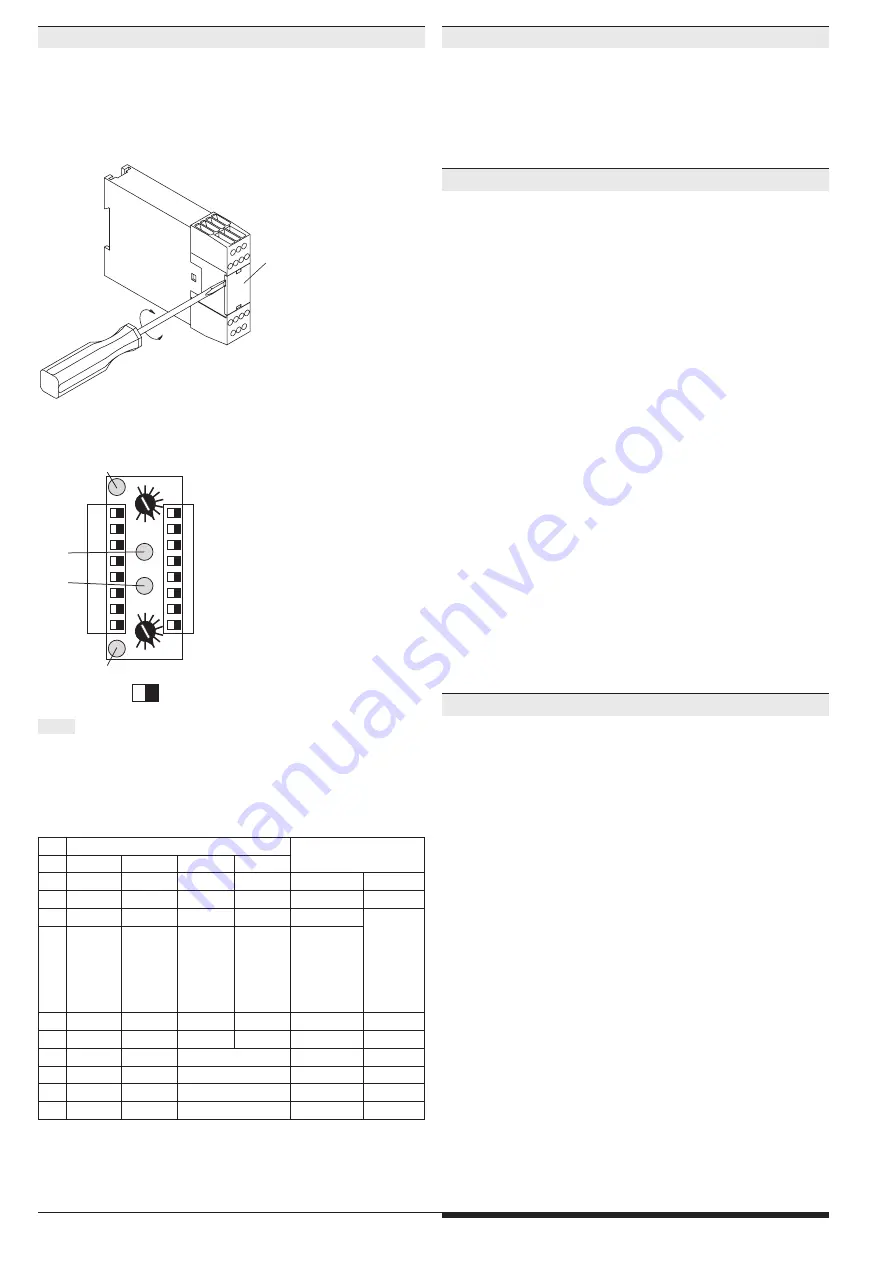
6
BG 5913.08/_2 _ _ _ / 03.11.20 / 314A
The module is assigned to the start inputs and the safety outputs via the
DIP switches.
The combinations of individual functions are set via the rotary switches.
To prevent accidently adjustments, these elements are covered by a front
plate and are redundant.
plate
M2926_
a
M8941_b
0
2
3
4
7
8
9
0 1 2
5
6
7
9
1
2
3
4
5
6
7
8
output
Mod3
Mod2
Mod1
Base
Mod3
Mod2
Mod1
Base
S1
S2
1
2
3
4
5
6
7
8
start
input
T1
T2
T3
T4
T1
T2
T3
T4
green LED "en 1"
green LED "en 2"
white LED
"run 1"
white LED
"run 2"
off
on
•
Settings to the unit must be performed by skilled personnel while
the unit is disconnected.
•
Before the front cover is removed, antistatic precautions must be
observed.
Note:
Setting of the Modules
Sw.
Function at Terminals
Start behavior of the LC
/ E-Stop
S12-S14 S22-S24 S32-S34 S22-S24
0
Gate
Gate
E-Stop
LC
Autostart
1
Gate
Gate
E-Stop
LC
Manual Start
2
E-Stop
E-Stop
E-Stop
E-Stop
Autostart
Enabling
only
when
all other
modules
permit
enabling
3
E-Stop
E-Stop
E-Stop
E-Stop Manual Start
4
E-Stop
E-Stop
E-Stop
E-Stop
Autostart
5
E-Stop
E-Stop
E-Stop
E-Stop Manual Start
6
E-Stop
E-stop
Two-hand IIIC
Autostart
7
E-Stop
E-stop
Two-hand IIIC
Manual Start
8
Gate
Gate
Two-hand IIIC
Autostart
9
Gate
LC
Two-hand IIIC
Autostart
Each function activates an enabling signal in the module software. The
control unit is permitted to enable the assigned safety outputs only after
all 3 (for two-hands control) or 4 enablings have been given.
With the exception of two-hand control, each function works independently.
The assigned safety outputs are enabled if the precondition for enabling
has been met for all functions.
This function will only work when the other two functions have already
permitted enabling. To provide for enabling, the two buttons must be
pressed within 0.5 s. As soon as one of the other function reacts, the two
buttons must turn inactive before the others can be enabled again. Only
after that, the buttons can be activated once more from an inactivated state.
The unit must be connected as specified in the application examples.
When the operating contacts are connected in parallel or in series, safe
functioning of the unit is cancelled.
The two-hand buttons must be designed and arranged in such a way as to
ensure that they cannot be disabled with easily, or pressed unintentionally.
The safety distance between the push buttons and the place of danger
must be large enough to make sure that after releasing a button, the place
of danger can only be reached after the dangerous movement has stopped.
The safety distance “S” is calculated according to the following formula:
S = V x T + C, where
a) gripping velocity V = 1 600 mm/s
b) overtravel time T (s)
c) and safety factor C = 250 mm.
When any access into the danger area, with operating keys pressed, is
safely prevented, e.g. by a protective cover for the keys, the safety factor
C may be set to the value 0. Generally, the minimum safety distance must
be 100 mm. In this respect, also see DIN/EN 574.
The two-hand control must be released when another function module
which affects the same outputs does not permit enabling.
The system may comprise only one function module with two-hand control.
The safety gate function always permits enabling if both contacts change
from inactive to active state within 3 seconds. If the second contact reacts
later, both changeover contacts must turn inactive before they can be
enabled again.
When activating the system, press the start button to simulate the compul-
sory opening and re-closing of safety gates which have been kept closed
since the system has started.
This simulation is possible only before enabling has been permitted for
the first time, and as long as both safety gate contacts remain closed as
well. As soon as a contact opens, simulation of the safety gate function
is no longer possible.
Setting of the Module
Functional Principle of Combined Inputs
Function of the Two-Hand Control
Safety Gate Function