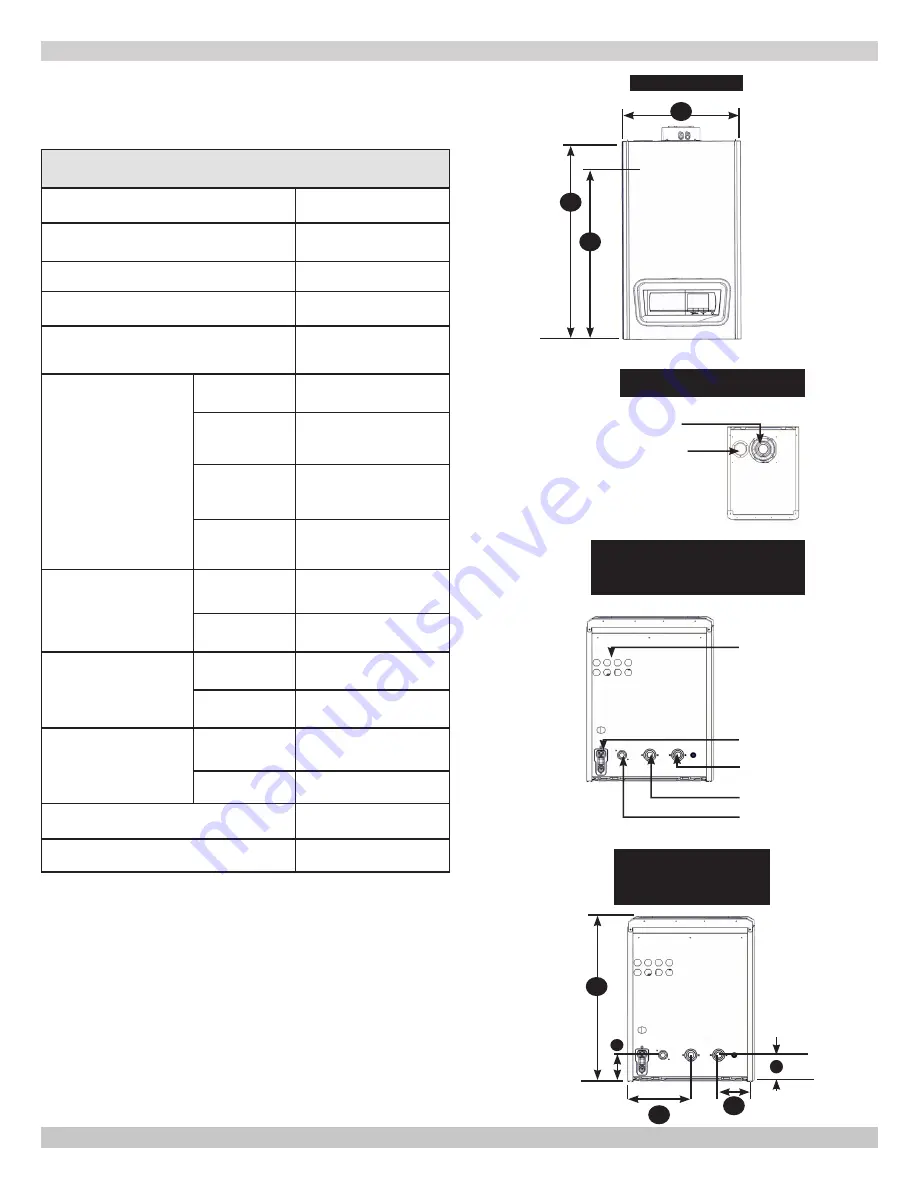
4
PHYSICAL DATA
Table 1: Physical Data
Model
240
Width (A)
17-¾" (450mm)
Height (B)
31-
¹
/
₁₆
" (763mm)
Depth (C)
23" (585mm)
Bracket (D) Location of Bracket on
back of unit
15-⅞" (403.2mm)
Water
Connections
Size
1" (25.4mm)
Location (G)
3-¾" (95.3mm)
Location (H)
Return
9" (228.6mm)
Location (I)
Supply
5" (127mm)
Gas
Connection
Location (J)
3-¾" (95.3mm)
Size
3/4" NPT
Condensate Drain
Connection
Location (J)
2-¼" (57.2mm)
Size
3/4" NPT
Weight
Shipping
145 LBS (65.8)
Unit
120 LBS (54.5kg)
Vent Connector
80/125 mm
Electrical Cord Length
5 ft. (1.5m)
Dimensions
Vent Connector
Combustion
Air
A
D
B
Front View
Top View
Bottom View
Dimensions
I
H
G
C
J
Condensate Drain
Connection
Return Water
Gas Connection
Bottom View
Connection
Identification
Supply Water
50 psi safety relief valve (3.44 bar)
Pressure relief valve connection 3/4"
(22.2m)
Wire Knockouts
P/N 240011656, Rev. E [07/30/2018]