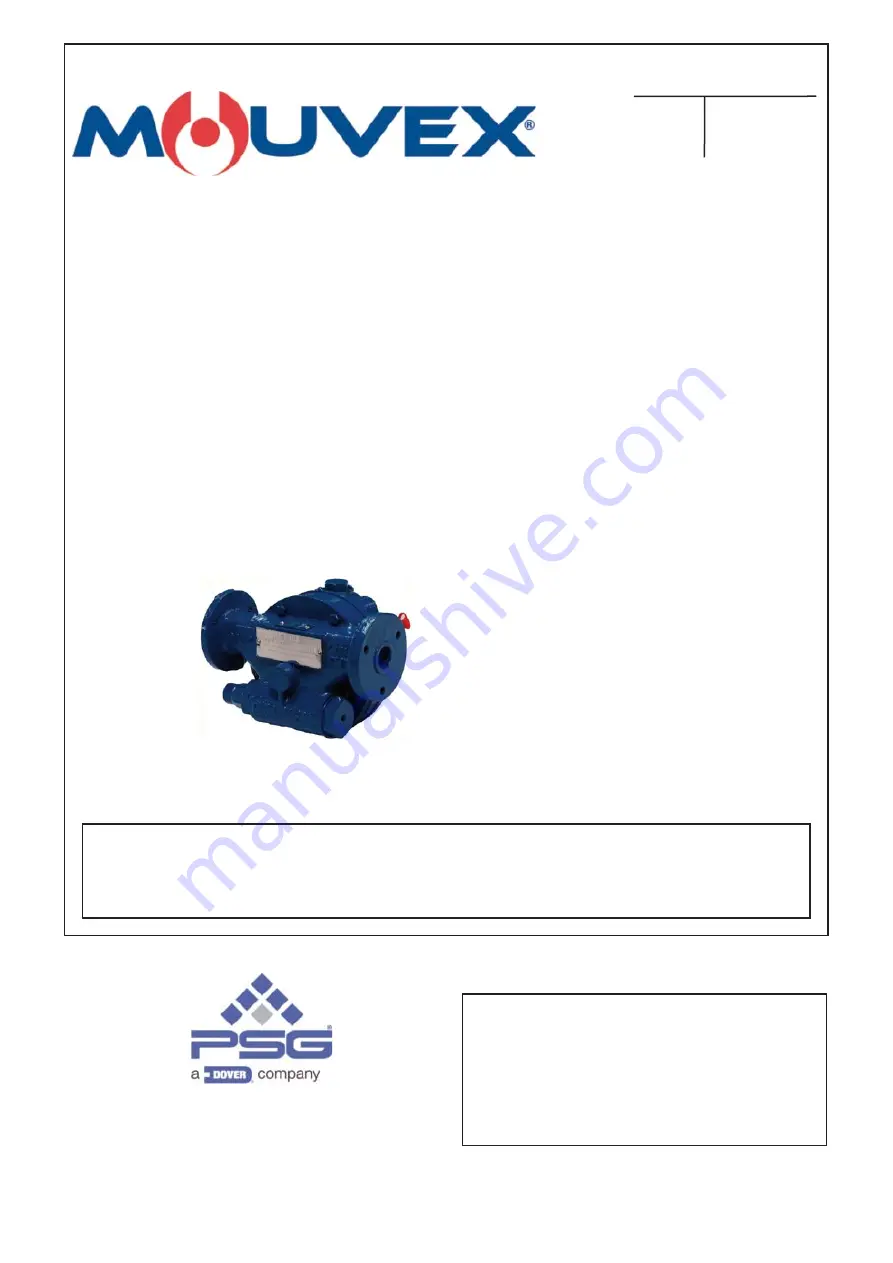
AZ PUMP
Construction O
INSTALLATION
OPERATION
MAINTENANCE
INSTRUCTIONS 1003-A00 e
Section 1003
Effective September 2018
Replaces May 2017
Original instructions
Your distributor :
Z.I. La Plaine des Isles - F 89000 AUXERRE - FRANCE
Tel. : +33 (0)3.86.49.86.30 - Fax : +33 (0)3.86.49.87.17
[email protected] - www.mouvex.com
WARRANTY :
A Series pumps are covered 24 months by warranty within the limits mentioned in our General Sales Conditions.
In case of a use other than that mentioned in the Instructions manual, and without preliminary agreement of MOUVEX,
warranty will be canceled.