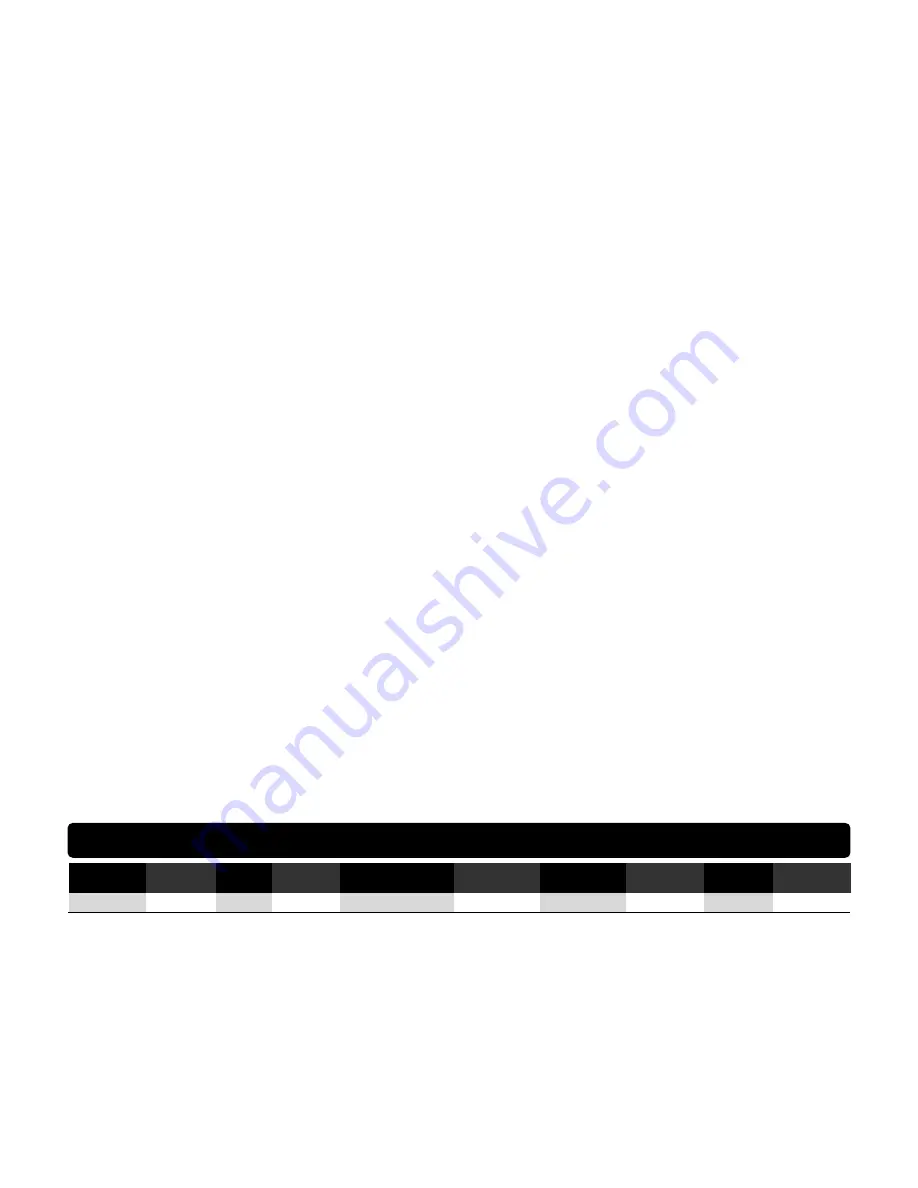
Machine Specifications
Assembly Instructions – .7 hp 3" Cut-Off Tool (Cont.)
4.
Install the 50009 Collet Body onto the rotor (torque to 17 N•m/150 in. lbs.).
5.
