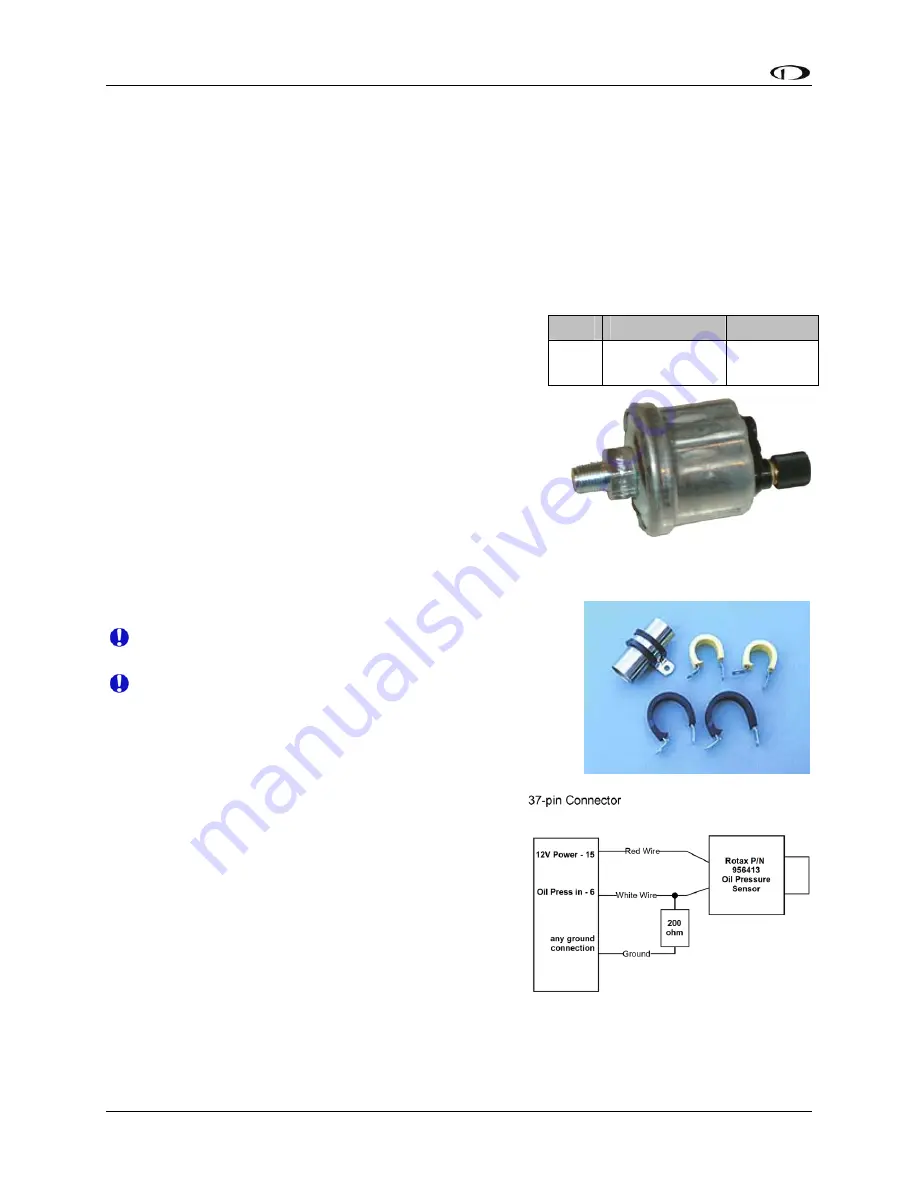
Transducer Installation
If you notice fluctuations on the manifold pressure reading on the FlightDEK-D180, you may
need to install a restrictor with a small hole inline between the sensor and the head where the
manifold pressure line is split off.
Oil Pressure Sensor
The FlightDEK-D180 supports several oil pressure sensor installations. The Dynon-supplied
sensor and the Rotax and Jabiru pre-installed sensors are the most common.
DYNON-SUPPLIED OIL PRESSURE SENSOR
First, mount the oil pressure sensor to a fixed location
using an Adel clamp (see picture at lower right) or other
secure method. The oil pressure sensor must
not
be
installed directly to the engine due to potential vibration
problems. Dynon Avionics’ sensor is supplied with a
1/8” NPT pipe thread fitting. An adapter might be necessary
for some engines. Please see the manual supplied by the
engine’s manufacturer. You must use appropriate pipe fitting
adapters and
ensure that the case of the sender has a
connection to ground.
This is critical for functionality.
Pin
Color
Function
6 White/yellow
Oil
pressure
3-6
FlightDEK-D180 Installation Guide
Use an Adel clamp similar to the
above to secure the pressure sensor
Crimp a standard #8 ring terminal onto the white/yellow wire
from pin 6. Unscrew the stud cap from the threaded stud.
Place the ring terminal on the stud and secure the cap down
sandwiching the ring terminal.
1/8-27 NPT
0-150 PSI
Due to vibration issues, never connect the sensor
directly to the engine.
If you use Teflon tape or other seal, ensure the sensor
casing still maintains a good connection to ground.
JABIRU AND ROTAX OIL PRESSURE
If you are installing on a Jabiru or Rotax engine, your engine
comes with a pre-installed oil pressure sensor.
Prior to mid-2008, Rotax provided an oil pressure
sensor with 2 tabs for electrical connection. In mid-
2008, Rotax switched to a new type of oil pressure
sensor (Rotax P/N 956413) with an integrated 2-wire
cable. Connect this newer sensor according to the
wiring diagram at right. Connect the red wire of the
new sensor to EMS DB37 Pin 15 (12V). Connect the
white wire of the new sensor to EMS DB37 Pin 6.
Then, connect one end of a 200
Ω
resistor to pin 6,
and the other end to ground. The Jabiru and both types of Rotax oil pressure sensors are
compatible with the FlightDEK-D180. Select the correct sensor type as described in the Oil
Pressure Configuration section on page 6-9.
Summary of Contents for FlightDEK-D180
Page 2: ......
Page 4: ......
Page 18: ......
Page 28: ...Transducer Installation 3 10 FlightDEK D180 Installation Guide...
Page 38: ......
Page 58: ......
Page 78: ......
Page 81: ...DSAB Configuration FlightDEK D180 Installation Guide 7 3...
Page 116: ......
Page 131: ...Appendix FlightDEK D180 Installation Guide 9 15...
Page 132: ...Appendix 9 16 FlightDEK D180 Installation Guide...