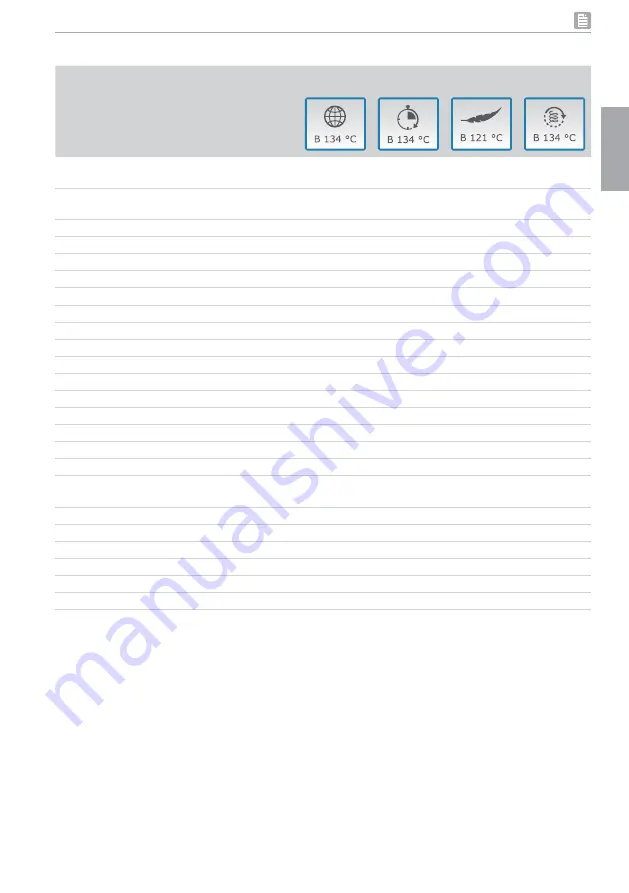
6046100064L02 1702V002SE
15
Product description
5.3 Overview of programs
Type tests
Universal
program
Quick pro-
gram
Gentle
program
Prions
program
Programme type in accordance with EN
13060
Type B
Type B
Type B
Type B
Dynamic pressure testing of the sterilisation
chamber
X
X
X
X
Air leakage
X
X
X
X
Empty chamber test
X
X
X
X
Bulky load
X
X
X
X
Porous partial load
X
X
X
Porous full load
X
X
X
Hollow body B
X
X
X
X
Hollow body A
X
X
X
X
Single packaging
X
X
X
X
Multiple packaging
X
X
X
Drying, bulky load
X
X
X
X
Drying, porous load
X
X
X
Sterilising temperature
134°C
134°C
121°C
134°C
Steriliser pressure (absolute)
312�0 kPa
312�0 kPa
210�7 kPa
312�0 kPa
Hold time
5�5 min
5�5 min
20�5 min
20 min
Max� bulky load
10 kg
6 kg
6 kg
10 kg
Max� single weight (e�g� load on tray, stand-
ard tray cassettes)
3�3 kg
2 kg
2 kg
3�3 kg
Max� massive load in containers
10 kg
6 kg
10 kg
Max� single-packed, bulky load
6 kg
1�5 kg
6 kg
6 kg
Max� double-packed, bulky load
6 kg
6 kg
6 kg
Max� porous load
2 kg
2 kg
2 kg
Max� single-packed, porous load
2 kg
2 kg
2 kg
Max� double packed, porous load
2 kg
2 kg
2 kg
X = compliance with all applicable sections of standard DIN EN 13060
EN
Summary of Contents for Hygoclave 90
Page 1: ...EN 1702V002SE 6046100064L02 Installation and Operating Instructions Hygoclave 90 0297 ...
Page 2: ......
Page 31: ...6046100064L02 1702V002SE 29 EN ...
Page 60: ......
Page 61: ......
Page 62: ......
Page 63: ......