Check
- Verify the finished leads are assembled correctly with a simple ohm check.
Each lead should produce roughly 180 ohms of resistance per foot of plug wire. To check,
disconnect the leads at both ends so you can make (firm) ohmmeter contact with the terminals on
each end. Watch the ohmmeter display while you exercise each end vigorously (twist/bend/tug) to
see if the reading jumps
significantly (several times the normal range). To repair a crimped terminal end, simply snip off the
bad end (assuming you have an inch or so to spare) and replace with a new terminal.
Note 1: Resistance checks are also recommended at annual inspection. It tests the condition of the
conductive components, but it does not check the electrical insulation, which is another way that
wires can fail. A visual inspection of plug wire is recommended, especially in areas of possible
Core wire is
folded back.
Pre-Crimp
jaws are
near tool
hinge.