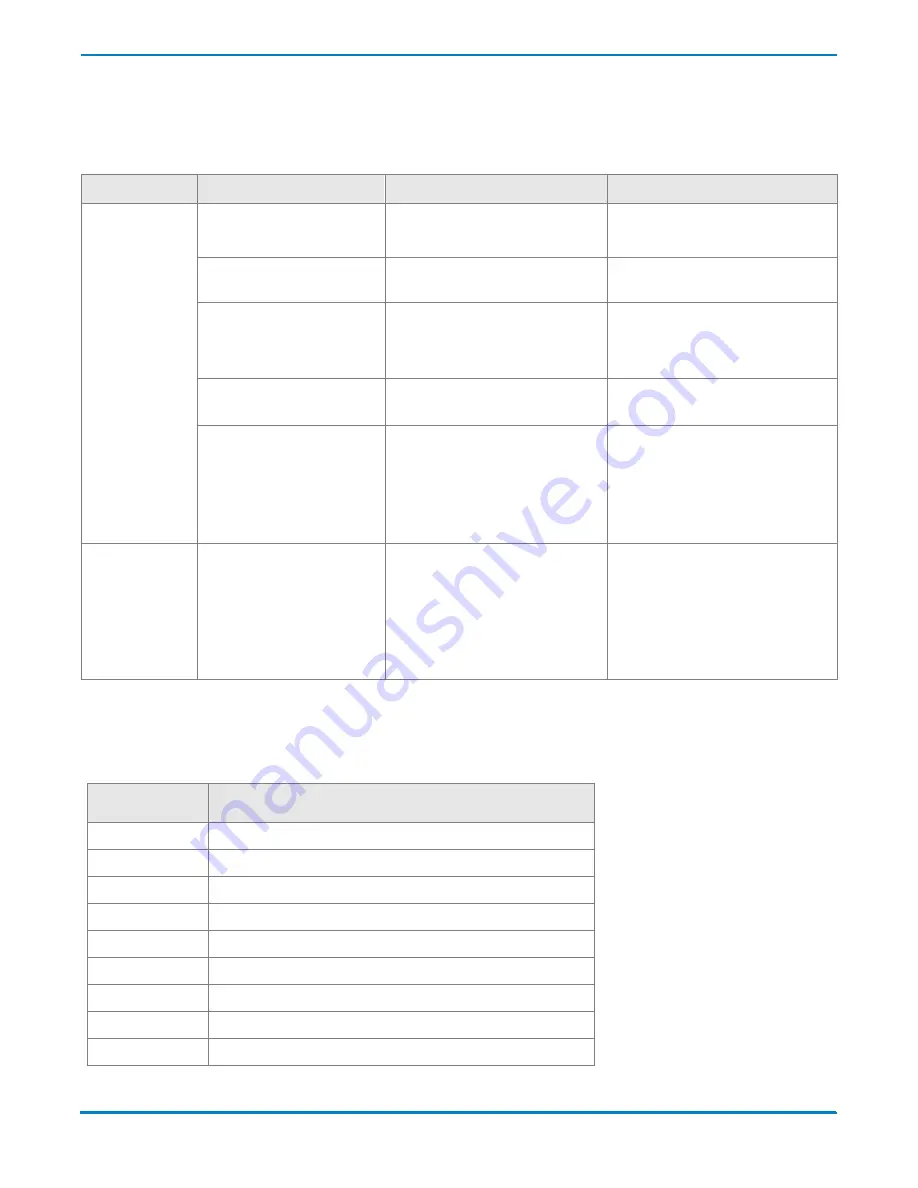
Dymax WIDECURE UV Conveyor
13
TROUBLESHOOTING
WARNING:
Only qualified maintenance personnel should attempt the following procedures:
Problem
Possible Cause
Testing
Corrective Action
Conveyor Not
Operating
Main Line Circuit Breaker
tripped.
Toggle Power Switch off,
then on.
Find cause of tripped breaker.
Improperly fastened
Connections.
Check all connections.
Properly fasten connections.
Fuses for Motor
Controller blown.
Remove Fuses from Fuse
Holders (located in the left side
of control box of unit) and
check with an Ohmmeter.
Replace Fuses if defective.
Belt is hung up.
Inspect the Belt for any signs
of a mechanical bind.
Resolve bind and continue
operation.
Tension too low on Belt
(Power Switch lights and
Motor turns but Belt does
not move).
Verify the operation of the
Drive Shaft and Drive Rollers.
Use the tracking adjustment
screws to increase the tension
on the Belt. Both knobs need to
be turned the same amount to
maintain alignment.
Belt Tracks to
One Side
Belt Adjustment Screws
are out of position.
Visually inspect the Belt. The
Belt will track to one side.
Tighten the Belt Adjustment
Screw (the one located on the
side to which the Belt is
tracking towards) until Belt
tracks straight. Only minor
adjustments should be made at
one time.
SPARE/REPLACEMENT PARTS
Part #
Part Description
40671
Conveyor Belt Guide
39376
18" Metal Halide Bulb (standard)
39613
18" Mercury Bulb
40672
Reflector for 18" Conveyor
39661
Conveyor Belt for 18" Conveyor
39373
25" Metal Halide Bulb (standard)
39614
25" Mercury Bulb
40673
Reflector for 25" Conveyor
39663
Conveyor Belt for 25" Conveyor