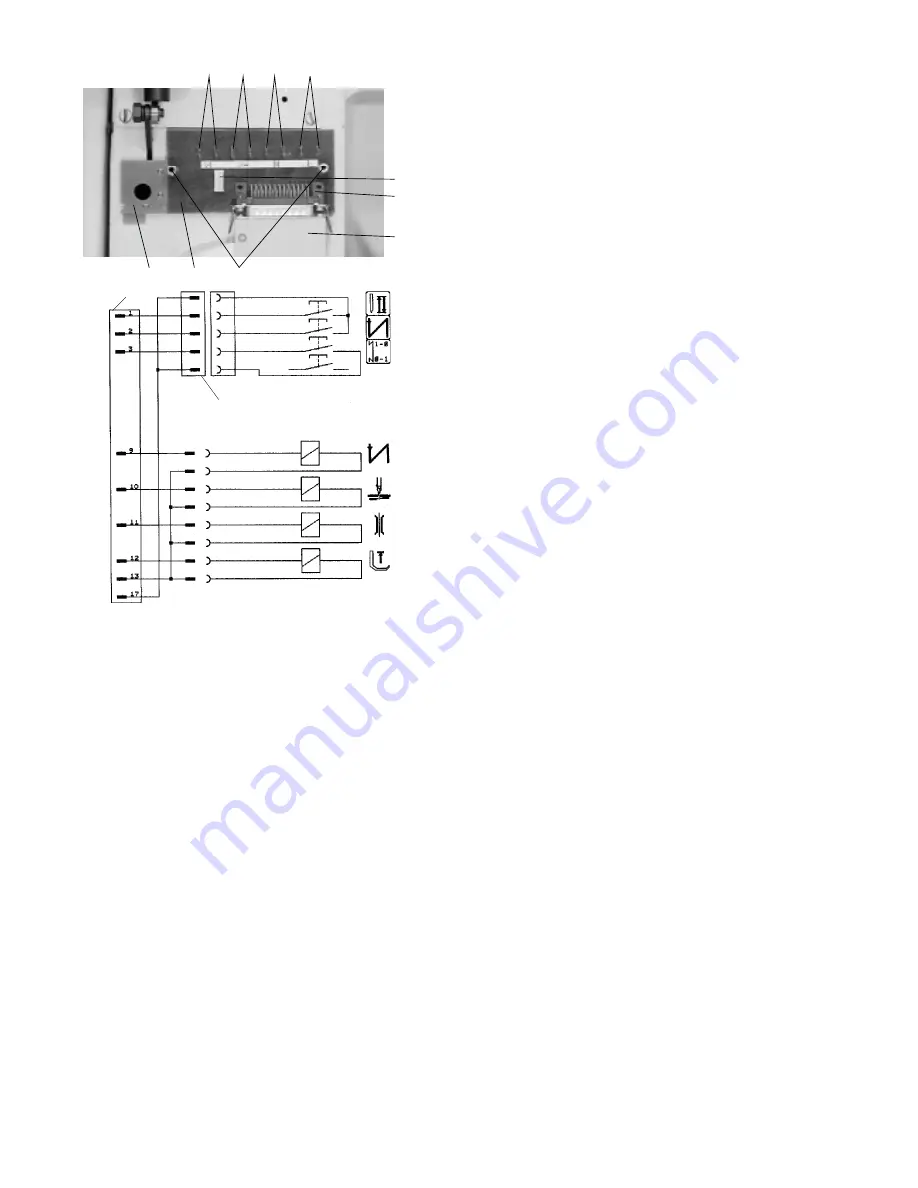
28
4
5
6
7
10
8
9
2
1
3
9
8
4
5
6
7
7. Connecting the electric elements on the
machine head
The connection of the electric elements (electromagnets,
backtacking, presser foot lifting, thread trimming, loosening
of the tensioner and push-buttons) is made by means of a
switchboard (1) fixed with its supporting plate (2) on the rear
side of the head by means of two distance screws (3) (In the
Fig., these electric elements are disconnected).
Connecting spots :
4 - backtacking electromagnet
5 - trimming electromagnet
6 - tensioner loosening electromagnet
7 - presser foot lifting electromagnet
8 - connector of push-button connecting
9 - connector of coupling the head with the stopmotor
10 - connecting cable of the head and stopmotor
Wiring diagram of connecting the electric elements of the
machine head.
8. Drive, control panel, position sensor
The detailed information concerning the drive, the control
panel and the setting of the position sensor is given in the
manual of the drive and of the control panel.