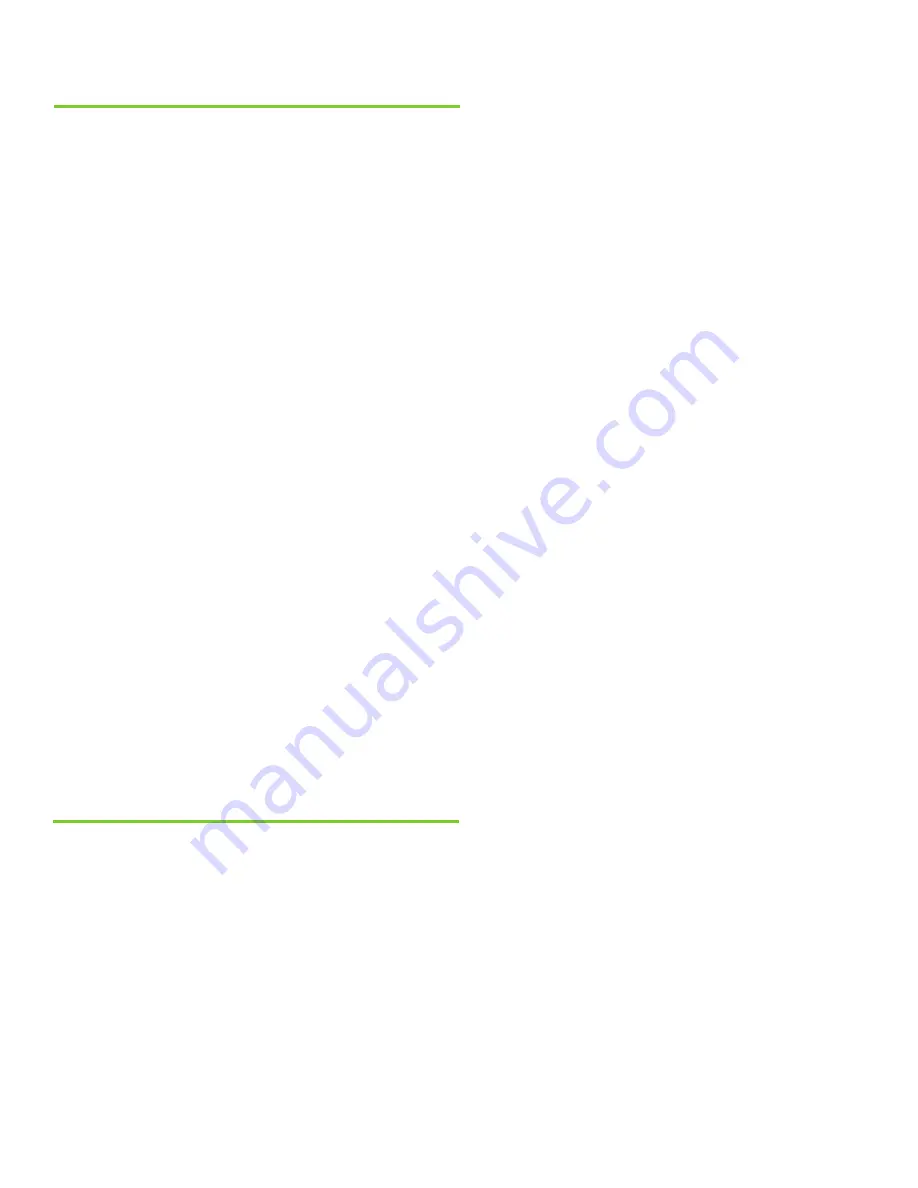
14
CONTAINMENT
To capture the blasting byproducts use heavy plastic or a tarp. Lay out your plastic and weigh the corners down, placing
your project in the center. You can sweep up media or use simple curtains or barriers.
MASKING
Mask off any glass, chrome, rubber seals, wiring, electrical, or moving mechanical parts and anything else that looks
delicate or like it shouldn’t have water and grit inside it. Tape works the best for protecting small parts and pieces.
NOZZLE CONTROL
It is important to use the proper nozzle to achieve the best blasting results. Nozzle size is based on air compressor size.
NOZZLE KNOWLEDGE
SLV Nozzle
•
Wide blast pattern
•
All purpose nozzle
ST Nozzle
•
Straight bore nozzle
•
Tight blast pattern
•
Detailed precision nozzle
Fan Nozzle
•
Spreads blast pattern out to cover a rectangular area
•
Perfect for brush blasting
•
Low impact compared to other nozzles
XL Performance Nozzle
•
Increases abrasive particle velocity
•
Allows for increased standoff distance while improving production and efficiency
CLEANUP
Depending the amount of media used, plastic may be too heavy to move all at once. Cut it into sections and roll it up, or let
the water evaporate to sweep or vacuum.
Containment, Masking, and Nozzle Control
BLAST WET, DRY, OR WITH SODA (AIR DRYER AND COOLER REQUIRED)
To prepare your machine for dry blasting:
1. Blast all media and water out of machine.
2. Remove fill cap.
3. Turn on air dryer and cooler.
4. Open air inlet valve halfway and let air circulate through machine for 5-7 min or until completely dry.
5. Put fill cap back on machine and pressurize tank.
6. Run air through the machine just like you were blasting for 2-3 min.
7. Shine light in machine to be sure all moisture is gone from the bottom.
8. If no moisture, fill with 1 bag of dry abrasive. Fill the remainder of the way.
Note: Using media such as plastic bead, walnut shell, corn cob, or soda requires dry blasting.
Switching from Wet Blasting to Dry Blasting
Summary of Contents for DB1500
Page 1: ...DB1500 DB3000 USER MANUAL...
Page 8: ...3...
Page 9: ...4...
Page 10: ......
Page 26: ...Toll Free 1 800 727 5707 International 1 713 869 2227 www DustlessBlasting com...