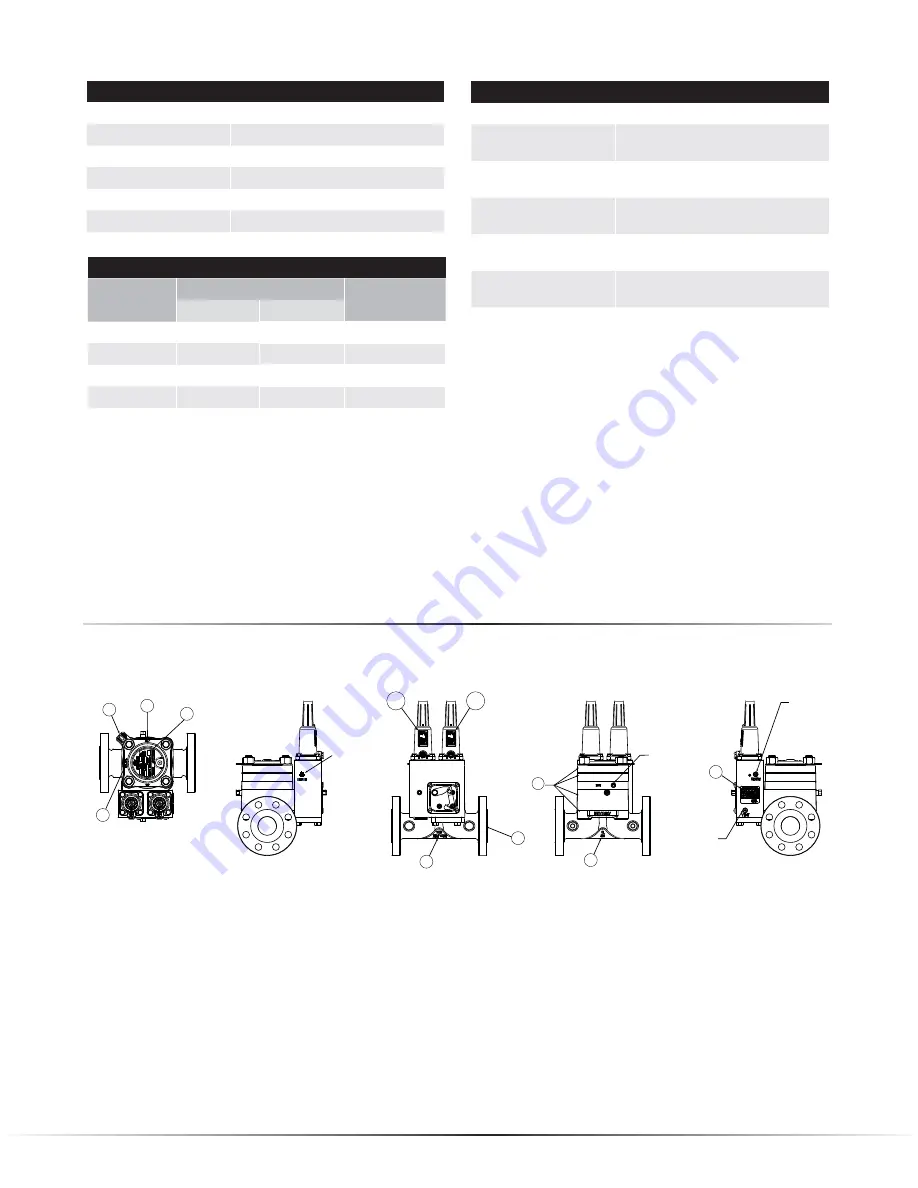
1
9,10
9,10
2
B-16
300
B-16
300
5
Vent Port
Slam
Shut
Sense
Port
8
7
6
7
3
4
1234
1234
1234
1234
1234
Sense Port
(Optional)
Pilot
Inlet
Supply
Port
2
|
Dresser
Materials of Construction
Housing Module
Carbon Steel (WCB)
Flapper Valve
SST
Controller
Aluminum
Springs
SST
Diaphragms
Standard: Nitrile
O-Ring & Seals
Standard: Nitrile
Specifications for 2", 3" and 4"
Sizes
2, 3, 4 inch sizes
Types
Stand Alone or Integrated into Flowgrid
Regulator
Pressure Protection
Standard: Over
Optional: Over and/or Under
Temperature**
-20°F to 150°F
(-29°C to 65°F)
Maximum Operating
Inlet Pressure
740 psig (50 Bar)
Operating Sense
Pressure
10 to 450 psig
(0.7 Bar to 31 Bar)
Response time
< .25 seconds
Spring Range and Accuracy
Spring Color
Outlet Pressure Range
Accuracy (% of
Set Point)*
psig
Bar
Plated
10-40
0.7 - 3
5
Blue
40-90
3 - 6
2.5
Purple
90-175
6 - 12
2.5
Black
175-250
12 - 17
2.5
White/Green
250-450
17 - 31
2.5
Under Pressure Inlet Pressure Sensitivity:
for data contact Dresser factory engineering.
Figure 3 – Valve Markings
Valve Markings
1. American National Standards Institute (ANSI) pressure
class rating of the valve.
2. ANSI pressure class rating of the flange.
3. Indication that the valve has been hydrostatically tested
according to code requirements.
4. The serial number for the Flowgrid Regulator and Shut
Off Valve is stamped on the spring case, spacer, seal
retainer, slam shut body, and body on Flowgrid regula-
tors with integral slam shuts. On Mooney Slam Shut
Valves (stand alone) the serial number is stamped on the
cover, seal retainer, slam shut body, and body.