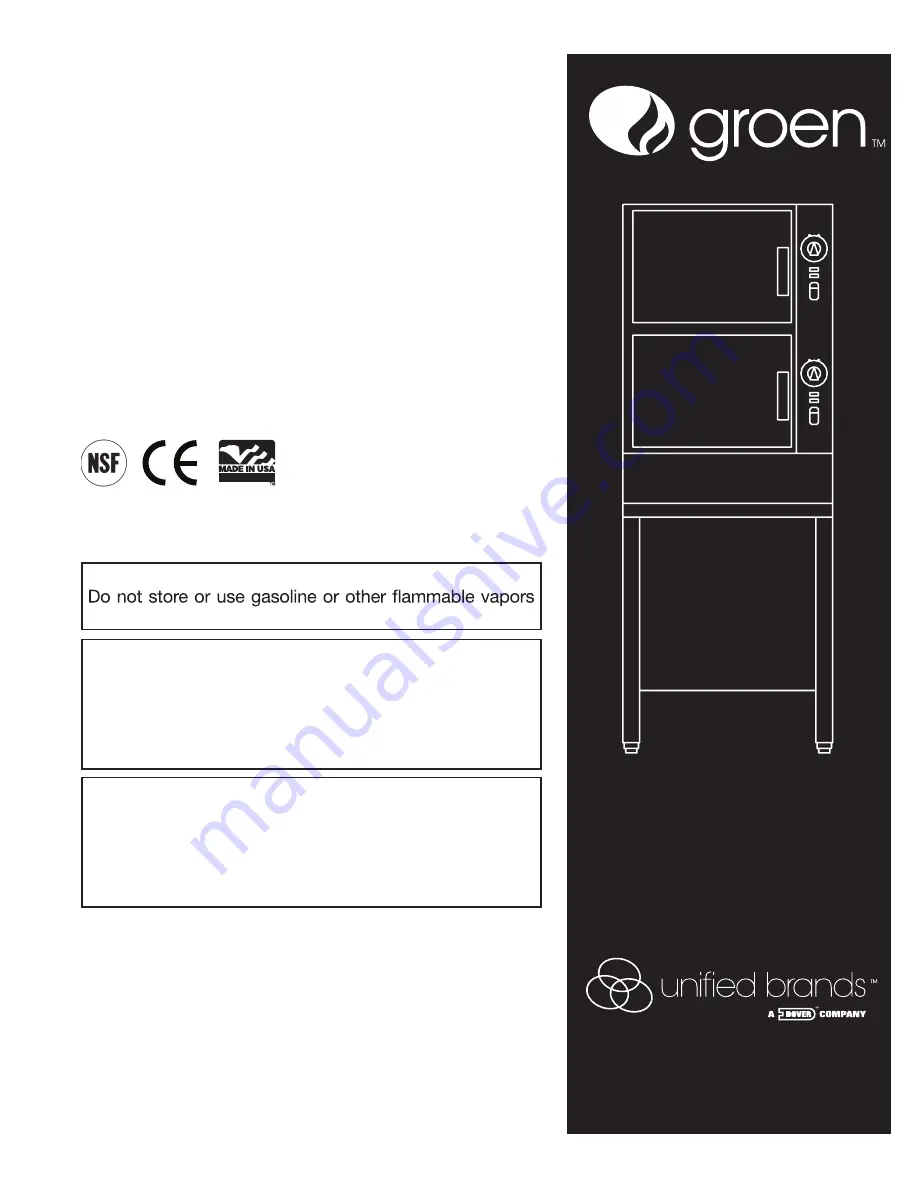
This manual provides information for:
OPERATOR MANUAL
IMPORTANT INFORMATION, KEEP FOR OPERATOR
PART NUMBER 128805 REV G (07/14)
MODEL HY-6G(CE)
HYPERSTEAM™
ATMOSPHERIC
CONVECTION STEAMER
INTERNATIONAL
· Self Contained
· Gas
· Capacity: 6 Steamer Pans (12” x 20” x 2-1/2”)
.
E
C
N
E
R
E
F
E
R
E
R
U
T
U
F
R
O
F
D
E
N
I
A
T
E
R
E
B
T
S
U
M
L
A
U
N
A
M
S
I
H
T
READ, UNDERSTAND AND FOLLOW THE INSTRUCTIONS AND
WARNINGS CONTAINED IN THIS MANUAL.
WARNING / FOR YOUR SAFETY
and liquids in the vicinity of this or any other appliance.
POST IN A PROMINENT LOCATION
Instructions to be followed in the event user smells
gas. This information shall be obtained by consulting
your local gas supplier. As a minimum, turn off the gas
and call your gas company and your authorized service
agent. Evacuate all personnel from the area.
WARNING
Improper installation, adjustment, alteration, service
or maintenance can cause property damage, injury or
death. Read the installation, operating and maintenance
instructions thoroughly before installing or servicing this
equipment.
NOTIFY CARRIER OF DAMAGE AT ONCE
It is the responsibility of the consignee to inspect the container upon receipt of
same and to determine the possibility of any damage, including concealed dam-
age. Unified Brands suggests that if you are suspicious of damage to make a
notation on the delivery receipt. It will be the responsibility of the consignee to file
a claim with the carrier. We recommend that you do so at once.
Manufacture Service/Questions 888-994-7636.
Information contained in this document is known to be current and accurate at the time
of printing/creation. Unified Brands recommends referencing our product line websites,
unifiedbrands.net, for the most updated product information and specifications.
1055 Mendell Davis Drive
Jackson, MS 39272
888-994-7636, fax 888-864-7636
unifiedbrands.net
Summary of Contents for Unified Brands Groen HyperSteam HY-6G
Page 25: ...OM HY 6G CE 25 Electrical Schematic ...
Page 41: ...OM HY 6G CE 41 ...
Page 42: ...42 OM HY 6G CE ...
Page 43: ...OM HY 6G CE 43 ...