Check the clearance between the rotor and the bearing plate by using a .001" thick feeler gauge (clearance should be at .001" to .0015"). Adjust
clearance by repeating steps 3-5 with different shimming if necessary. Once proper rotor/gap clearance is achieved proceed with the
motor assembly.
6.
Install lubricated (10W oil;
95842
Dynabrade Air Lube)
01185
Blades (4/pkg.).
7.
Place
01028
Cylinder onto the assembly so that the air inlet opening will line up with the inlet holes in the
01721
Rear Bearing Plate.
8.
Press
02649
Bearing into the
01721
Bearing Plate by using
96240
Bearing Press Tool (ordered separately) pushing against the outer race
of the bearing.
9.
Press the rear bearing/bearing plate assembly onto the rear shaft of the
55021
Rotor by using
96240
Bearing Press Tool (ordered separately)
pushing against the inner race of the bearing.
Important:
Carefully press the bearing/bearing plate assembly onto the rotor so as to achieve a snug fit between the bearing plates
and the cylinder. A snug fit will trap the cylinder while still allowing it to be shifted from side to side with a slight amount of finger pressure. A loose
fit will not achieve the proper preload of the motor bearings.
10.
With the outer diameters of the bearing plates and the cylinder aligned carefully slide the motor assembly into the housing so that the air passage node
of the
01721
Rear Bearing Plate will fit into the air passage notch inside the motor housing. Be sure that the motor is positioned properly, all the way
into the housing before installing the lock ring.
11.
Secure the motor housing in a vise by holding on the flats of the housing so that the rotor shaft is pointing up.
12.
Insert
01796
Block Plate into
01371
Lock Ring. Apply a small amount of Loctite #567 (or equivalent) to the threads of the lock ring and install
these parts onto the motor housing (torque to 34 N•m/300 in. lbs.).
13.
The motor can now be checked for proper adjustment. With the motor housing still mounted in the vise pull up on the end of the rotor shaft while
turning it back and forth. (apply 10-15 lbs. force) Perform the same procedure while pushing down on the rotor shaft with the same amount of
force. The rotor should turn freely without any drag, or rub being felt. If a pull rub is felt, increase preload or remove shims. If a push rub is felt,
then deload or add shims.
14.
Install collet assembly.
15.
Place 3" cut-off shroud assembly over tool spindle and secure using
95168
Screw.
Motor Assembly Complete.
Throttle Positioning Procedure:
1.
Loosen the
95168
Screw to release tension on the
40029
Motor Lock.
2.
Orient the shroud housing to the operators desired grip and positioning.
3.
Tighten
95168
Screw.
Throttle Positioning Procedure Complete.
Please allow 30 minutes for adhesives to cure before operating tool.
Important: The motor should be tested for proper operation.
Before operating, place 3 drops of
95482
Dynabrade Air Lube 10W/NR (or equivalent) directly into inlet with throttle lever depressed. Carefully connect
the tool to an air supply. Operate tool for 30 seconds to allow air lube to properly lubricate internal motor components. Motor should now be tested for
proper operation at 90 PSIG max.(6.2 bar g). The tool should operate within 10% of the maximum rated RPM. If tool operates at a higher RPM than
marked on the tool or if vibration and sound levels seem abnormal, the tool should be serviced to correct the cause before use.
Tool Assembly Complete.
Loctite
®
is a registered trademark of the Loctite Corporation.
Model
Motor
Motor
Sound
Maximum Air Flow
Air Pressure
Collet
Weight
Length
Height
Number
hp (W)
RPM
Level
SCFM (LPM)
PSIG (Bars)
Size
Pound (kg)
Inch (mm)
Inch (mm)
52418
.7 (522)
20,000
79 dB(A)
37 (1,048)
90 (6.2)
3/8"
3 (1.3)
10-5/16 (265)
5-1/4 (133)
Additional Specifications: Air Inlet Thread 1/4" NPT • Hose Size 3/8" (10 mm)
Sound Level is the pressure measurement according to the method outlined in ISO regulation ISO-15744.
6