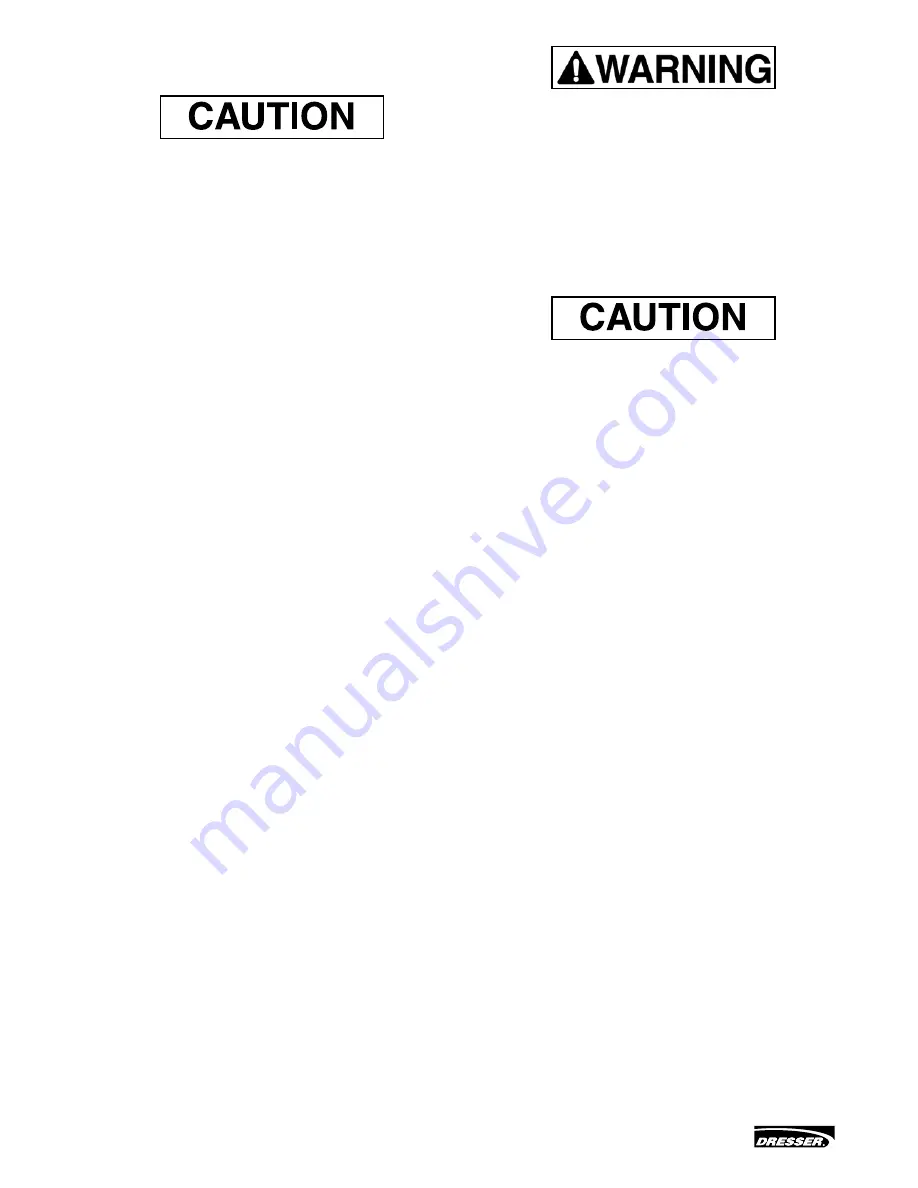
14
Instructions EM36005 – 07/10
36005 Series V-Max
®
Control Ball Valve
g. Remove the upper diaphragm case (84) and
diaphragm (85).
The diaphragm plate (88) remains under spring
load.
3.6.1.2 Reassembly
A. Ensure that sealing surfaces of diaphragm cases
(84) and (91) are clean and free of any dirt or
debris. Check that there are no foreign objects that
may interfere with travel or damage diaphragm.
B. Install diaphragm (85) on diaphragm plate (88).
Align bolt holes with holes in lower case (91).
C. Install three tension bolts (95) with warning
plates (97) into upper case (84). Ensure bolts
are equally spaced at 120° to each other.
D. Mount upper case (84) onto diaphragm plate
(88) such that the tension bolts pass through
holes in diaphragm (85) and lower case (91).
E. Install tension nuts (96) finger tight onto tension
bolts (95).
F. Tighten each tension nut (96) three turns before
proceeding to the next to ensure actuator spring
(90) is evenly loaded. Continue until the diaphragm
is firmly sandwiched between the flanges of the
upper and lower diaphragm cases. Torque tighten
tension bolts to 50 in. lbs.
g. Install cap screws (86) and nuts (87). Torque
tighten to 50 in. lbs. in a criss-cross pattern. As this
will tend to unload the tension bolts (96) repeat
torque tightening of tension bolts and cap screws
(86) to 50 in. lbs. in a criss-cross pattern until joint
is evenly loaded to specified torque values.
H. Reconnect air supply.
I. Stroke actuator to confirm operation.
3.6.2 Model 33 size AC actuators only. Refer to
section 3.6.1 for sizes B & C.
3.6.2.1 Disassembly
A. Relieve actuator pressure and disconnect air
supply. Do not remove pivot pin (39).
B. Verify that all three tension bolts (95) and nuts
(96) are in place and secure.
C. Remove nuts (87) and cap screws (86) following
a criss-cross pattern.
D. Verify actuator stem (15) and rod end (94) are
securely connected to lever (32) through pivot
pin (39) and that retaining clips (40) are in place.
E. Loosen tension nuts (96) evenly in sequence.
Do not exceed three turns of any one nut (96)
before proceeding to the next one. Do not vary
the sequence.
Failure to evenly unload tension nuts may result
in personal injury!
F. Continue loosening tension nuts (96) until further
loosening of the tension nuts (96) is no longer
accompanied by an increase in separation of the
upper diaphragm case (84) from the lower case
(91). At this point the tension nuts (96), bolts (95)
and warning plates (97) can be removed.
g. Remove the upper diaphragm case (84) and
diaphragm (85).
The diaphragm plate (88) remains under spring
load.
3.6.2.2 Reassembly
A. Ensure that sealing surfaces of diaphragm cases
(84) and (91) are clean and free of any dirt or
debris. Check that there are no foreign objects that
may interfere with travel or damage diaphragm.
B. Install diaphragm (85) on diaphragm plate (88).
Align bolt holes with holes in lower case (91).
C. Install three tension bolts (95) with warning plates
(97) into upper case (84). Ensure bolts are equally
spaced around the circumference of the case.
D. Mount upper case (84) onto diaphragm plate
(88) such that the tension bolts pass through
holes in diaphragm (85) and lower case (91).
E. Install tension nuts (96) finger tight onto tension
bolts (95).
F. Tighten each tension nut (86) three turns before
proceeding to the next to ensure actuator spring
(90) is evenly loaded. Continue until the diaphragm
is firmly sandwiched between the flanges of the
upper and lower diaphragm cases. Torque tighten
tension bolts to 50 in. lbs.
g. Install cap screws (86) and nuts (87). Torque
tighten to 50 in. lbs. in a criss-cross pattern. As this
will tend to unload the tension bolts (95) repeat
torque tightening of tension bolts and cap screws
(86) to 50 in. lbs. in a criss-cross pattern until joint
is evenly loaded to specified torque values.
H. Reconnect air supply.
I. Stroke actuator to confirm operation.