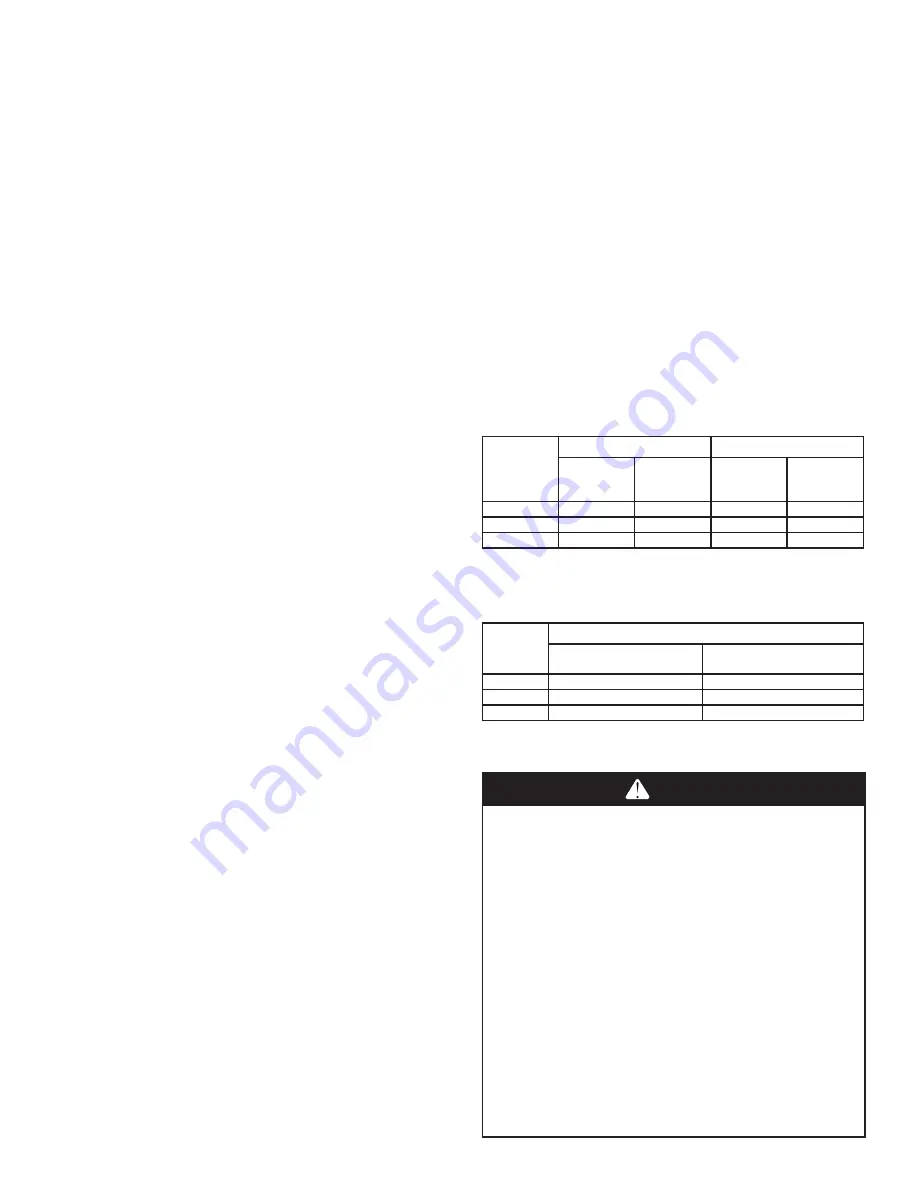
3
Section 1
Introduction
1-1. General
This manual provides instructions for the installation,
operation and maintenance of the Duff-Norton 6415 &
7415 Series A C actuator. It includes proper procedures
for the disassembly, cleaning, inspection, rebuilding
and assembly of the actuator. To ensure efficient, long,
satisfactory use of this unit, these instructions should be
followed closely.
1-2. Industrial Use Only
The actuators described and illustrated in this manual are
intended for industrial use only and should not be used
to lift, support or otherwise transport people, unless you
have a written statement from Duff-Norton Company
which authorizes this actuator unit, as used in your
application, as suitable for moving people.
1-3. Factory Preparation
Each actuator is carefully assembled and tested at the
factory to ensure that the motor and the mechanical
components will function properly and that the actuator
will lift its rated load.
The brake is preset at the factory and no further
adjustment is required. With proper maintenance, this
brake prevents the actuator from self-lowering.
The actuator is pre-lubricated at the factory and thus
requires minimum maintenance.
Limit switches are checked at the factory for proper
functioning.
External wires are provided for customer hookup. Wires
are color coded as to direction of travel of the actuator
(see wiring diagram, Figure 1-2).
1-4. Warranty and Warranty Repair
Subject to the conditions stated herein, Duff-Norton
will repair or replace, without charge, any parts proven
to Duff-Norton’s satisfaction to have been defective
in material and workmanship. Claims must be made
within one year after date of shipment. Duff-Norton will
not repair or replace any parts that become inoperative
because of improper maintenance, eccentric loading,
overloading, chemical or abrasive action, excessive heat,
or other abuse.
Equipment and accessories not of Duff-Norton’s
manufacture are warranted only to the extent that they
are warranted by their manufacturer, and only if the
claimed defect arose during normal use, applications and
service. Equipment which has been altered or modified
by anyone without Duff-Norton’s authorization is not
warranted by Duff-Norton. EXCEPT AS STATED HEREIN,
DUFF-NORTON MAKES NO OTHER WARRANTIES,
EXPRESS OR IMPLIED, INCLUDING WARRANTIES OF
MERCHANTABILITY AND FITNESS FOR A PARTICULAR
PURPOSE.
If you have any questions concerning warranty repair,
please contact the Duff-Norton Company. Authorization
for return must be received from the Duff-Norton
Company before returning any equipment for inspection
or warranty repair.
1-5. Specifications
Table 1-1. 6415 Series DC Actuator
Specifications
Applied
Load (lbs)
Speed (in.min)
Amps
Standard
115 Volt Mo-
tor (60 Hz)
Standard
220 Volt Mo-
tor (50 Hz)
Standard
115 Volt Mo-
tor (60 Hz)
Standard
220 Volt Mo-
tor (50 Hz)
500
52
44
5.00
1.70
1000
51
42
5.50
1.70
1500
50
41
6.20
2.00
Table 1-2. 6415 Series DC Super Pac Actuator
Duty Cycle
Applied
Load (lbs)
# Duty Cycle (in/hour)
Standard 115 Volt Motor
(60 Hz)
Standard 220 Volt Motor
(50 Hz)
500
560
675
1000
540
625
1500
500
600
# Total inches of travel (up and down) per hour with
equally timed intervals between cycles.
WARNING
1. Some actuator external surface temperatures may
reach 230°F at or near max. allowable duty cycle.
2. Do not operate actuator before setting limit
switches.
3. Position hooded vent to prevent moisture and
dirt from entering actuator (see instruction and
maintenance sheet).
4. The actuator is not recommended for use in
applications where it can be jammed. Examples of
jamming include overtraveling the limit switches and
jamming the nut and screw internally at the extreme
ends of the stroke, or driving the actuator against an
immovable object and thus overloading the actuator
severely. Therefore consult Duff-Norton Engineering
if jamming is expected.
Summary of Contents for 6415 Series
Page 15: ...15 Notes...