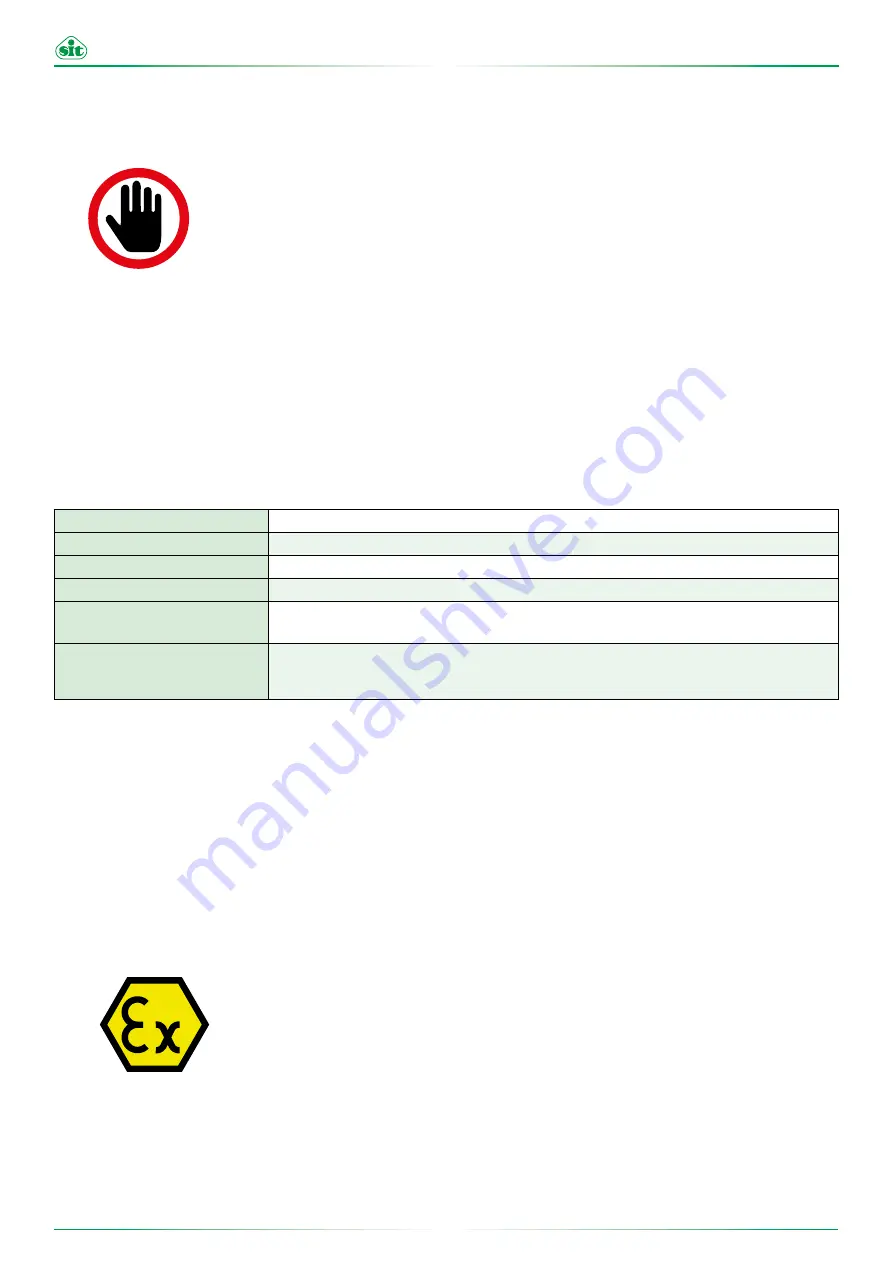
www.sitspa.com
TRASCO
®
- User and Maintenance Manual
114.02 - Rev. 2 - 2
nd
March 2020
Approved by: SIT S.p.A.
5
1.4 General advice in case of danger
1.5 Reference laws and standards
2
Characteristics of TRASCO
®
couplings
DANGER!
Every operation performed on the coupling, either with mounting or
maintenance, must be carried out with the machine not connected
to the power supply. Accidental contact with the rotating parts can
cause serious injury to the operator. It is recommended to read these
operating instructions to ensure safety.
STOP
• Affix proper warning signs around the machine
• Instruct the operator before giving permission to work on the coupling
• Operate on the coupling and on the transmission in safe conditions
• Make sure the machine power is disconnected before carrying out any operation
• Do not touch any moving part of the machine and wait until it stops completely
• Protect the coupling against accidental contact with protection devices
This evaluation was carried out in accordance with the provisions of the relevant laws, directives, standards mentioned below:
TRASCO
®
couplings are a flexible and constant-velocity coupling that ensures maximum performance with same overall dimensions.
It is very compact and allows a safe transmission of motion between the motor and the driven machine, absorbing shocks and torsional
vibrations. It also allows, through the elastic deformation of the elastic spider, to compensate for angular, radial and axial misalignments
due to small variations in length of the shafts. The hub teeth and spider profiles are designed so as to obtain a uniform pressure
distribution.
The elastic element is subject only to compression stress and does not induce any axial or radial stresses, providing the TRASCO
®
coupling with great load capacity and durability. The coupling can be assembled both horizontally and vertically, and it correctly tolerates
load variations and reversals.
DIN 740/2
Reference standard for flexible couplings
ATEX DIRECTIVE 2014/34/EU
Equipment and protective systems intended for use in potentially explosive atmospheres
ATEX GUIDELINES 2014/34/EU
Guidelines to the application of Directive 2014/34/EU
EN 1127-1:2011
Explosion prevention and protection against explosion. Basic concepts and methodology
EN ISO 80079-36:2016
Explosive environments – part 36. Non-electrical equipment for potentially explosive atmospheres.
Basic method and requirements
EN ISO 80079-37:2016
Explosive environments – part 37. Non-electrical equipment for potentially explosive atmospheres.
Non-electrical equipment constructional safety type "c", control of the sources of ignition type “b”,
immersion in liquid type “k”.
The TRASCO
®
series is suitable for use in areas classified with the
presence of flammable gases, vapours and mists or combustible
dusts (Zone 1/21, category 2 GD, EPL Gb Db) and applications in
mining (Group I, category M2, EPL Mb).
It is designed and built in accordance with the ATEX Directive
2014/34/EU and in accordance with the following European
standards:
•
EN 1127-1:2011
•
EN ISO 80079-36:2016
•
EN ISO 80079-36:2016