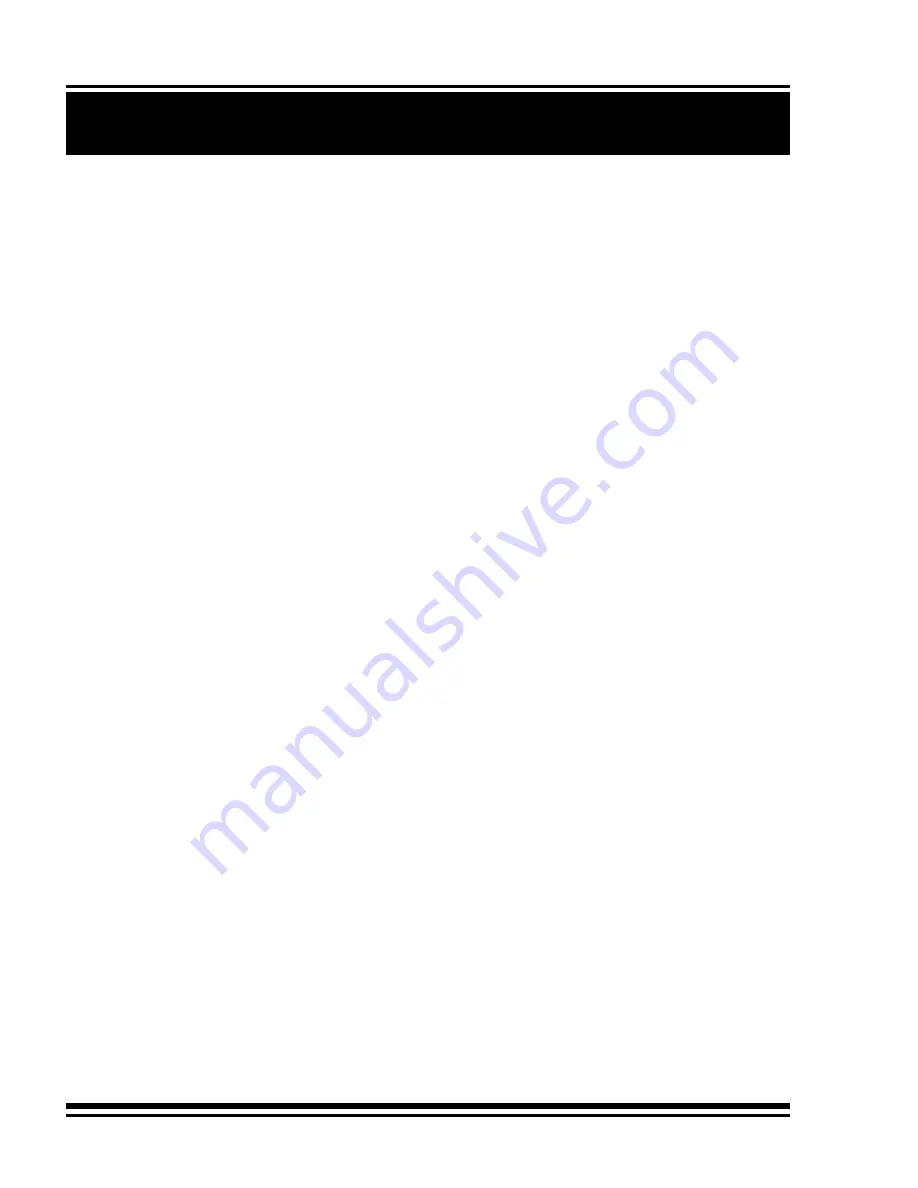
PAGE 2
338 REV.031001
The PULLMASTER Planematic drive is a high performance, highly efficient, planetary hydraulic drive with
reversing speed 4.3 times faster than forward speed.
The main components of this unit are:
✛
hydraulic motor
✛
brake housing
✛
hydraulically released multi-disc brake with static and dynamic function
✛
primary planetary reduction
✛
final drive housing
✛
final planetary reduction
✛
output shaft
FUNCTION IN FORWARD ROTATION:
In forward rotation the torque and rpm of the hydraulic motor are transmitted to the sungear of the primary planet
reduction. The sprag clutch which connects the motor drive shaft to the automatic brake assembly permits free
rotation in forward direction* (brake is not effective in forward direction).
The output torque and rpm of the primary reduction are transmitted to the final reduction by the final sungear which
is splined to the primary planet hub. The output shaft is splined to the final planet hub. When the rotation is
stopped, the suspended load or the tension in the reverse direction causes the sprag clutch to lock and the
maximum permissible load is held safely by the disc brake. The pressure required to rotate the output shaft may
vary up to 200 psi (14 bar) without load.
* With the exception of models supplied with brake effective in both directions, brake assembly permits free
rotation in forward direction.
FUNCTION IN REVERSE ROTATION:
In reverse rotation, hydraulic pressure from the reversing side of the hydraulic motor is channelled to the brake
piston, causing the brake piston to release the multi-disc brake against the brake springs. The sprag clutch locks
motor drive shaft with the connecting shaft. Connecting shaft coupled with brake hub and primary internal gear
causes the primary reduction to rotate at the rpm of hydraulic motor, thus eliminating the primary reduction.
Elimination of primary reduction in this manner increases the output shaft speed and decreases the output torque
4.3 times of forward direction. Based on standard motor, pressure required to rotate the output shaft, without load
depending upon speed, may vary from 450 to 750 psi (31 to 52 bar).
If the applied load drives the Planematic faster than desired, the motor consumes more oil than is supplied and
pressure at the reversing port decreases. The brake partially applies and slows the drive. In this manner, the motor
continuously regulates brake pressure to safely and smoothly control the load without counterbalance or holding
valves.
The partially applied brake results in temperature. This temperature is dissipated by an internal circulation flow,
supplied out of the hydraulic motor or from an external source. For models with external circulation, required flow
is approximately 4.5 (US) gpm (17 l/min). The circulation return line must go to the reservoir directly.
IMPORTANT:
For proper drive function, system back pressure in the brake housing and at the motor return
port must never exceed the allowable limits listed in the SPECIFICATIONS section of this
manual.
DESCRIPTION OF THE MODEL PH50