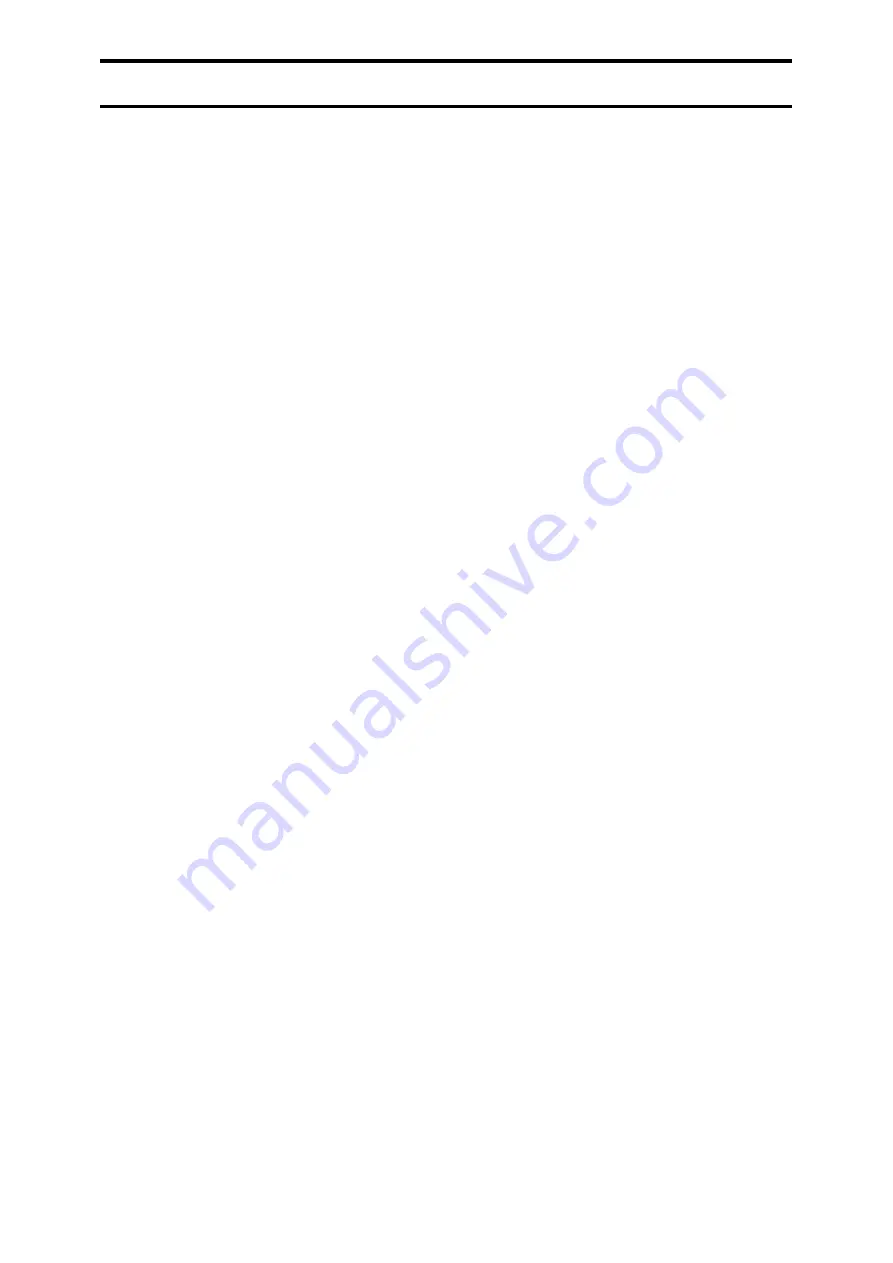
3.0 INSTALLATION
3.8 LEAK TEST (SYSTEM
PRESSURE TEST)
1.) Leak test pressure is at 200psig
[1380kPa]. Disconnect or shut off all
devices which may be damaged by
200psig [1380 kPa] test pressure.
2.) Open all valves in system so that entire
system can be pressurized and connect
refrigerant cylinder to charging
connection.
3.) Charge in freon vapor to the system until
50psig [345 kPa] and then pressurize with
dry nitrogen until 200psig [1380 kPa].
Stop charging gas if noise of escaping gas
is heard. Skip to sequence (6.)
Caution:
Always use inert gas such as
nitrogen for testing. Never use other gases
such as Oxygen or acetylene which may
be inflammable.
4.) With pressure at 200psig [1380kPa], shut
off the valve connecting nitrogen cylinder
to the system. Disconnect nitrogen
cylinder and leave pressure gauge
indicating 1380kPa connected to system.
5.) With halide torch or electronic leak
detector, leak check every valve, joint,
pressure control, coils and headers. Mark
every leak and record down as remarks.
6.) When all leaks have been found, blow off
charge through tube to outside to prevent
refrigerant accumulation around the
system.
7.) Repair all leaks (check off on your
remarks): If rebrazing is required, feed
nitrogen through into the system at
slightly excessive pressure (leave system
open and make sure nitrogen flows
through).
8.) After repairing leaks, re-check as per
procedure 1 through 7.
9.) When system tight after leak test, keep
pressurized at 200psig [1380kPa] and
hold for 12 hours. Full in pressure should
be negligible (some may be due to
temperature change only.)
10.)
When system is tight, proceed with
vacuum test and dehydration.
3.9 VACUUM TEST AND
DEHYDRATION
The purpose of evacuation is to evacuate the
system when it is known or suspected that the
system has been exposed to atmosphere, and
there is a possibility that moisture has entered
the system.
1.) Blow-off charge or pump down the
refrigerant.
2.) Connect vacuum pump the liquid line
valve and carefully check the unit piping to
ensure all passages are open. (NEVER
USE SYSTEM COMPRESSOR TO
EVACUATE).
3.) Start vacuum pump operation and pull
vacuum to about 2 to 2.5mmHg [0.26 to
0.33 kPa] absolute pressure. During
evacuation the pressure may remain steady
for sometime at about 0.5” or 12mmHg
[1.69 kPa] absolute pressure. This is
caused by moisture evaporating in the
system. This "boiling off" or "evaporation
period" last about the same period of time
as it took from initial start to reach this
point.
4.) When the "boiling off" period lasts longer
that indicated under 3, break vacuum with
refrigerant or nitrogen gas to sweep
moisture out and evacuate and dryer shells,
etc., up to a temperature of 100°F
[37.8°C].
5.) Break vacuum with refrigerant or nitrogen
gas until pressure is 0psig [0 kPa].
6.)
Re-evacuate to 1mmHg [0.133kPa]
absolute pressure.
7.)
Disconnect vacuum pump and leave
system standing for 6 hours. There should
be no change in vacuum during this period.
If there is a change repeat 1 to 7.
14