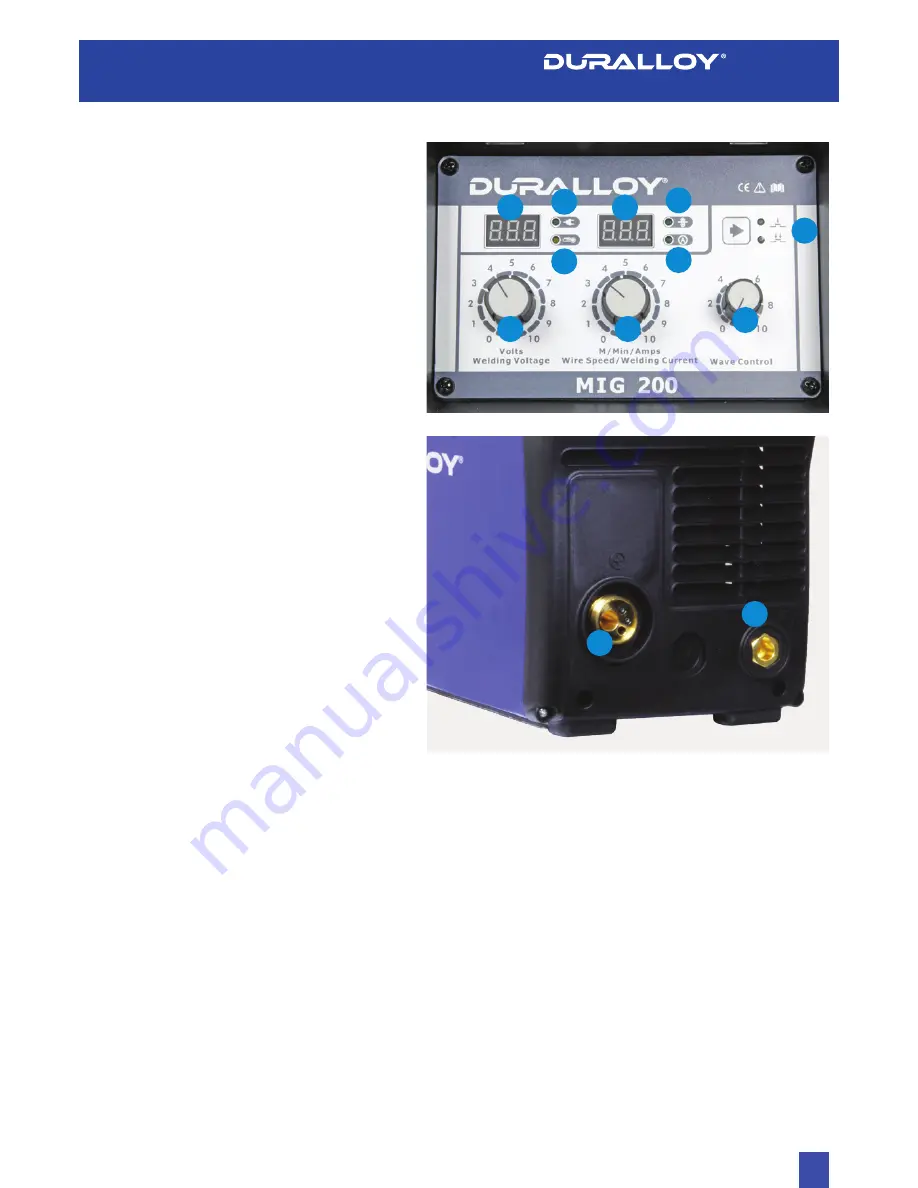
KNOW YOUR MACHINE
More detailed explanations of function on following pages.
1. MIG Wire Feed Speed
2. MIG Voltage
3. Wire Feed Speed/ Current Display Meter*
4. Power Indicator. Lights when input power connected and
machine switched On
5. Error/ Overload Indicator*
6. Display Value Indicator- Wire Feeding Speed
7. Display Value Indicator- Current
8. Trigger Switch Selector 2T/4T
9. Mig Wave Control/ Inductance Knob*
10. Display Value Indicator- Voltage
11. Negative (-) Welding Power Output Connection Socket
12. MIG Torch Euro Connection Socket
www.duralloy.net.au
|
1300 369 456
5
MIG Wire Feed Speed
This knob sets the wire feeding speed.
MIG Voltage
This knob sets the welding voltage.
Wire Feed Speed/ Current Display Meter
Displays wire feeding speed in m/minute prior to welding, during
welding displays welding current output.
Display Meter
Displays welding voltage.
Overload/ Error Indicator
Lights when over voltage, over current or electrical overheating
(due to exceeding duty cycle) is detected and protection is
activated. When protection is activated, welding output will be
disabled until the safety system senses the overload has reduced
sufficiently and indicator lamp goes out. May also trigger if
machine experiences an internal power circuit failure.
When protection is activated, welding output will be disabled until
the safety system senses the overload has reduced sufficiently
and indicator lamp goes out. May also trigger if machine
experiences an internal power circuit failure.
FURTHER CONTROLS EXPLAINED
1
2
3
6
10
9
8
11
12
MIG 200
OWNER’S MANUAL
7
4
5
Summary of Contents for MIG 200
Page 1: ...MIG 200 OWNER S MANUAL www duralloy net au 1300 369 456 ...
Page 9: ...www duralloy net au 1300 369 456 WIRING DIAGRAM 9 MIG 200 OWNER S MANUAL ...
Page 22: ...www duralloy net au 1300 369 456 22 MIG 200 OWNER S MANUAL ...
Page 23: ...www duralloy net au 1300 369 456 23 MIG 200 OWNER S MANUAL ...