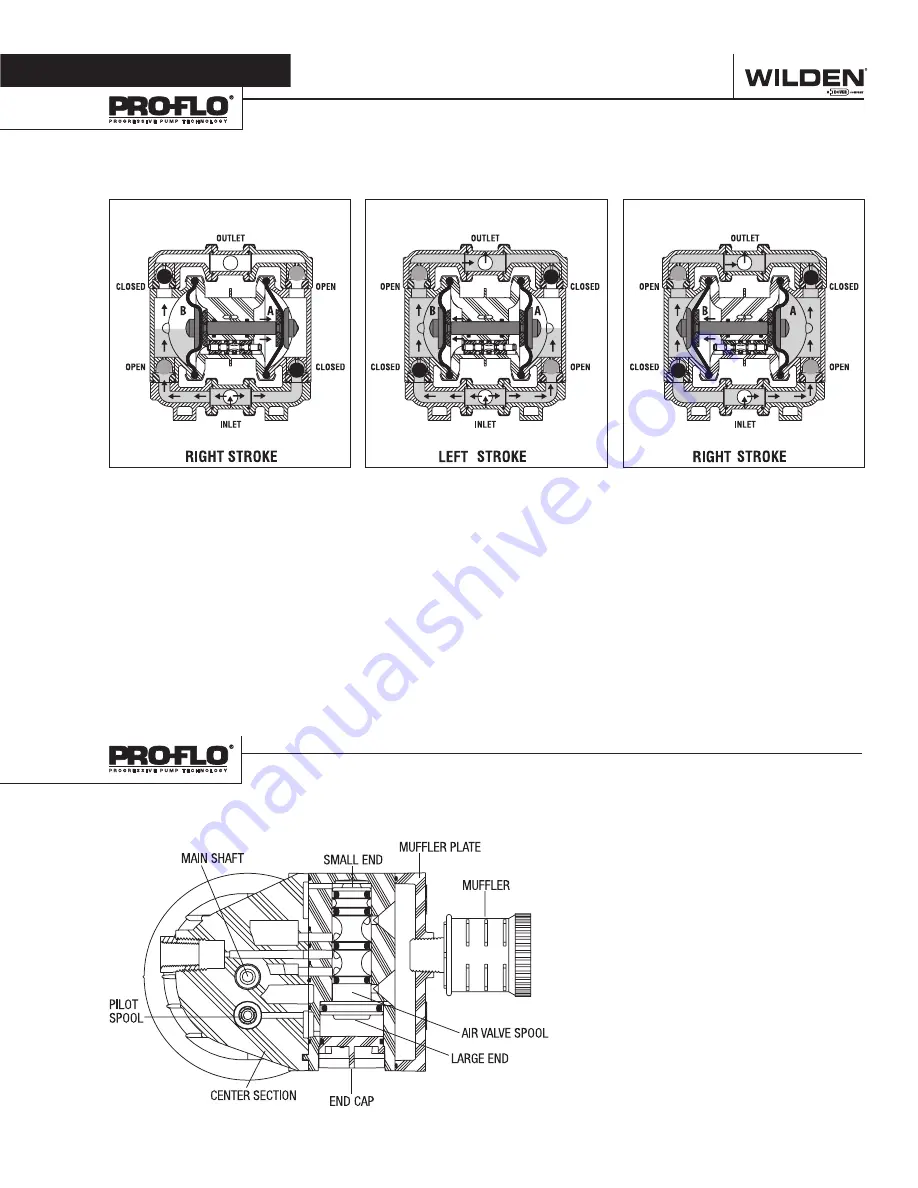
The Wilden diaphragm pump is an air-operated, positive displacement, self-priming pump. These drawings show the flow
pattern through the pump upon its initial stroke. It is assumed the pump has no fluid in it prior to its initial stroke.
FIGURE 1 The air valve directs pressurized air to
the back side of diaphragm A. The compressed air
is applied directly to the liquid column separated by
elastomeric diaphragms. The diaphragm acts as a
separation membrane between the compressed air
and liquid, balancing the load and removing mechan-
ical stress from the diaphragm. The compressed air
moves the diaphragm away from the center block of
the pump. The opposite diaphragm is pulled in by
the shaft connected to the pressurized diaphragm.
Diaphragm B is on its suction stroke; air behind the
diaphragm has been forced out to the atmosphere
through the exhaust port of the pump. The move-
ment of diaphragm B toward the center block of the
pump creates a vacuum within chamber B. Atmo-
spheric pressure forces fluid into the inlet manifold
forcing the inlet valve ball off its seat. Liquid is free
to move past the inlet valve ball and fill the liquid
chamber (see shaded area).
FIGURE 2 When the pressurized diaphragm,
diaphragm A, reaches the limit of its discharge
stroke, the air valve redirects pressurized air to the
back side of diaphragm B. The pressurized air forces
diaphragm B away from the center block while pull-
ing diaphragm A to the center block. Diaphragm B
is now on its discharge stroke. Diaphragm B forces
the inlet valve ball onto its seat due to the hydraulic
forces developed in the liquid chamber and mani-
fold of the pump. These same hydraulic forces
lift the discharge valve ball off its seat, while the
opposite discharge valve ball is forced onto its seat,
forcing fluid to flow through the pump discharge.
The movement of diaphragm A toward the center
block of the pump creates a vacuum within liquid
chamber A. Atmospheric pressure forces fluid into
the inlet manifold of the pump. The inlet valve ball is
forced off its seat allowing the fluid being pumped
to fill the liquid chamber.
FIGURE 3 At completion of the stroke, the air valve
again redirects air to the back side of diaphragm A,
which starts diaphragm B on its exhaust stroke. As
the pump reaches its original starting point, each
diaphragm has gone through one exhaust and one
discharge stroke. This constitutes one complete
pumping cycle. The pump may take several cycles
to completely prime depending on the conditions
of the application.
The Pro-Flo
®
patented air distribution system
incorporates three moving parts: the air valve
spool, the pilot spool, and the main shaft/dia-
phragm assembly. The heart of the system
is the air valve spool and air valve. As shown
in Figure A, this valve design incorporates an
unbalanced spool. The smaller end of the spool
is pressurized continuously, while the large end
is alternately pressurized then exhausted to
move the spool. The spool directs pressurized
air to one air chamber while exhausting the
other. The air causes the main shaft/diaphragm
assembly to shift to one side — discharging
liquid on that side and pulling liquid in on the
other side. When the shaft reaches the end of
its stroke, the inner piston actuates the pilot
spool, which pressurizes and exhausts the large
end of the air valve spool. The repositioning of
the air valve spool routes the air to the other air
chamber.
Figure A
3
WILDEN PUMP & ENGINEERING, LLC
WIL-10140-E-08
S e c t i o n 3
H O W I T W O R K S — P U M P
H O W I T W O R K S — A I R D I S T R I B U T I O N S Y S T E M
Summary of Contents for Wilden Original P1
Page 21: ...S e c t i o n 5 N O T E S ...