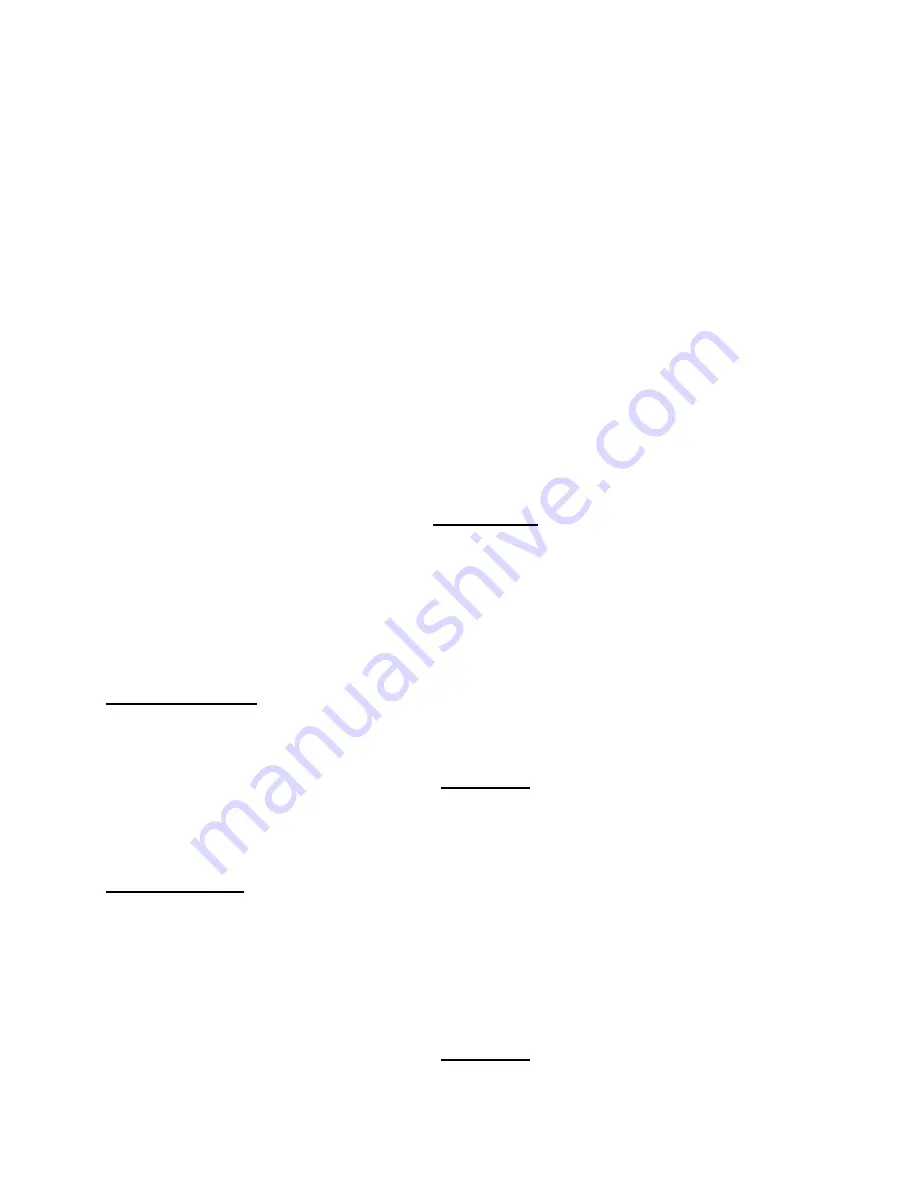
A7
The installation must be made with a connector that meets with the standard for connectors movable
gas appliances ANSI Z21.69-XX and a Quick-disconnect device that complies with the standard for
Quick-disconnect devices for use with gas fuel ANSI Z21.41-XX and addenda Z21.41a-XX and
Z21.41b-XX. Refer to last edition year for XX. It must also be installed with restraining device
(chain comes with the oven) to guard against transmission of strain to the gas supply and connectors.
The pipe fittings compound must be certified for gas.
The customer must install a manual shut off valve at the end of the gas supply pipe near the burner
which is approved by the American Gas Association Standard in the United States and with the
Canadian Gas Association in Canada.
Exhaust: A draft hood is provided with the unit and it must be used when the chimney is directly
connected to a gas vent pipe. The exhaust pipe must be certified for use of gases.
Clean the air contained in the gas supply pipe at the installation to insure a successful firing on the
first try. The gas pipe sealing compound tightness must be verified using a solution of water and soap
prior to firing the unit.
ATTENTION
Make sure not to obstruct the overpressure opening on the gas regulator.
NOTE:
If there's any modification done to the system or change of the type of gas used,
make sure that the regulator pressure of the burner is adjusted as recommended in this
manual.
2. To the electrician
Electrical supply installation must be in accordance with the electrical rating on the nameplate.
WARNING
The electrician must make sure that the supply cable does not come in contact
with the oven top which becomes hot.
3. To the plumber
This equipment is to be installed to comply with the applicable federal, state or local plumbing codes.
Connect the steam system (1/4 NPT) to the cold water distribution network.
We highly recommend a water softener to eliminate minerals in the water. We suggest you to use
CUNO # CFS6135 (Doyon part number PLF240).
WARNING
Do not adjust the needle valves, it has been done at the factory.
Summary of Contents for JA10G
Page 24: ...SECTION B DIMENSIONS ...
Page 27: ...B3 35 55 1 4 38 30 5 8 JA10G JA10G SLIDING DOORS ...
Page 31: ...B7 81 1 4 55 1 4 30 5 8 JAOP10G JAOP10G SLIDING DOORS ...
Page 35: ...B11 86 1 2 55 1 4 30 1 4 JA20G JA20G SLIDING DOORS ...
Page 37: ...SECTION C BURNER ADJUSTMENTS ...
Page 40: ...SECTION E COMPONENT PARTS ...
Page 44: ...E4 AND ELI240 INFINITY SWITCH KNOB 1 20 ELB097 20A BREAKER 2 Model JAOP10 G View FRONT ...
Page 45: ...E5 1 2 3 5 4 6 7 8 9 10 JAOP10G JAOP10G SLIDING DOORS ...
Page 47: ...E7 Dwyer 25 0 45 0 350 150 550 OFF 1 2 3 4 5 6 7 8 9 10 11 12 JAOP10G JAOP10G ...
Page 49: ...SECTION F CONTROL PANELS ...
Page 58: ...SECTION G ELECTRIC SCHEMATICS ...