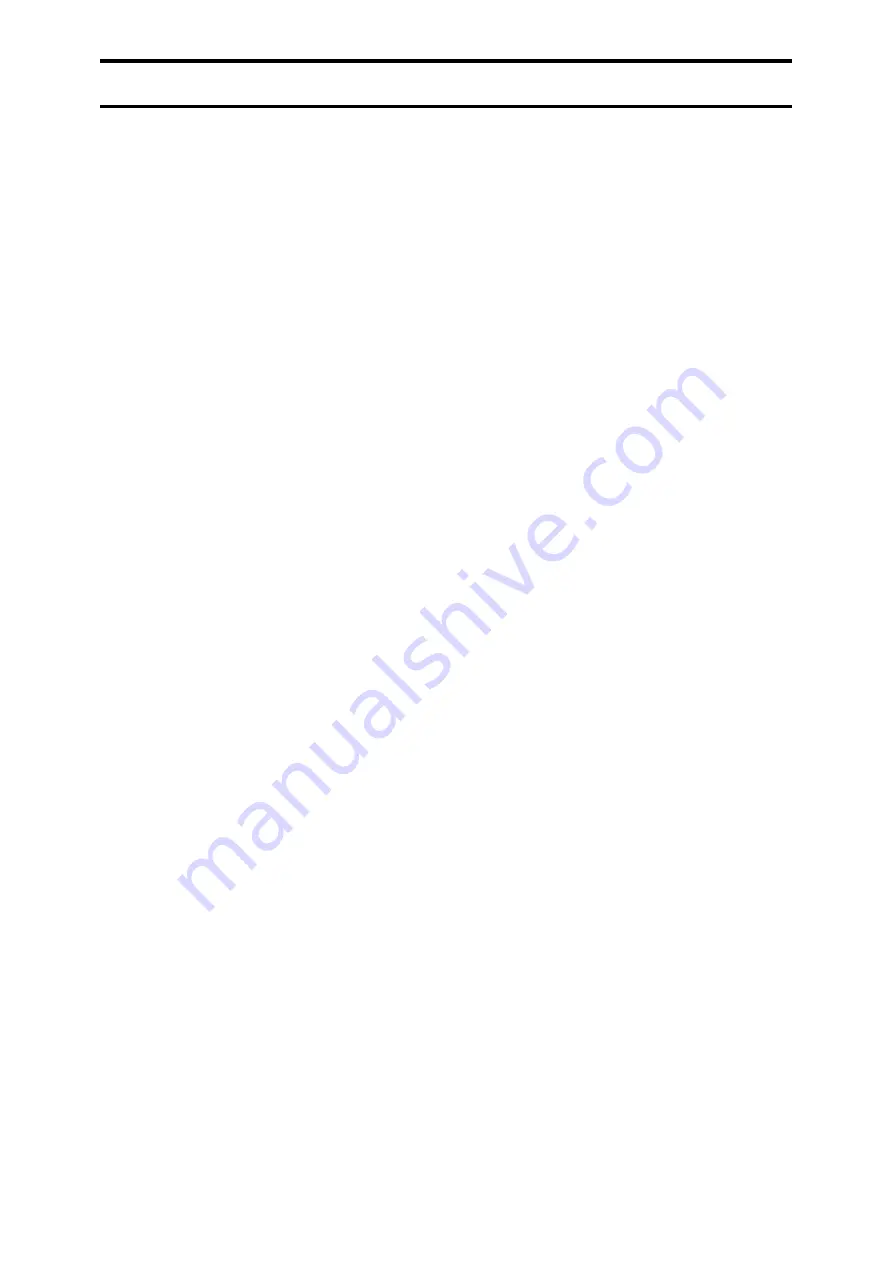
3.0 INSTALLATION
3.10 INSTALLATION
OF
DRIERS OR SIGHT
GLASS
1.) Break vacuum with nitrogen.
2.) When permanently brazed drier or sight
glass is used, open one valve on system to
atmosphere while maintaining slight
nitrogen flow.
3.) When flare connected drier or sight glass is
used, use similar procedure as under 2.
However, no valve need to be left open to
atmosphere.
4.) When replaceable dryer core is used follow
procedure as under 3. Insert drier core(s).
Tighten cap screws.
5.) Re-evacuate system to 1mmHg [0.133
kPa] absolute.
3.11 CHARGING
1.)
Connect refrigerant cylinder through
charging connection to charging valve.
2.) Loosen flare nut on other end of charging
connection and blow air out with
refrigerant. Tighten flare nut on charging
connection.
3.) Weight refrigerant cylinder.
4.)
Open charging valve and charge in
refrigerant vapor through suction access
valve until about 150psig [1034 kPa].
Switch to liquid line access valve and
charge in liquid refrigerant. Continue
charging with liquid refrigerant until clear
glass is observed.
5.) Shut off refrigerant charging valve but
keep connected. Check charging valve
flare nut for leak. Check and record down
discharge and suction pressure. If more
than one system to be charged, follow
procedure 1 through 4 for each system.
After all the systems have been done up to
step 4, proceed with 5 and 6.
6.) Shut off the system (compressor, fans,
pumps) and leave for 24 hours.
3.12 LUBRICATION
The scroll compressor use mineral oil 3GS, for
R22 compressors and POE (Polyol ester) oil
for HFC refrigerants (R134a, R407c etc)
compressors. Please refer to compressor name
plate for original oil charge. Recharge shall be
118ml less than the original charge. The
condenser fan used a direct-drive permanent
split capacitor motor. The motor should be
lubricated with 30 to 40 drops of SAE #20
non-detergent oil as follows depending on
service:
LIGHT DUTY
-After 25,000 operating
hours.
NORMAL DUTY
-Annually after three years
or 8,000 operating hours.
HEAVY DUTY
-Annually after one year
or at least every 1500 operating hours.
CAUTION: DO NOT OVER OIL
3.13 SENSING BULB
LOCATION
1.) Sensing bulb is not installed for the
evaporator unit due to limited space and
for precautionary reasons.
2.) The sensing bulb should be attached to a
horizontal suction line at the evaporator
outlet.
3.) If more than one TXV is used on
evaporator sections, make sure that the
sensing bulb of each valve is applied to the
suction line of the evaporator fed by that
valve.
4.) On suction lines 7/8” [22.2mm] OD and
larger, it is recommended that the bulb be
installed at 4 or 8 o’clock on the side of the
horizontal line and parallel with respect to
the direction of flow. On smaller lines, the
bulb should be mounted on the top of the
line. See Figure 3.13.
15