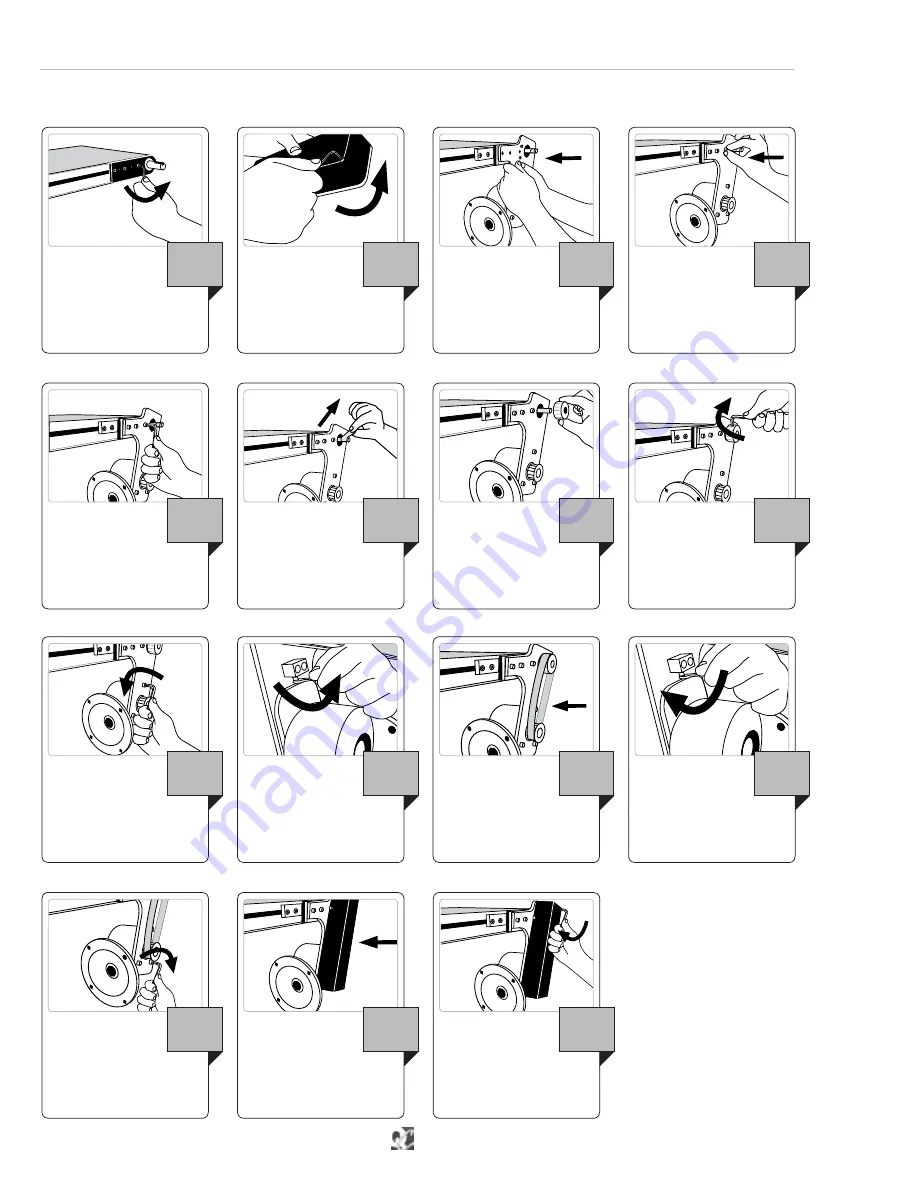
Run square head screw out,
moving speed reducer away
from conveyor and creating tension
on belt.
12
14 | Heavy Duty Top & Bottom Drive Mounting Packages — Drive Packages
AS40 Manual
Heavy Duty Top & Bottom Drive Mounting Packages
CARET-LEFT
DRIVE PACKAGES
Remove and discard three
socket head cap screws
from drive side bearing plate.
(Do not remove bearing plate)
1
Loosen three socket head
cap screws holding speed
reducer in position.
3
x
9
Tighten three socket
head screws.
5
Retighten three socket head
cap screws.
3
x
13
Replace guard.
14
Insert and tighten four
socket head cap screws.
4
x
15
Remove four socket head
cap screws from guard and
remove guard.
4
x
2
Tighten jacking screw so
speed reducer can move
toward conveyor.
10
Remove nylon tape holding
key in place.
(Do not remove key)
6
Mount drive package over
drive mounting plate.
3
Install timing belt
over sprockets.
11
Slide top sprocket onto
conveyor‘s output shaft
and key.
7
Align mounting holes
and install three socket
head screws.
3
x
4
Tighten set screws to secure
in place.
8
The Drive Package will ship separate from the conveyor. For Heavy Duty Drives, the motor is always shipped in its own box; the right angle
speed reducer will be attached to the drive mounting package.
3
x
3
x
2
x