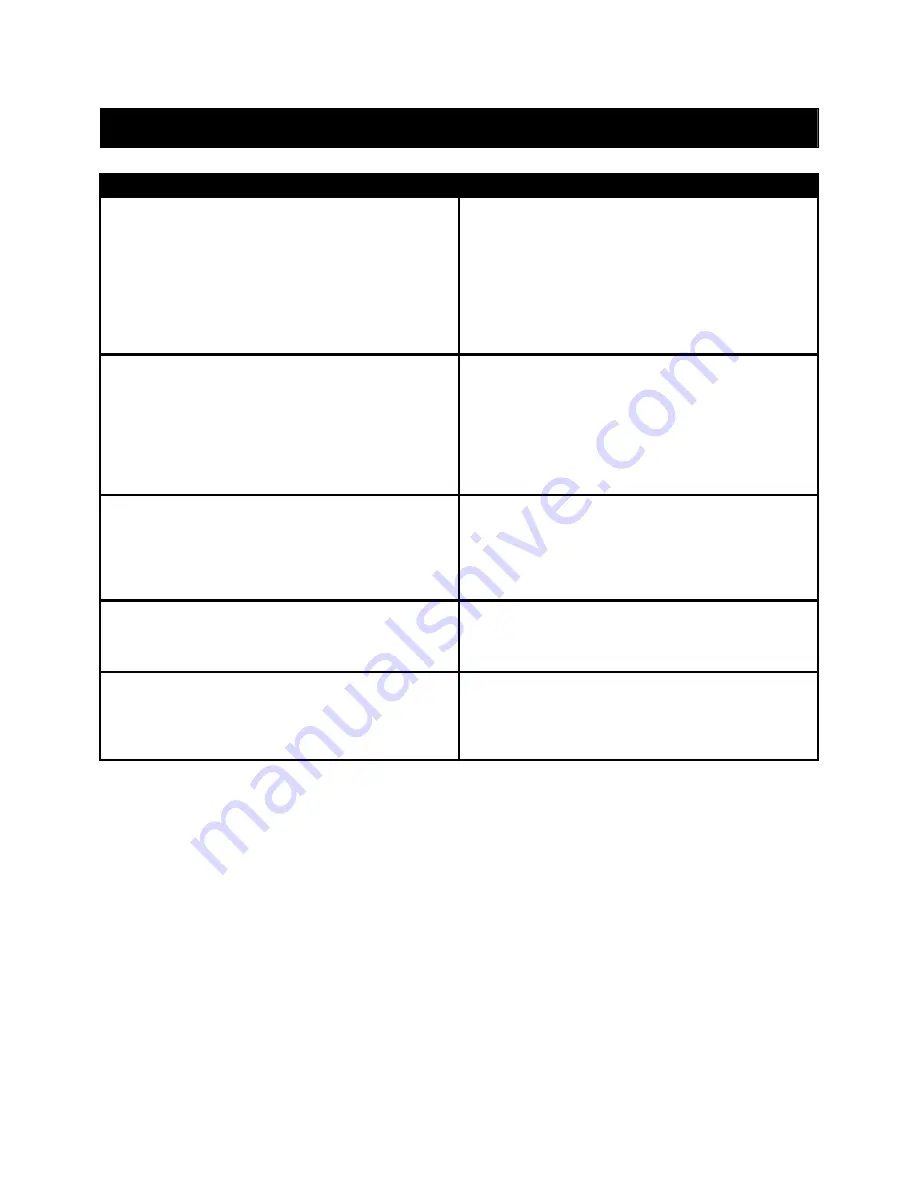
23
TROUBLESHOOTING
FAILURE
PROBABLE CAUSE
Winch won’t hold load.
a) Excessive
backpressure in the system. Check
the system for restrictions and reduce the
backpressure.
b) Brake discs are worn out. Replace brake
discs.
c) Winch clutch is slipping. Inspect the clutch and
driver for wear and replace worn parts.
Winch will not raise the load it should.
a) Relief valve setting may be too low to allow
proper lifting. Increase relief valve pressure
setting.
(Note: Do not exceed recommended
system pressures)
.
b) Load being lifted may be more than the winch’s
rating. Reduce the load or re-rig to increase
mechanical advantage.
Oil leaks from vent located on the top of the
gearbox.
a) The motor shaft seal may have failed. Replace
this seal and reduce backpressure if that
caused the shaft to fail.
b) Brake piston seals may have failed. Service
the brake section and replace worn parts.
Winch runs too slow
a) Low flow rate. Check the flow rate and
increase if necessary.
b) Hydraulic motor worn out. Replace the motor.
Cable drum won’t free spool
a) Winch not mounted squarely. Check mounting
and confirm that the winch is mounted on a
level surface.
b) Clutch not disengaged. Disengage the clutch.
Summary of Contents for RUFNEK 100
Page 10: ...10 CLUTCH INSPECTION...
Page 27: ...27 VISCOSITY CHART...