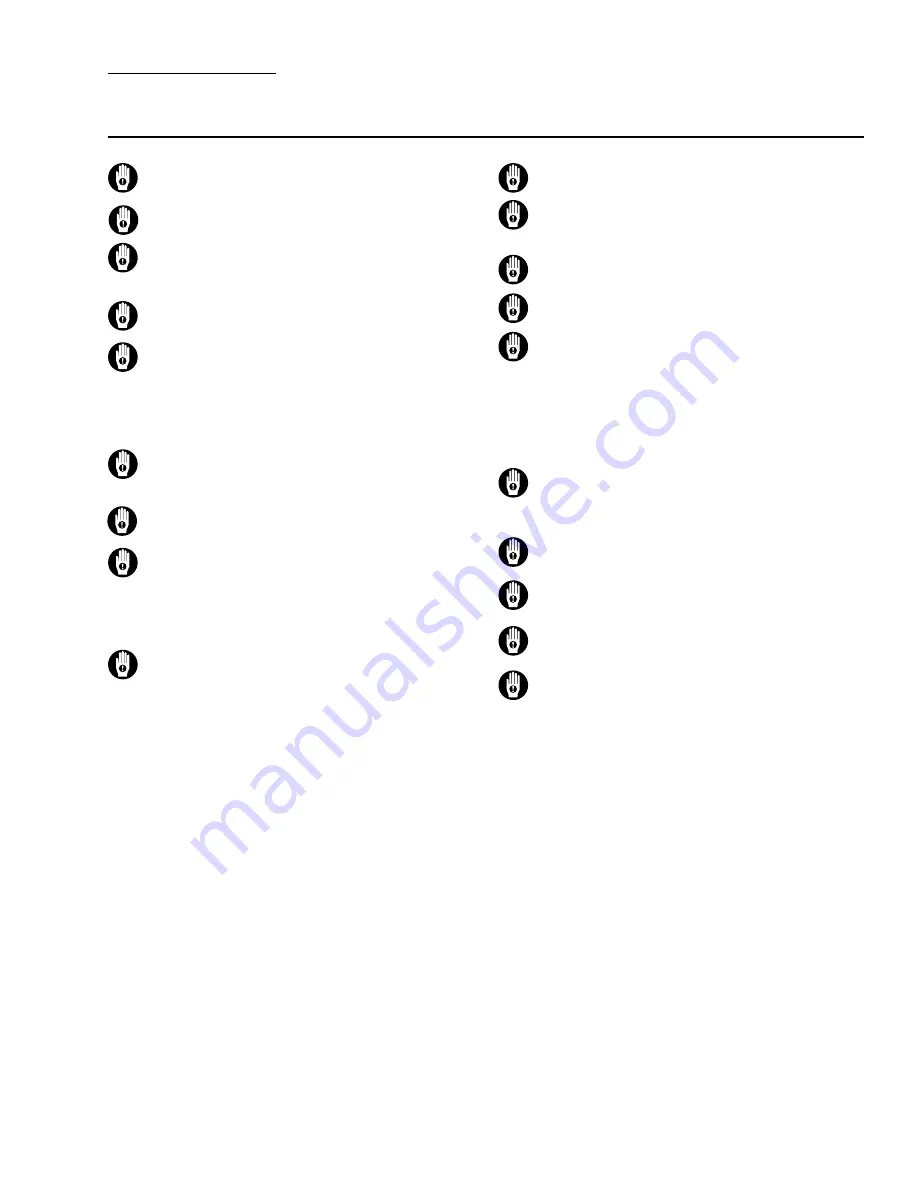
SECTION 3
WILDEN MODEL H25/1600S
CAUTIONS — READ FIRST!
PUMP TEMPERATURE LIMITS
-12.2°C to 65.6°C 10°F to 150°F
CAUTION:
The H25/1600S is designed for open loop
systems.
CAUTION:
The liquid discharge pressure generated by
this pump is approximately 13 times the inlet air
pressure supplied.
CAUTION:
Do not apply compressed air to the
exhaust ports — pump will not function.
CAUTION:
The model H25/1600S is designed to pump
clean fluid such as hydraulic fluid and should not be
used for pumping solid objects or particles. Whenever
the possibility exists that solid objects or particles may
be sucked into the pump, a strainer should be used on
the suction line.
CAUTION:
Only explosion proof (NEMA 7) solenoid
valves should be used in areas where explosion proof
equipment is required.
CAUTION:
The H25/1600S pump is designed to oper-
ate lubrication free.
CAUTION:
Maximum temperature limits are based
upon mechanical stress only. Certain chemicals will
significantly reduce maximum safe operating tempera-
tures. Consult Wilden's Chemical Resistance Guide
(see publication E-4) for chemical compatibility and
temperature limits.
WARNING:
Prevention of static sparking — If static
sparking occurs, fire or explosion could result. Pump,
valves, and containers must be grounded to a proper
grounding point when handling flammable fluids and
whenever discharge of static electricity is a hazard.
CAUTION:
Do not exceed 8.6 bar (125 psig) air supply
pressure.
CAUTION:
The process fluid and cleaning fluids must
be chemically compatible with all wetted components
(see publication E-4).
CAUTION:
Pumps should be thoroughly flushed with
water before installing into process lines.
CAUTION:
Always wear safety glasses and proper
protection when operating and maintaining pump.
CAUTION:
Before any maintenance or repair is
attempted, the compressed air line to the pump should
be disconnected and all air pressure allowed to bleed
from the pump. Before disassembly of the pump, or
removal from process lines, all pressure must also be
bled from the liquid side of the pump and all fluid
drained into a suitable container. Failure to do so may
result in product under pressure being sprayed on user.
CAUTION:
Blow out air line for 10 to 20 seconds
before attaching to pump to make sure all pipeline
debris is clear. Use an in-line air filter. A 5µ (micron) air
filter is suggested.
CAUTION:
Pump is not rated for UL 79 service.
CAUTION:
H25 pumps are not submersible.
CAUTION:
Tighten all hardware prior to installation.
CAUTION:
All piping valves, gauges and other compo-
nents installed on the liquid discharge must have a mini-
mum pressure rating of 110.3 bar (1,600 psig).
Summary of Contents for Wilden Advanced H25
Page 19: ...TT5178...