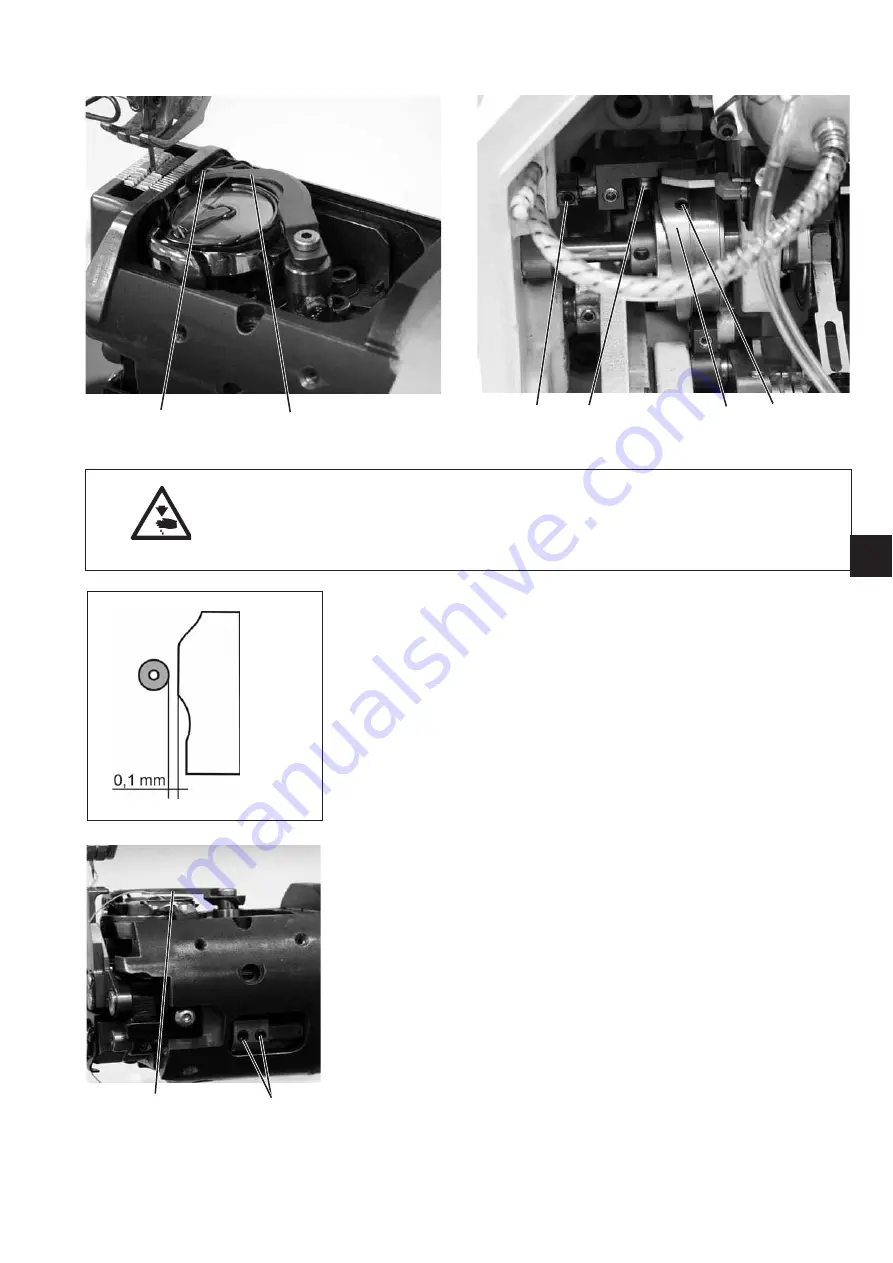
2.14.3
Thread pulling knife
Caution: Danger of injury!
Turn off the main switch.
Only check and adjust the thread pulling knife when the machine is
switched off.
Standard checking
When the thread pulling knife 1 is in its rest position the distance
between the cam 4 (highest point) and the spool 5 should be 0.1 mm.
Here the cam must be next to the edge of the snap fit coupling 8.
In the rest position the thread pulling knife should be flush with the
edge of the counter blade 2.
–
Check whether the cam is close by.
–
Turn the machine until the highest point of the cam 4 is next to the
spool 5 (80° on the hand wheel).
–
Check the distance between the cam 4 and the spool.
Correction
–
Undo screws 3 on the cam 4.
–
Put the cam right over to the right.
–
Do up the screws 3 on the cam again.
–
Undo screw 6.
–
Set a distance of 0.1mm between the cam 4 and the spool 5.
–
Tighten screw 6.
–
Undo screws 7.
–
Turn the thread pulling knife 1 so that it projects 0.2 - 0.8 mm over
the edge of the counter blade.
–
Tighten screws 7.
39
GB
2
1
6
5
4
3
1
7
Summary of Contents for M-Type 869
Page 4: ......