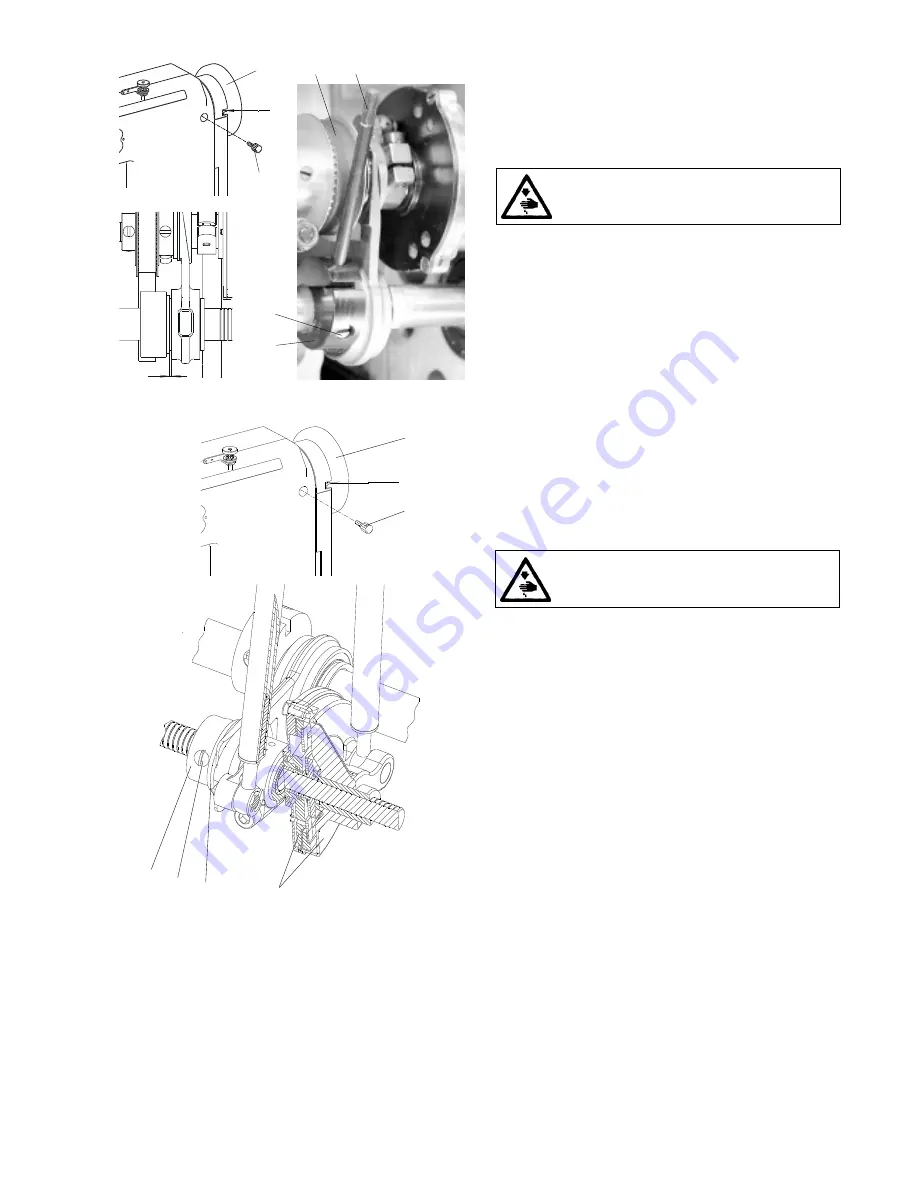
13
1
2
90
o
6
7
9
3
3
6
4
5
A
244
o
2
1
3.5.4.1.3 Setting of the lower eccentric
The rotation of the eccentric (3) must be delayed in phase by
1/4 revolution against the rotation of the eccentric of the stitch
length. This corresponds to the angle of 244
°
on the handwheel
(1), when the setting pin (4) is put into the eccentric (3) which
is in contact with the indented belt (5).
Caution! Danger of injury!
Switch off the main switch! Before starting the
setting operation, wait until the motor stops!
- Set 244
°
on the handwheel (1) and lock it with the screw
(2), which is included in the accessory of the machine
(tighten it carefully).
- Put the setting stick (4) into the hole in the eccentric (3) and
prop it from below against the indented belt (5).
- Set eccentric (3) axially.
- Tighten it the utmost the screws of the eccentric (6).
- By means of the handwheel, turn the eccentric (3) into the
marked position and check in this position the clearance
A = 0.05, proceed eventually to its correction by a new
side setting of the eccentric.
3.5.4.1.4 Setting the engagement and
disengagement of the clutches
The nut (7) is to be side set in such a way that the shifting of
the clutches is done at the moment when the clutch disks (3)
do not move, which means, when they are at the dead center
of their oscillating movement. This corresponds to the angle
90
°
on the handwheel.
Caution! Danger of injury!
Switch off the main switch! Before starting the
setting operation, wait until the motor stops!
- Loosen the screws of the indented pulley of feeding and
shift it to the left.
- Set the maximum stitch length.
- Set the angle 90
°
on the handwheel and lock it with the
screw (2). which is included in the accessory of the machine
(tighten it carefully).
- Loosen three screws (6) in the nut (7) and unscrew it by
2 mm to the left.
- Tighten slowly the nut (7), until it strikes against the axial
bearing (9). (At this moment, the tightening moment
increases in jumps) and tighten the screws (6).
- Set the the handwheel on 85
°
and push the backtacking
lever, the feeder is to turn against the movement of the
needle. Set then the handwheel on 95
°
, the feeder is to be
turned in the sense of the needle movement. If not being
so, correct the side setting of the nut (7). When the clutches
shift too soon, turn a bit the nut (7) to the right and inversely.
- Tighten the screws (6).
- Return the indented pulley in its original place according to
the paragraph 3.6.2.