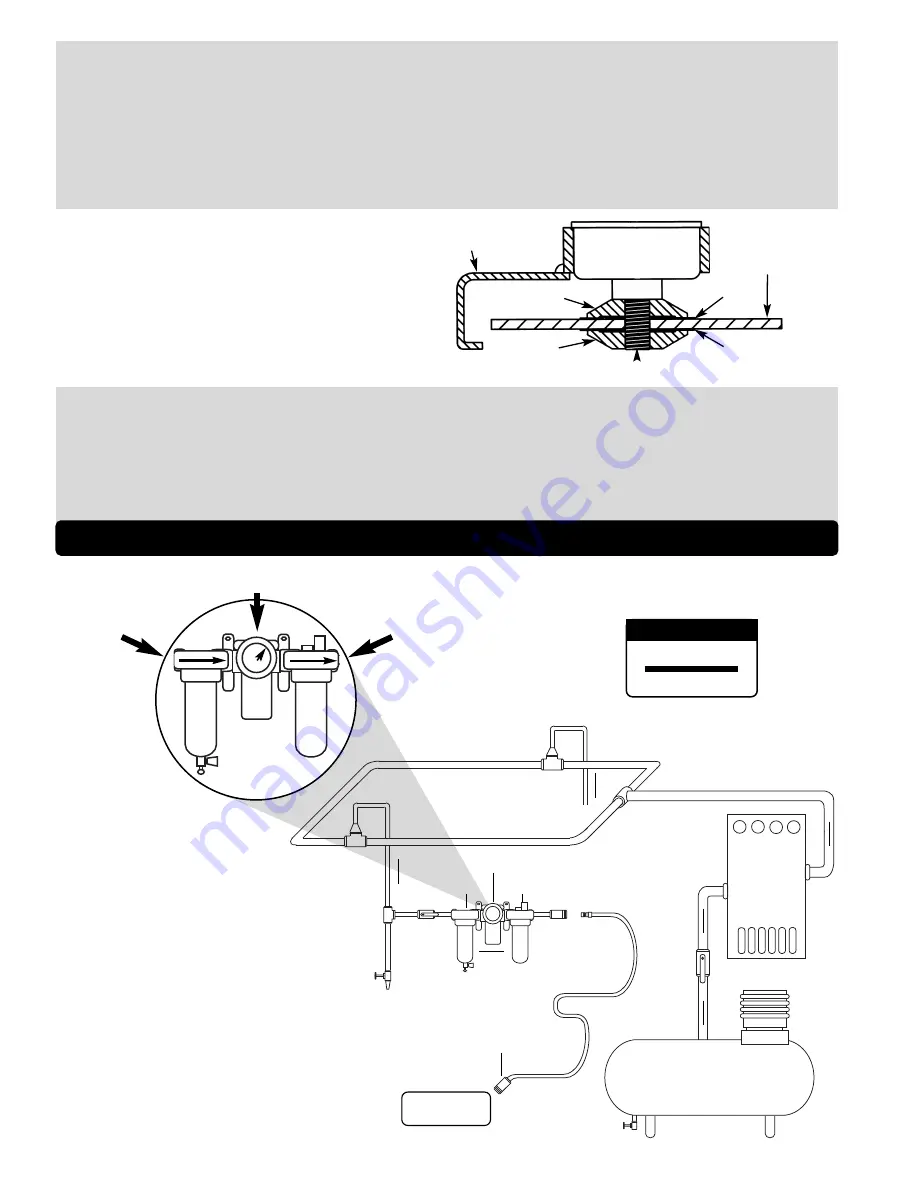
OPERATING INSTRUCTIONS (continued)
Caution:
Hand, wrist and arm injury may result from repetitive work, motion and overexposure to vibration.
• Keep hand and clothing away from working end of the air tool.
Be sure that any loose clothing, hair and all jewelry is properly restrained.
• Secure inlet bushing on air tool with a wrench before attempting to install the air fitting to avoid damaging housing assembly.
• Check tool RPM (speed) with tachometer with air pressure set at 90 PSIG while the tool is running. If tool is operating at a higher speed than the RPM marked on the tool
housing, or operating improperly, the tool must be serviced and corrected before use.
Caution:
Tool RPM must never exceed abrasive/accessory RPM rating. Check accessory manufacturer for details on maximum operating speed or special
mounting instructions.
• With power source disconnected from air tool, mount cut-off wheel onto spindle. See diagram below for typical mounting assembly.
• Follow recommended procedure from the manufacturer.
• Connect air tool to power source. Be careful NOT to depress throttle lever in the process.
Do not expose air tool to inlet pressure above 90 PSIG or (6.2 Bars).
Caution:
After installing the accessory, the cut-off tool must be started at a reduced speed to check for good balance. Gradually increase tool speed. DO NOT USE if tool
vibration is excessive. Correct cause, and retest to insure safe operation.
• Make sure that work area is uncluttered, and visitors are at a safe range from the tools and debris.
• Use a vise or clamping device to hold work piece firmly in place.
• Do not apply excessive force on tool or apply “rough” treatment to it.
• Always work with a firm footing, posture and proper lighting.
Report to your supervisor any condition of the tool, accessories, or operation you consider unsafe.
CUT-OFF WHEEL MOUNTING
Typical Mounting for Type 1 Cutting-Off Wheels
• Mount reinforced cutting-off wheel 1/8" (3.0mm)
Maximum Thickness
• Use factory recommended flanges only. Do not substitute.
Caution:
• Air tools are not intended for use in explosive atmospheres and are not insulated for contact
with electronic power sources.
• Ensure that sparks and debris resulting from work do not create a hazard.
• This tool is rear exhaust. Exhaust may contain lubricants, vane materials, bearing grease,
and other materials flushed thru the tool.
• Warning: Grinding/Sanding certain materials can create explosive dust. It is the employers
responsibility
Safety Guard
Reinforced Cut-Off Wheel
Outer Flange
Spindle
Blotter
Blotter
Driving Flange
To Tool Station
Closed Loop Pipe System
(Sloped in the direction of air flow)
Ball
Valve
Ball
Valve
Filter
Coupler
Regulator
Lubricator
Air Flow
Drain
Valve
Drain
Valve
Air Compressor
and Receiver
Drain Valve
Air Hose
Air Flow
Refrigerated
Air Dryer
2
Filter
Regulator
Lubricator
90 PSIG
(6.2 Bar)
Air System
1
DROP/MIN.
20
SCFM
LUBRICATOR SETTING
•
Dynabrade Air Power Tools are designed to
operate at 90 PSIG (6.2 Bar/620 kPa) maximum
air pressure at the tool inlet, when the tool is
running. Use recommended regulator to control
air pressure.
•
Ideally the air supply should be free from moisture.
Incorporating a refrigerated air dryer after the
compressor and drain valves at each tool station
(as shown) further reduces moisture from
condensation in the air supply.
➤
➤
➤
➤
➤
➤
Air Tool
90 PSIG MAX
(6.2 Bar)