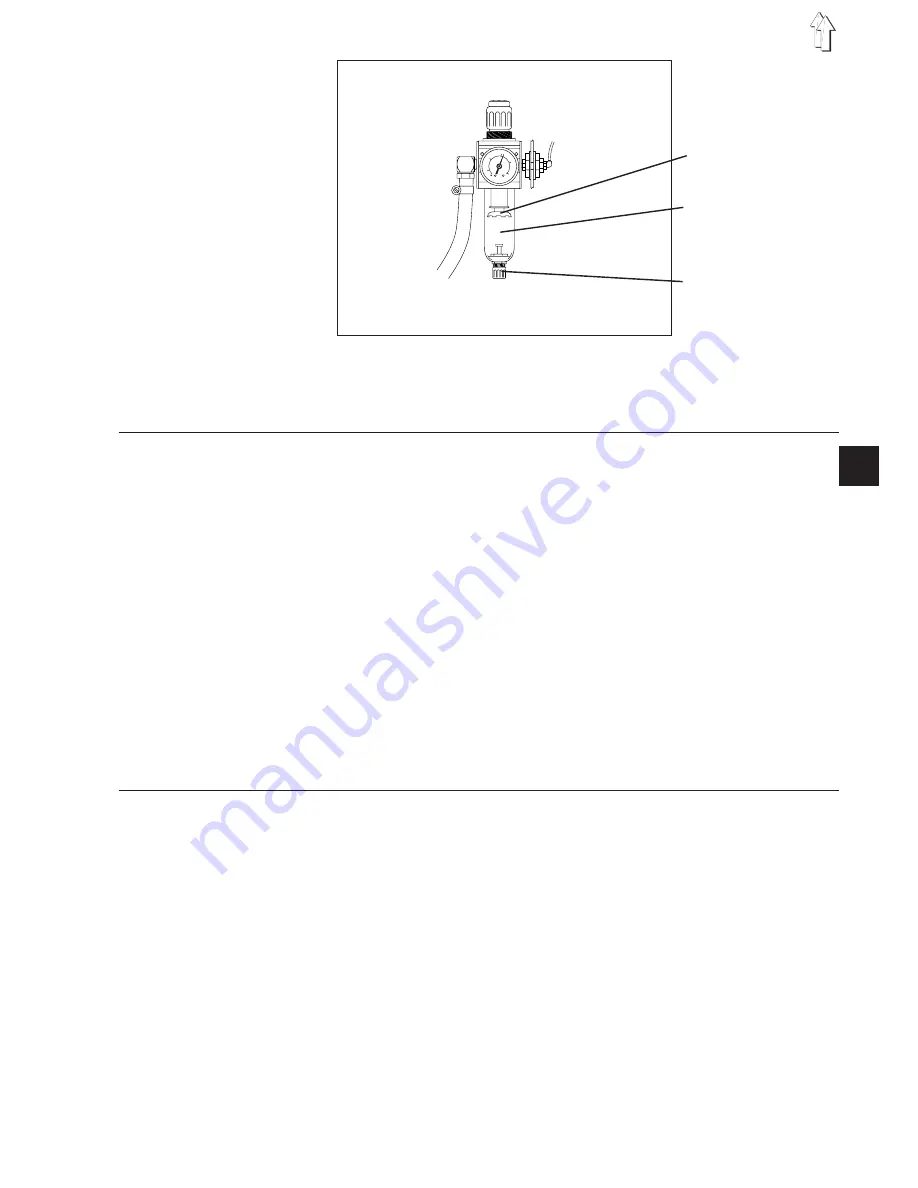
Maintenance work
Explanantion
Service
to be carried out
hours
Pneumatic System
- Check water level in the
pressure regulator.
- Clean the filter element.
- Check the tightness of the
system.
The water level should not reach the filter element 1.
- After turning-in the draining screw 3 drain the
water separator 2 under pressure.
The filter element 1 separates dirt and condensed wa-
ter.
- Disconnect the machine from the compressed air line.
- Turn-in the draining screw 3.
The pneumatic system of the machine must be
pressure-free.
- Unscrew the water separator 2.
- Unscrew the filter element 1.
Wash the dirty filter tray and the filter element with
petroleum benzine (no solvent!) and
blow clean by compressed air.
- Re-assemble the conditioning unit.
40
500
500
21
1
2
4
6
8
10
1
2
3