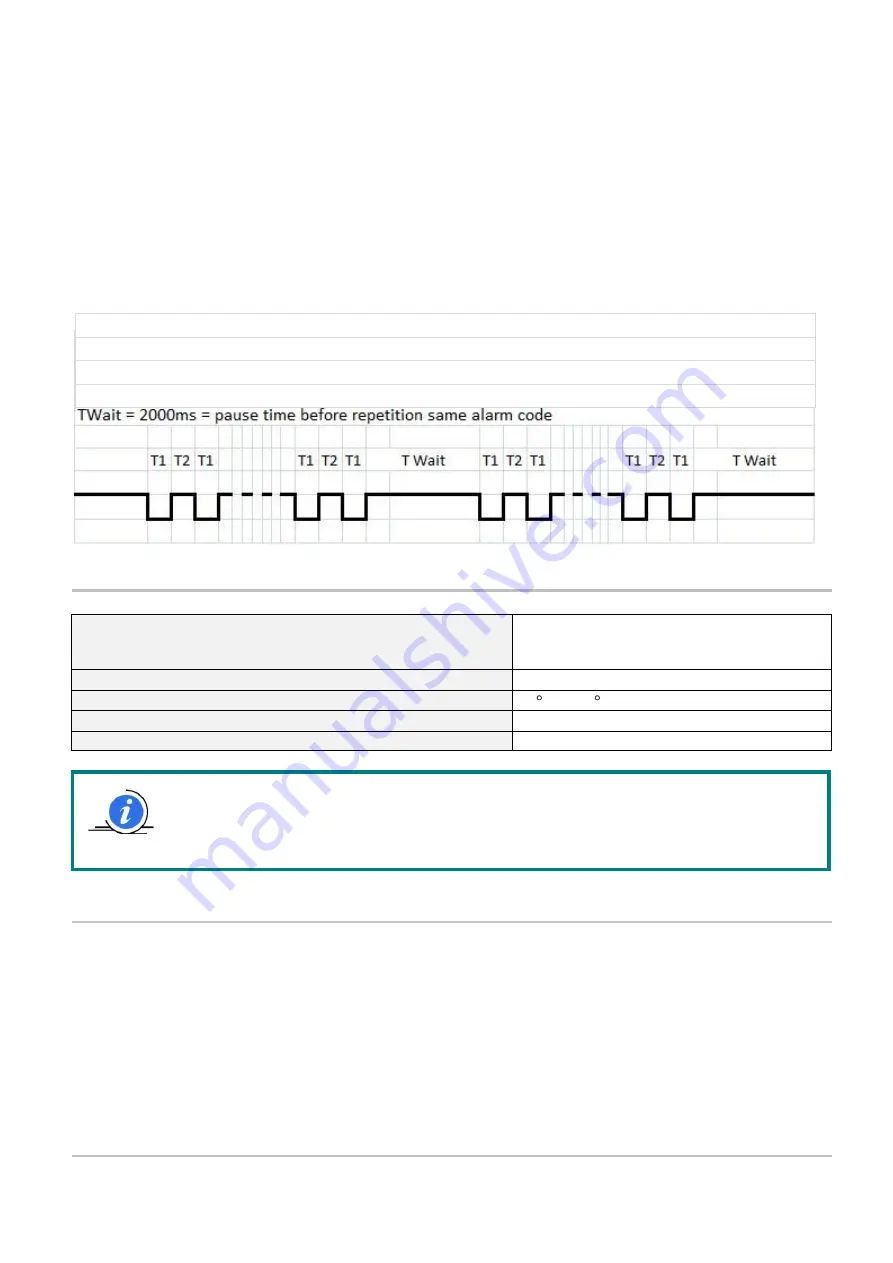
24/29
10.3 REMOTE CODED ALARM FUNCTION
The VIP5 controller has the ability to use a remote pulsed coded alarm contact.
Every time the VIP5 control enters an alarm condition, the remote alarm relay contact is activated.
Most alarm contacts are simply a NC or NO contact that gives a remote system indication that the local controller is in a
fault condition.
Additionally, the VIP5 can trigger the alarm according to the alarm code being generated and allow a remote PLC (or even
a remote LAMP signal) to read the number of the alarm being generated.
This is done by pulsing the alarm relay in 500ms bursts with a 2000ms gap between each signal burst.
The timing chart below shows how to interface the logic with your PLC.
11. TECHNICAL SPECIFICATIONS
OPERATING VOLTAGE
12/24 Vdc/ac (1639141)
110V~ (1639142)
230V~ (1639140)
Power consumption
2,5W
Temperature Operating Range
- 5 C ÷ + 70 C
Permissible Temperature storage range
- 20°C ÷ + 80 °C)
Operating Relative Humidity
90% max
12. MAINTENANCE PROCEDURES
VIP05
has been designed not to require any regular maintenance. We recommend to occasionally clean the unit with a
damp cloth, not using solvents
The battery life is approximately 10 years. In the event that the battery needs to be replaced you should note that there
are two possible battery types.
a)
A Soldered type battery that must be removed and re-soldered.
This type of battery can be obtain from Panasonic PART NUMBER BT-CR2032-H,
easily purchased all over the world.
b)
The replaceable type battery can be simply removed and replaced.
This type of battery can be obtain from Panasonic PART NUMBER CR2032, easily purchased all over the world.
Alarm code= number of (T1+T2)
T1= 500ms = alarm contact activation time
T2= 500ms = alarm contact deactivation time
TWait= 2000ms= pause time before repetition of same alarm code
Note
:
To ensure that seal of the casing is guaranteed alone use appropriate cable glands that provide
adequate protection.. If the cable glands are not sufficient in number for your configuration, use a multi-
connector solution and a cabling harness that will ensure adequate sealing and avoid torsion and tension
on the cable.